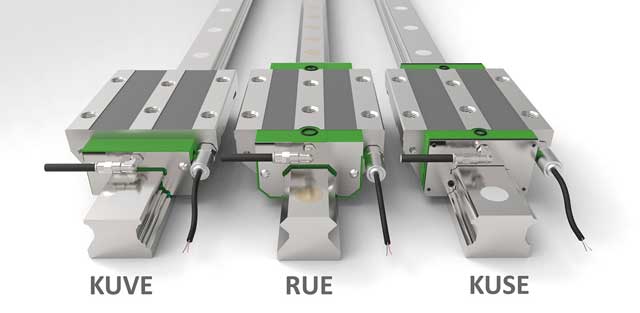
Automated relubrication offers longer machine operating times and reduced maintenance costs, says Joachim Bockenheimer, Schaeffler product manager for linear systems and sensors.
Certain items of auxiliary equipment are put into operation and then forgotten about, including lubrication systems. If no unexpected failures occur, the lubrication intervals and lubricant quantities that were initially defined generally go unquestioned. In this context, a requirements-based lubricant supply offers enormous potential for extending machine operating times and reducing maintenance costs.
The Schaeffler DuraSense offers such a system for Schaeffler’s linear guideway assemblies.
Linear guides are main components used in machine tool and handling systems, for example. Because linear guides are very sensitive to lubrication, monitoring of this parameter is very important.
Analysis of failures of linear guides shows that a considerable proportion are related to lubrication. That doesn’t necessarily mean that the guides haven’t been lubricated at all; it means that they haven’t been lubricated according to the recent conditions in the application. Relubrication intervals are influenced by load, speed, stroke and contamination of an application. Changing conditions require adjusted lubrication settings.
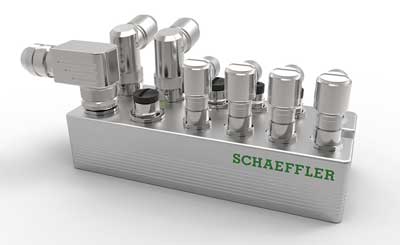
A linear axis typically consists of a number of guide rails with several carriages. With the DuraSense system, each carriage can be equipped with one sensor, providing individual monitoring of each carriage. A pre-processing unit (PPU) allows up to seven sensors to be connected per axis for monitoring the lubrication conditions of each guide carriage. The sensors gather intelligence on the quality of the lubricant inside the carriages by analysing the vibration modes of the carriages. The lubricant quality is expressed through the lubrication variable, which is checked against a threshold value. This threshold is deduced from a reference run of the linear axes under specific conditions.
The detection of the actual lubrication variable is carried out under identical conditions to the reference run. Once the threshold limit has been reached, a signal is triggered by DuraSense, which can be used with a central automatic lubricator to trigger relubrication. In simpler cases, a red light alert can be triggered followed by manual relubrication.
After relubrication and a short time of running, the lubrication variable will normally drop back to an acceptable level from where, under continuous use, it will rise towards the threshold again. If, after relubrication, the lubrication variable does not drop, this indicates a malfunction of the lube line. This means DuraSense will not just monitor the quality of the lubricant inside individual carriages but will also see if the grease delivered by a central lubrication unit actually ends up inside the carriage. If the lubrication variable does not drop, this may indicate a jammed or loose grease hose.
Suitable lubrication systems include Schaeffler products such as the CONCEPT2 and CONCEPT8 automatic lubricators, as well as other central lubrication systems.
With DuraSense, lubricating impulses can be triggered in two ways. The first is for the pre-processing unit to deliver 24V trigger signals for each of the seven channels. The 24V outputs can be connected both to the relubrication units and the machine control system.
The second option allows the lubrication variable to be emitted as a 4-20mA signal for each of the seven channels. This enables the user to continuously monitor lubrication conditions and to adjust the relubrication function with even greater flexibility. The signal can even be used for further analysis such as the calculation of the remaining bearing life.
Manifold benefits with a simple system design
With DuraSense, both insufficient lubrication and over-greasing are reliably prevented, resulting in lubricant savings of up to 30% achieved at optimum load, as well as reducing the number of failures caused by contamination.
DuraSense reliably monitors the lubrication conditions of each individual carriage in linear axes. Relubrication only occurs when it is needed and in the right volumes, so there is no risk of overgreasing. This in turn means a cost reduction for operating supplies, which also helps preserve resources and the environment. The system also verifies that the lubricant actually reaches the carriages. Individual monitoring of each carriage means that any problems such as a loose grease hose can be located easily.
Another benefit is higher machine availability due to less unplanned downtime, which in turn results in reduced maintenance costs and higher productivity.