Ford is making ventilator subassemblies for the NHS in the UK after transforming an empty warehouse into a manufacturing plant in record time.
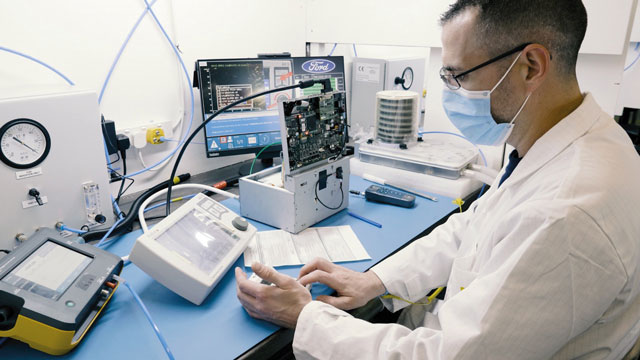
Employees worked non-stop for three weeks to get the high-tech production line into operation – a feat that would usually take a full year. Ford is part of the VentilatorChallengeUK Consortium – a collaboration between leading technology and engineering companies to make 15,000 Penlon Prima ES02 ventilators for the NHS to use for critically ill COVID-19 patients.
“It took many late nights and a lot of hard work, but the ingenuity and commitment of our people has been just remarkable, and it shows how a crisis can bring out the best in us,” said Ford of Britain chairman Graham Hoare. “The way they have sacrificed time with their families and been willing to learn something new to help build these life-saving devices is testimony to their desire to deliver, and it makes me very proud to be part of this team.”
Converting a warehouse at the company’s Dagenham Engine Plant into an ISO9001 accredited site required the team to adapt existing equipment and quickly establish a production line for component boxes and 8.4-inch remote display screens that are key parts of the fully assembled units.
3D printing processes were employed to make components for 200 workstations – which adhere to social distancing requirements – for the Ford volunteers who include operators, product coaches, technicians and engineers from a range of departments. In total, at full production, more than 650 people will work in three shifts at the plant.
Ford is part of the consortium executive, which includes Airbus, McLaren, Penlon and Siemens. To collaborate on a daily basis with Penlon, located in Oxford, the Ford team is using HoloLens 2 virtual reality headsets. These allow remote technicians and specialists to view the perspective of the HoloLens wearer on a computer screen and provide real-time guidance and information, seen as holograms in the wearer’s field of view.
Dagenham Engine Plant manager Martin Everitt said: “There’s no hierarchy in a time of crisis. People just work together for a common goal. By working closely with Penlon and medical practitioners, we quickly bridged the gap to go from making engines to making ventilators, and together with our partners in the consortium we’re now producing a device that’s normally made in small quantities by the thousand.”
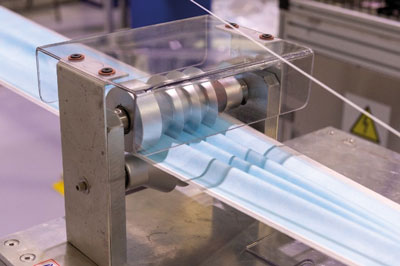
Project Apollo
Ford is also helping to reduce the spread of COVID-19 with Project Apollo, the company’s global effort to produce personal protection equipment and increase the availability of ventilators and respirators.
The company’s Research and Innovation Center in Aachen, Germany, recently assisted with the development of a new powered air-purifying respirator for healthcare professionals, being produced at the company’s Vreeland facility near Flat Rock, Michigan.
The respirator includes a hood and face shield, while a battery operated ventilator and a high-efficiency filter system provides a supply of 99.97 % filtered air for up to eight hours. The engineers who worked on Ford’s interior air advanced filtration system provided expertise in the filter design and testing to develop the clinical grade filter used in the respirator.
The company is producing protective face masks and shields as part of initiatives to provide a safe working environment for employees performing essential roles at Ford sites during the COVID-19 crisis.