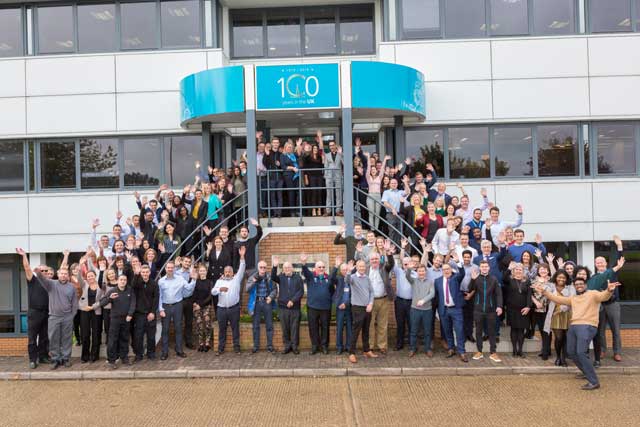
Atlas Copco has marked a century of operations in the UK by looking forward to how industrial technology might evolve over the next 100 years.
The company, founded in Stockholm in 1873 as a supplier to Sweden’s railways, was established in the UK with a single sales office selling diesel engines at the end of World War I. It has grown to employ more than 2,500 people at six production centres and numerous sales offices across the country.
Milestones during that time included the launch of the world’s first oil-free, rotary screw, stationary compressor in 1967; the first compressor with integrated variable speed drive in 1994; and the launch of the VSD+ compressor in 2013.
Looking forward to the next 100 years, the company identified digitalisation, electrification and artificial intelligence as megatrends set to transform the face of modern industry.
Atlas Copco has embarked on a significant process of electrification, with battery and hybrid products expected to reduce its carbon emissions by 50% by 2030.
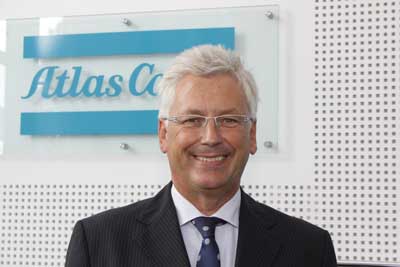
“One of the major areas of emphasis going forward will be the continued drive towards sustainability, particularly in electrification of equipment such as mobile compressors and generators, lighting towers and pumps,” said Atlas Copco UK holdings manager Alex Bongaerts. Traditionally, much of this type of equipment has been driven by diesel engines, but in urban environments or events such as music festivals, there is a desire for cleaner and quieter performance. That is resulting in the development of a wide range of battery-powered and hybrid products, which deliver reductions in carbon emissions. The future will require all of our products to be designed with a great deal of environmental consideration in mind.”
The company also described how technologies such as the internet of things, through the application of sensors and connectivity, would give industrial organisations much better visibility of their assets, bringing about advances in areas such as remote monitoring and predictive maintenance.
The use of artificial intelligence would allow equipment such as compressors to track and make process improvements autonomously, as independent systems. This could ultimately lead to a situation where compressed air systems operate independently in their own right, making autonomous adjustments to pressure and flow to facilitate process improvements.
And connected technologies such as virtual and augmented reality would transform the way that maintenance workers repaired industrial equipment, both in factories and in the field.
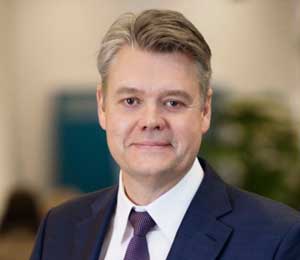
Atlas Copco president and chief executive Mats Rahmström identified a trend towards automation that was also flexible and agile, and allowed production to be adjusted according to demand.
He emphasised the importance of sustainability to the company. “All our sites around the world are connected to renewables where there is access.” He added that the company was investing in solar panels around the world. The production of solar panels extensively used vacuum, making products such as the company’s vacuum pumps essential, he pointed out.
compressorsGB.web@atlascopco.com
www.atlascopco.co.uk/compressors