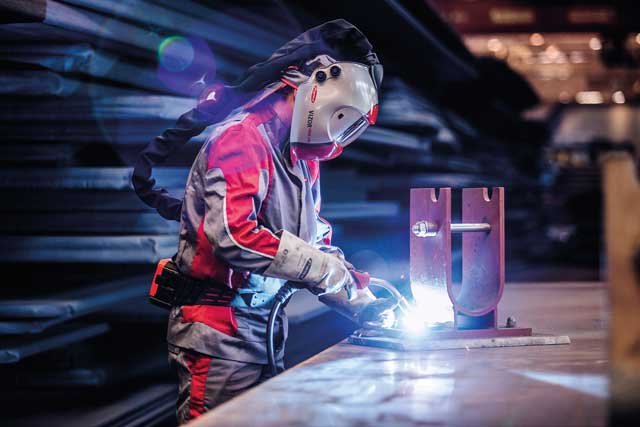
Make sure you comply with tightened enforcement expectations on welding exposure, say Lee Parkinson, Fronius UK head of technical support (national), and Kieren Hebborn, Impact Technical Services LEV design and installation manager.
In February last year, the Health and Safety Executive strengthened its enforcement expectation for the control of exposure to mild steel welding fumes. These were already known to contain manganese, which can cause neurological effects, and are now proven to cause lung cancer.
The reclassification of mild steel welding fume as a human carcinogen comes after the International Agency for Research on Cancer concluded that exposure can scientifically be linked to lung cancer, with some evidence that additionally links it to kidney cancer. As general ventilation is not adequate for achieving the levels of control necessary to lower these risks (in fact there is no known safe level of exposure), the HSE has set out the latest measures it expects all employers to follow to reduce exposure to airborne contaminants when welding is taking place.
Leicester-based Impact Technical Services supplies systems and services for the control of fumes in the workplace. It advises that employers and staff alike should take the HSE’s advice very seriously, especially employers who are responsible for implementing fume control measures and could face heavy fines if found not to be protecting employees.
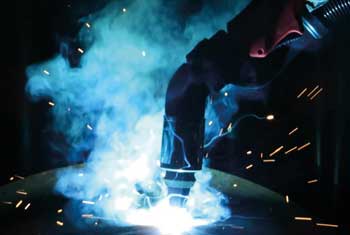
Local exhaust ventilation (LEV) is the most commonly recommended form of control because it removes the hazardous airborne carcinogens from the working environment. A reputable supplier will assess and advise of the most effective LEV method for a given application, taking factors such as the number of welders and how often the tasks are undertaken into consideration.
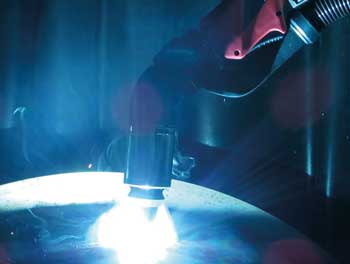
LEV products include many types of hoods and extraction products that can be used to effectively remove fumes at the source. Smaller hoods are available for individual use, as well as large pivoting hoods to extract fumes from a large working area. Downdraught benches are a popular selection for welding as they provide a high level of extraction across a large working area, with fumes being extracted both from the back wall and underside of the bench.
Once an LEV system or product has been installed, it will be commissioned and users will be given training, a logbook (to record regular checks) and a parts list (including filter type used). Airflow indicators are a recommended addition, to continuously monitor the effectiveness of the system and to enable the user to see quickly if there is a blockage or problem with the system.
Where the use of a hood requires frequent manoeuvring to the point that it interrupts the job, fume extraction torches are an alternative, in which extraction occurs from the source of the fume in all welding positions. Austrian manufacturer of welding products, Fronius, produces both lightweight and ergonomic fume extraction torches and torch attachments.
To offer further protection against inhalation of toxic fumes and ultra-fine particles when welding for any length of time, but particularly for regular (daily or weekly) welding or high-intensity indoor welding, local exhaust extraction or on-torch extraction can be doubled up with respiratory protective equipment (RPE). This is especially useful when completing long lengths of weld where the fume capture requires continuous repositioning and therefore may not adequately control all fume exposure.
RPE can also be more suitable for outdoor welding. It often comes in the form of a welding helmet with inbuilt respirator, for example the Fronius Vizor 4000 or Vizor Connect Air/3, a powered air purifying respirator with long battery life complete with a fully automatic welding visor. This system is certified with the highest filter quality THP3, filtering out more than 99.8% of particles. The respirator system distributes the air flow optionally between mouth and forehead.
For Fronius and Impact Technical Services as manufacturers, the new classification by IARC emphasises the requirement to continue to improve and develop new approaches and systems to keep welders’ exposure to fume to a minimum. We highly recommend visiting www.hse.gov.uk to ensure you are complying with the latest regulations concerning welding fume control, including thorough examination and testing of the systems in place. Let’s all go home healthy!
Fronius UK 01908 512300
info-uk@fronius.com | www.fronius.co.uk
Impact Technical Services 0116 2448855
enquiries@impactts.co.uk | www.impacttechnicalservices.co.uk