Online or wireless vibration analysis is easy to set up and is helping manufacturers during the Covid-19 emergency, says PCMS Engineering reliability consultant James Frank.
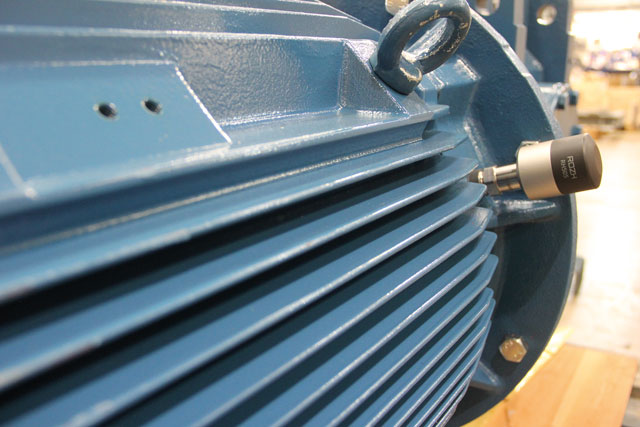
An effective condition monitoring programme can reduce unplanned machine downtime, improve safety and increase machine performance, with a small investment often leading to significant savings.
Faults such as imbalance, misalignment and bearing wear can be identified through vibration analysis, enabling maintenance and repairs to be planned.
Most vibration monitoring programmes rely on a dedicated vibration engineer with a handheld data collector visiting each machine in turn to gather the data, which can be cost-effective initially but has several drawbacks. There is no indication of the health of the machine between scheduled visits, so opportunities to repair the machine could be missed. And assets where access is restricted for safety reasons or by the movement of the machine cannot form part of the condition monitoring programme.
Moreover, in these uncertain times where social distancing has become a necessity, maintaining a route-based vibration analysis programme has become almost impossible.
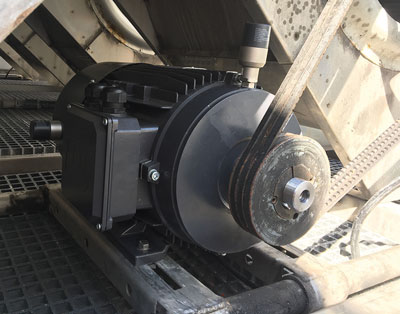
Many companies are turning to wireless monitoring systems – such as the Ronds RH560 used by PCMS – because they provide alerts when there is a change in machinery vibration or temperature, without an engineer having to attend site to collect the data. Such monitoring systems are allowing maintenance managers to track the health of their machines from anywhere, with new data being received every 1-8 hours.
A typical wireless monitoring kit consists of a mounted data collector or gateway which receives and processes the signals from several vibration and temperature sensors. Some manufacturers are able to achieve a sensor transmission range of up to 300m, meaning that many assets can be covered by a single gateway.
The data is then transferred to a server or network via one of the many different connectivity options. Wi-Fi or LAN can be used to integrate with a company’s existing IT system, while connection using a 4G option allows the data to be stored on a remote server. This can be configured before delivery, making the system an out of the box solution capable of monitoring assets within an hour of the kit being received. It also means that the data can be accessed and analysed from anywhere.
Single axis and tri-axial sensors are available, with many collecting temperature and vibration values simultaneously. They are easy to install – they can be mounted using threaded studs, magnets or adhesive, so they can be retrofitted to machinery of any age, and have an average battery life of two years.
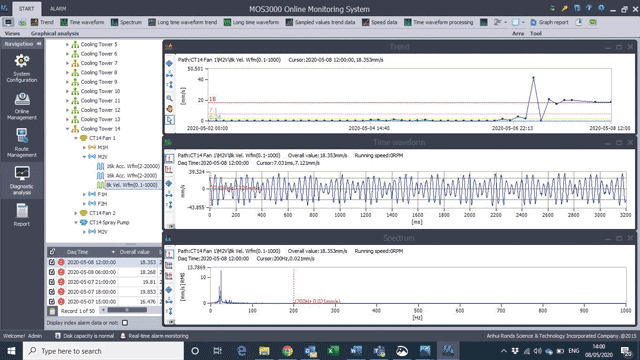
Many of the latest systems offer full analysis capability including trends, spectra, waveforms and more advanced analysis techniques such as enveloping for early identification of bearing faults.
The fully customisable collection settings make sure that the correct frequency range and data resolution is being collected to cover every possible failure mode for each machine type, and most have the facility to set alarms which will trigger emails and text alerts to give the maximum warning of a change in machinery condition.
The benefits of installing a wireless system were recently seen on a rail-mounted cement delivery skip in a precast concrete factory in the UK. The client mounted wireless sensors on the motors and drivetrains throughout the delivery system, which was suspended in the factory roof.
The wireless system indicated an increase in vibration, and a subsequent inspection found that a chain tensioner had snapped, allowing excess movement of the drive chain. It was estimated that if this had been allowed to fail it would have resulted in lost production costs of £120,000.
A wireless monitoring system can be fitted to almost any machinery type, although it makes sense to keep an eye on the assets where failure has the biggest cost or safety implications. It’s worth considering what machines in your workplace would benefit from condition monitoring.
james.frank@pcmseng.co.uk | www.pcmseng.co.uk
Tel Office: 01709 876712 | Tel Mob: 07891 859467