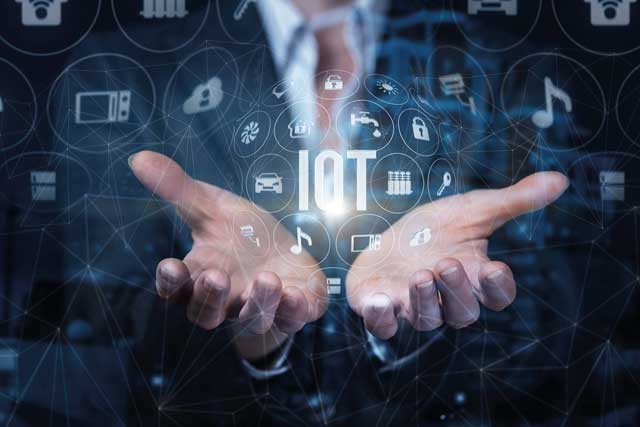
A new era in which asset data quality drives performance is at hand, says James Dunnett, IT director of facilities management company Emcor UK.
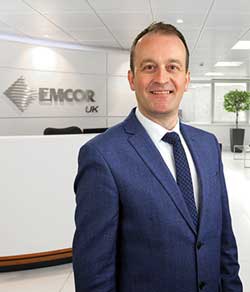
Data quality is the bedrock for effective asset management. However, often datasets miss valuable asset information. Experience at Emcor UK shows that in taking on a new contract, computer aided facilities management (CAFM) systems often omit as much as 40% of the available asset data, a shortfall that can only be corrected by a full asset survey. Inaccurate or inconsistent data can pose compliance problems, which can risk financial or operational penalties.
In circumstances like this, it is important for companies to adopt processes that will enable them to collect, refine and filter data. In that way they will be able to retain up to date asset and maintenance data, helping make sure that that plant managers have the information needed to make the best possible decisions.
In order to address these issues, it is essential to create a set of data quality standards for all key facility management activities. For example, it is now possible to measure the accuracy and completeness of asset data in real time, grade it and highlight exceptions or errors, enabling users to correct shortfalls and drive up quality.
Systemised asset maintenance
One of the principal and constant challenges for providing compliant asset management is the need to keep pace with legislative changes. The adoption of condition-based maintenance and business-focused maintenance can also create problems for facilities operators. In general, Emcor UK’s experience of working with highly complex estates shows that maintenance approaches are rarely substantially amended more than twice a year. Fortunately, by implementing systemised tools to make these changes, backed up with reliable data, plant managers can dynamically, accurately and quickly modify maintenance strategies.
Emcor UK has developed a set of bespoke software tools that are able to update maintenance regimes over an entire asset portfolio or building in a few clicks of a mouse. By taking this systemised approach it is possible to quickly and accurately make changes and evaluate their impact before they are applied. This provides the ability to change maintenance regimes daily if required, instead of every six months.
Understanding business drivers
Establishing a collaborative relationship with key stakeholders is essential for facilities management service providers and asset management consultants to fully define the desired business outcomes of a plant. Understanding this will also enable them to define the importance of each asset, or asset system, and establish hierarchies in order to highlight single points of failure or high risk resources that support critical business operations. Once these risk bottlenecks have been identified it is possible to deploy appropriate strategies to reduce the risk.
A key theme for all progressive organisations is making sure that the right people have the right systems and information to help make informed decisions. Presenting data in clear, concise and innovative ways rather than a flat, uninspiring spreadsheet adds real business value. Equally, analysing data isn’t the job of a few. All key stakeholders need to be able to analyse data with minimal effort to present their findings to their peers.
A holistic approach to data aggregation
Plants are increasingly data-rich due to the range of available information sources such as CAFM, BMS, smart assets, web services (such as weather reports) and IoT sensors. However, the resulting data sets are typically kept in separate ‘silos’, and any insights have a narrow focus.
To establish a successful approach to asset management it is essential to aggregate analytics for all the data elements. For example, it is possible to decide if a chiller unit needs replacing based on its age and replacement cost (from the CAFM), the utilisation of the locations it serves (from IoT) and how much power it is drawing (from the BMS). This holistic approach is integral to any forward looking facilities solution.
The era of predictability
Machine learning and artificial intelligence are key technical capabilities which are having a huge impact on the way assets are maintained. For instance, AI excels at spotting patterns in big datasets. This is especially useful for facilities management providers that have many years of high quality asset performance information, because AI can been used to create predictive models that forecast an asset’s performance over time. Calculating an expected asset failure in the next month, or forecasting its condition in three years, is possible with a high degree of accuracy.
Introducing these new technologies is heralding the dawn of a new era of predictable asset management. This will allow for optimised and dynamic asset management strategies to be deployed, balancing the requirements of cost, performance and business risk.