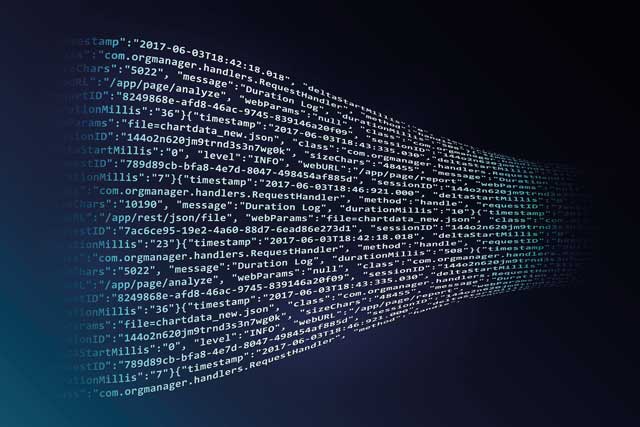
Advances in artificial intelligence, machine learning and data science are making possible a collaborative approach to plan for and predict failures, says Robert Golightly, senior manager for manufacturing at AspenTech
For decades, engineering companies have focused on how to use data to drive business value. Forty years ago, they began upgrading plant control systems from analogue to digital, helping facilitate the capture of data from sensors located around these plants. This data enabled the development of higher-level applications such as advanced process control and optimisation, which benefitted engineers by enabling them to operate plants closer to their limit.
Now engineers have found ways to achieve even greater benefits from the data capture and management process. It is easier and more cost-effective for them to generate large volumes of relevant data and then apply it to make operational gains in every aspect of their work, from design to troubleshooting.
This has come about partly because the price of instrumentation is falling and the cost of connectivity to that instrumentation is coming down. In addition, the advance of technology such as edge computing and fog computing is making more data available to engineers, and the ubiquity of the cloud is allowing companies to consolidate multiple silos of information and prepare it for analysis.
Easier access to larger volumes of data than ever before has, in itself, brought gains, allowing senior operatives to use plant data to improve working processes and drive operational, environmental and health and safety benefits. What has really changed things, though, are the latest advances in artificial intelligence, machine learning and data science.
Together, these technologies make possible a new approach: prescriptive analytics. This pinpoints patterns and “signatures” in the data that warn the operating company of an impending outage or plant breakdown, enabling it to take remedial action in advance.
The success of prescriptive analytics in providing weeks of accurate warning of asset failures is making possible a new collaborative approach to plan for those failures. Extending warnings from hours or days to weeks or even months is creating an opportunity to revolutionise how the whole organisation responds to the event. Maintenance, operations, scheduling, supply chain and maybe even sales can all get involved to reduce the impact.
These technologies are fuelling a revolution in asset maintenance that no operating company or plant operator can afford to ignore.
It is a change in the “ownership” of reliability, in which the responsibility is shared by maintenance and operations. When a sense of shared ownership of the downtime problem is fostered at the highest levels, it changes maintenance completely, enabling operators to reduce unplanned shutdowns, as well as cutting plant maintenance costs and operating expenses, while driving up revenue and building their competitive edge.
Solving the downtime problem has a direct and positive impact on the two most important issues companies are facing: safety and environmental responsibility.
Uncontrolled emergency shutdowns are hard on equipment, but industry estimates suggest 40% of injury accidents also happen in conjunction with those events. For the maintenance workers themselves, it is especially stark: the rate of accidents drops by an order of magnitude when maintenance is planned as opposed to unplanned.
Emissions can be much higher during periods of process upset or emergency shutdown. Flaring is a prime example, and though some flaring is unavoidable, the extreme emissions that often accompany rapid shutdowns can be avoided with earlier warnings and well-established responses.
The regulatory exposure to fines for exceeding allowances in these periods should be motivation enough to aggressively pursue the elimination of unplanned downtime. Beyond that, energy and water efficiency, along with air quality regulations, are prime concerns for shareholders – and should be at the forefront of the minds of corporate leaders as well.
All these issues demand innovative approaches, and implementing predictive maintenance to eliminate unplanned downtime is a critical step in the right direction. The emergence of prescriptive analytics brings more than just evolutionary change to process industries. If operating companies want to avoid being left behind, they need to join the revolution today.
More information:
Kate Jones, Kate.Jones@aspentech.com
www.aspentech.com