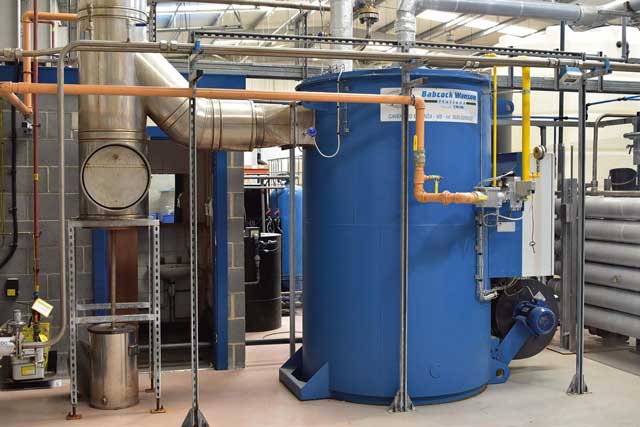
The world’s first 1MW gas fired supercritical water heater has been produced by Babcock Wanson for use in nanomaterial production. Chris Horsley, director of Babcock Wanson’s process engineering division, has the details
Nanomaterials specialists Promethean Particles has built the world’s largest continuous multi-material nanoparticle manufacturing plant, producing in excess of 1000 tons per year (up to 200 kg of nanoparticles per hour) .
The company, based in Nottingham, was established in 2007 following a spinout from Nottingham University, based on the research of Professor Ed Lester of the university’s chemical engineering department).
Promethean Particles designs, develops and manufactures inorganic nanoparticle dispersions to customers’ specifications. It covers many industries’ needs such as printed electronics (enabling flexible circuitry, 3D printing and so on), nanocomposites, catalysts, metal organic frameworks (MOFs), healthcare (for artificial bone), scratchproof coatings and flame-retardant materials, to name but a few. It is able to produce thousands of different nanomaterials, with a wide degree of control of factors such as particle size and morphology.
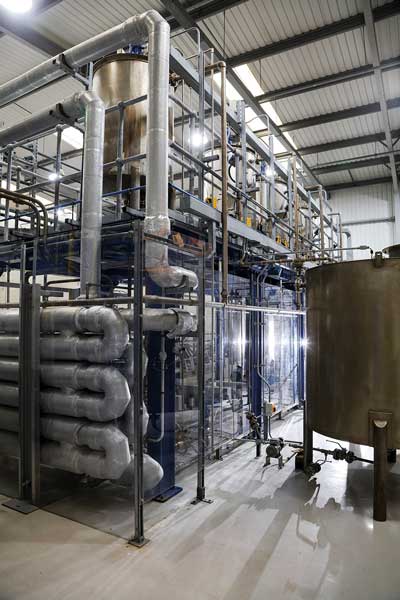
Its unique reactor design allows for continuous (as opposed to batch) production and flexibility, enabling it to produce a huge variety of materials. The flexibility is largely down to the wide temperature range achievable with its process, which is important as there is a correlation between the temperature and particle size – large size particles require a higher temperature. For example, high temperatures are required for zirconia, whereas lower temperatures are necessary for MOFs (too much heat and the organic component breaks down).
The patented technology also reduces costs and the need for natural resources by using less material in the solution, whether this is a metal, mineral or other substance.
A bespoke TPC SW 1MW gas-fired supercritical water heater produced by Babcock Wanson is an integral part of the process. It has been designed for a maximum working pressure of 275 bar at up to 490°C.
Babcock Wanson was one of a handful of manufacturers approached by Promethean Particles, and the only one to provide a suitable solution. The heater is based on a Babcock Wanson TPC 1000B, but with very special inners and controls. For the bespoke heater Babcock Wanson designed and manufactured a specially wound continuous coil assembly to form the main heating surface using 9mm thick wall ASI 321 stainless steel, as opposed to the usual 4mm carbon steel for a standard industrial water heater. The bore of the tube is very small. This material and thickness were chosen to meet the pressure and temperature demands of the process to be able to produce supercritical water in normal operation at up to 250 bar and 450°C.
Challenges included designing the heater with the ability to accept variations in water flow (between 600-3000 kg/h per hour) and heat input within quite wide parameters; developing specialist welding techniques to cope with the material and the design pressure required; and specifying and installing specialist instruments and controls to work at these temperatures and pressures.
The heater took seven months to design and build. The combustion system, control scheme and software were designed in-house by Babcock Wanson. Relevant mountings, safety valves, pressure controllers and differential controllers were sourced and fitted in-house to enable Pressure Equipment Directive approval. A hazard and operability study (HAZOP) was carried out between Babcock Wanson and Promethean engineers to review the controls and integration with the site control SCADA system.
Return fluid heat recovery limits the final temperature rise of the heating fluid to 90°C. The inlet process heat recovery exchanger process brings the water up to 360°C at nominally 270 bar, with the TPC SW heater adding the final 90°C to reach the required supercritical condition.
The supercritical water is then pumped into the reactor at the same time as the precursor where it mixes to form the product. The product leaves the reactor through a specially constructed section at 350°C. It then goes through a heat exchanger to cool it down, and the pressure is reduced before passing the product into a holding tank. Depending on the product, further processing may then be required.
The entire process is controlled by sophisticated software and it is encased in a toughened casing for safety.
Promethean Particles production engineer Lewis Neve said the project went very smoothly: “The heater is running as expected. Babcock Wanson knew what they were doing and were very easy to work with.”
For more information, please contact 020 8953 7111
info@babcock-wanson.co.uk | www.babcock-wanson.co.uk