Manufacturing industry is rising to the challenge of the Covid-19 epidemic, with a range of companies offering different approaches to the shortage of ventilators and a new hand sanitiser plant coming on stream in under 10 days.
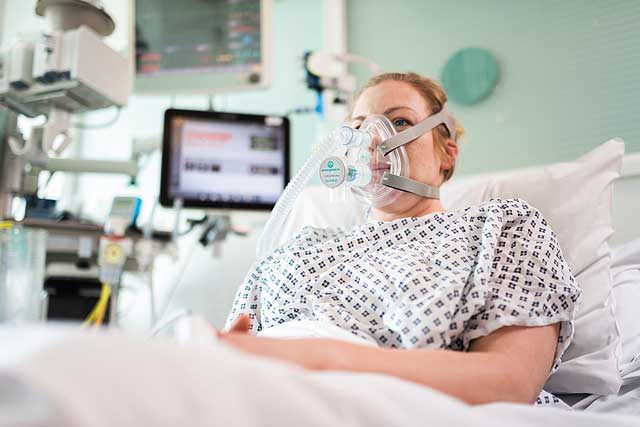
Ineos hit its own 10-day target to build the sanitiser plant at Newton Aycliffe, County Durham. The plant went into production in the last week of March, working three shifts around the clock. It will produce a million sanitisers a month.
It began issuing the products free to the NHS at the end of the month. As well as helping to meet the needs of frontline medical and care services, the plant will make pocket hand sanitisers for personal use, to World Health Organization specifications.
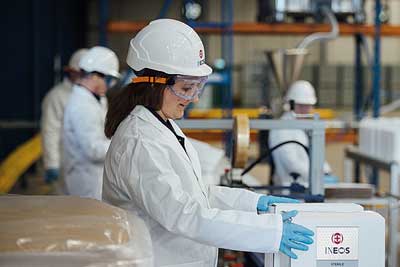
Ineos is the leading European producer of the key raw materials for sanitisers, isopropyl alcohol and ethanol. The company is running its plants flat out and has been diverting more of the product to essential medical use.
Last month the government issued a call for manufacturers who could provide support in the supply of ventilators and ventilator components as part of the response to the virus, as well as businesses with skills in design/specification, rapid prototyping, product assembly and certification/regulation/testing.
Three consortia had won orders from the UK government for ventilators by the end of March. Ventilator Challenge UK will step up production of existing designs from Smiths Group and Oxfordshire-based Penlon. The government ordered 10,000 units from the consortium, which includes Airbus, BAE Systems, Ford, and a number of Formula One teams and is chaired by Dick Elsy, chief executive of the High Value Manufacturing Catapult.
Dyson, which has developed an all-new design, has also won orders for 10,000 ventilators, though its model will need regulatory approval.
Mechanical engineers at UCL and clinicians at UCLH, working with Mercedes-AMG High Performance Powertrains, have developed a breathing aid designed to keep patients out of intensive care. The continuous positive airway pressure device, or CPAP, took fewer than 100 hours from the initial meeting to production of the first device. It has been recommended for use by the Medicines and Healthcare Products Regulatory Agency. 100 devices are to undergo clinical trials at UCLH, with the aim of rapid introduction in hospitals.
Meanwhile the CBI said that there had been confusion arising from the status of manufacturing – it is not included in the list of businesses ordered to close (mainly retail and leisure establishments) by the government but its employees are not considered “key workers”. It said that there had been diverging advice from the UK government and the devolved administrations in Scotland, Wales and Northern Ireland, and called for a consistent approach from governments, regulators, enforcement agencies and the police.
A CBI webinar heard reports of manufacturing workers on their way to work, and vehicles making deliveries, being stopped by the police. The CBI and Make UK both recommended companies could help by issuing employees with letters to state that their employer is not one of the businesses that the government has required to close; their workplace remains open; they cannot work from home due to the nature of the business or their role; and they are required to travel to work. Make UK has provided a template on its website www.makeuk.org/news-and-events/news/2020/03/25/covid-19-furlough-letter-to-employee
CBI advice to companies was that they should adapt workplace setups and practices to meet the Covid-19 safety measures, including enforcing the 2m distance rule. They should demonstrate compliance with the government guidelines and be open about the changes being introduced. Companies should involve unions and listen to the concerns of the workforce, who might also come up with solutions.
The HSE is issuing regular bulletins and guidance on workplace safety – see www.hse.gov.uk/news/coronavirus.htm?utm_source=sendinblue&utm_medium=email&utm_campaign=coronavirus&utm_content=hse
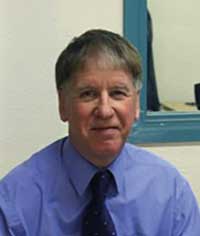
Harmill Systems – an SME’s story
Harmill Systems, a manufacturer and installer of access and other equipment (including dust extraction systems) used in rail maintenance and in other industries, is managing to keep production going but is unable to deliver its products.
The company has turnover of around £2m-£3m and a workforce of 26, of whom around a third are office-based design and admin staff, with the remainder engaged in manufacture and installation. Managing director Patrick Hughes said installation has come to a halt because clients are not granting access to their sites except for emergency maintenance, so about half the non-office staff staff are on furlough, with emergency calls being handled by the company’s directors.
So far the company has been able to get delivery of steel and other materials (though nuts and bolts are becoming difficult to obtain) and production is continuing. “The difficulty is we can’t deliver the finished products to site, so sooner or later we’re going to run out of space,” said Hughes.
At the heart of the company’s manufacturing operations are six 6m2 welding bays where individual welders can work safely. A rota system has been introduced for using the canteen to maintain social distancing. Keeping the 2m distance generally has proved the biggest challenge, said Hughes. Around half the design staff are working from home, on a rota system because some are needed on site to manage the manufacturing side, and admin staff are also working from home.
Employees have not experienced any difficulty in travelling to work.
For now, apart from space, cash flow is the biggest potential concern. Because the company can’t deliver completed orders it is not being paid. Meanwhile it is still paying the wages of the furloughed staff, until the government scheme comes into action.
“We’re lucky that we can keep going for now,” said Hughes, “but there’s no way of telling when this is going to end.”