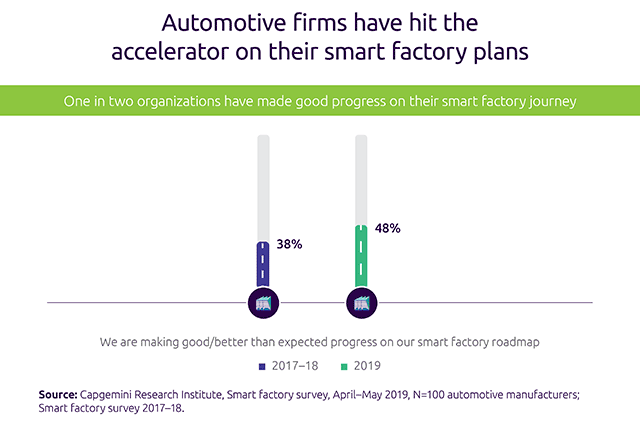
The automotive industry is well ahead of other industry sectors in adopting smart factory technology, and is accelerating its introduction. Investment is set to increase by over 60% in the next three years, and productivity gains could reach over $160bn (£124bn), according to a new report by the Capgemini Research Institute. However, only a minority of automotive firms are fully ready to take advantage through deployment at scale, it said.
The report, How automotive organizations can maximize the smart factory potential, tracks the development of smart factories by automotive manufacturers (OEMs) and suppliers in 2019, compared with equivalent research from 2017/18. The survey covered 100 firms in 11 countries.
It found that the industry had exceeded expectations on smart factory adoption, with 30% of plants been made smart in the last 18-24 months compared with 24% that executives said they had planned two years ago.
The automotive industry has plans to convert a further 44% of its factories to smart operation in the next five years, compared with 42% in discrete manufacturing, 41% in process industries, 40% in power, energy and utilities and 37% in consumer products. Automotive companies will be investing in a combination of greenfield and brownfield sites.
By 2023, the research estimates that smart factories could achieve a productivity gain in the region of $135bn on the average scenario (£104 bn) to $167bn on the optimistic scenario (£129bn). This is an annual improvement of 2.8%-4.4%, and an overall productivity gain of 15%-24% for the industry as a whole. The potential for these gains is already being demonstrated by companies such as Mercedes-Benz Cars, which has achieved a fourfold reduction in rejection rate on some key components through its use of advanced data analytics.
Dr Seshu Bhagavatula, Ashok Leyland president for new technologies and business initiatives, said there were three primary reasons behind its smart factory initiative. “The first is to improve the productivity of our old factories through modernising and digitising their operations. The second is to deal with the quality issues that are difficult for human beings to detect. And the third is to incorporate made-to-order or mass-customization capabilities,” he said.
However, the industry remains a long way from achieving the targets it has set for its smart factories. Compared with a productivity improvement target of 35%, so far only 15% has been achieved, and there has been only an 11% improvement in overall equipment effectiveness and reduced stocks/work in progress, compared with targets of 38% and 37% respectively. This demonstrates that many initiatives are yet to be scaled fully.
As many as 72% of automotive firms were still ranked as “novices” compared with 10% considered “frontrunners” ready to realise the full potential of smart factories at scale. Among OEMs, 18% were frontrunners, against 8% of suppliers.
A smart factory was defined as one exploiting digital technologies to gain improvements in productivity, quality, flexibility, and service. The three key digital technologies are connectivity, intelligent automation and cloud-scale data management and analytics.
