DAK Consulting’s Dennis McCarthy reveals a helpful guide, hidden in the TPM process
This article is an overview of the leadership road map embedded in the Total Productive Mainttenance process. Its existence may be news to those who consider the ultimate outcome of TPM to be operator maintenance. The true outcome of TPM and the purpose of the TPM leadership road map, is a workforce engaged with learning, sharing knowledge and problem ownership to achieve year on year effectiveness gains.
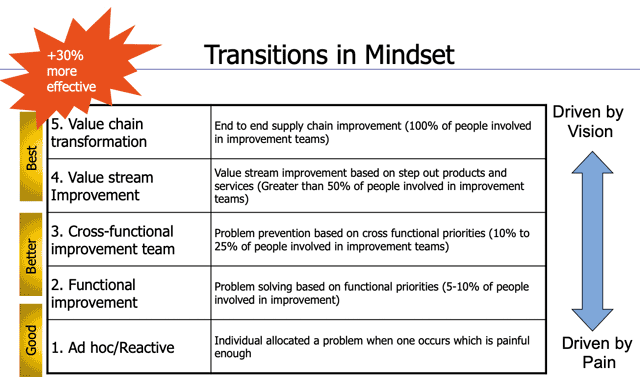
The first thing to understand is that leadership is a social skill and that conversation is the most powerful leadership tool.
Figure 1 sets out the range of conversations that leaders could have. At the pain-oriented end, leadership conversations are only triggered when things go wrong. This encourages short-term cost cutting and reactive management.
At the vision-oriented end of the continuum, leader conversations are triggered by action to change future performance by learning how to create new opportunity and advantage. Needless to say, the latter type of conversation is most commonly heard in award-winning organisations.
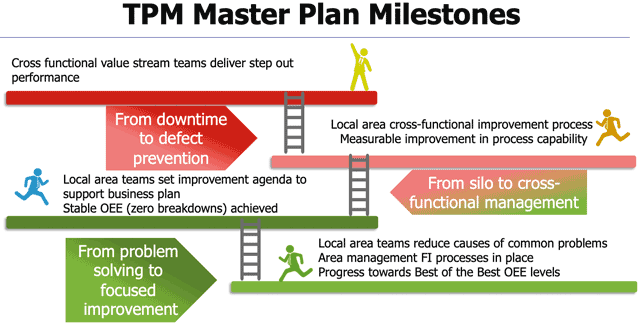
The TPM process provides a framework for the leadership team to align its view of what the future could be and develop the capability of the organisation to achieve that vision. This is a process characterised by leadership action to set clear accountabilities, and systematically win over the cynics and those who “just don’t get it” through practical hands-on actions.
The TPM master plan (see Figure 2) provides TPM leaders (known as pillar champions) with a series of conversations guided by series of policy principles and coaching plans. Through this they systematically develop front-line team capability and local area problem ownership.
These conversations, linked to practical improvement activities, systematically shift mindset from an outlook of short-term problem fixes to one of engagement with the journey towards a compelling vision such as zero breakdowns.
The journey is one of developing front-line team competence and confidence to handle day-to-day area routines. That includes tasks that are traditionally carried out by support departments such as asset care, work planning, quality assurance, performance reporting and focused improvement.
Initially, at the heart of the leadership coaching agenda are actions to increase collaboration between production and maintenance roles at a local area/line level. (see figure 3).
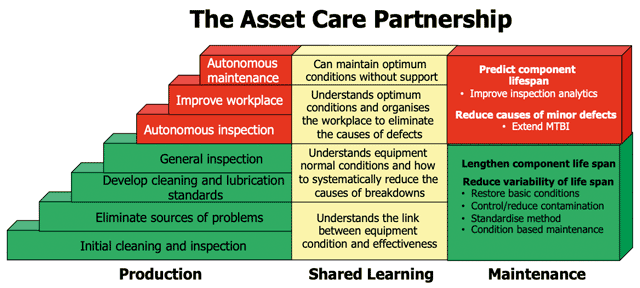
Progress through each of these steps involves front-line personnel in cross-functional team projects carried out alongside day-to-day work routines. Correctly designed, these become workplace learning projects that simultaneously develop local leadership and front-line team capabilities.
Through the leadership process underpinning the green steps, the increased competence of front-line teams frees resources to progress through the red steps. This provides a robust foundation for growth-related projects such as order lead time reduction or the introduction of new products and services.
This “secret sauce” for leaders hidden within the TPM process is relevant to improvement journeys irrespective of whether they are supported by Lean, Six Sigma, Shingo or TPM tools. It is a journey characterised by a leadership action to:
• Manage the future performance (driven by vision);
• Engage the workforce in practical projects to deliver that future;
• Facilitate shop floor workplace learning and knowledge sharing;
• Develop the front-line team capability to take on more of the routine local area management tasks.
Overall, in addition to cost, quality and delivery gains, the leadership process releases time for managers and specialists to concentrate on higher added value tasks. What’s more, these are typically achieved at low or in some cases no additional cost.
www.dakconsulting.co.uk
info@dakconsulting.co.uk 01491 845504