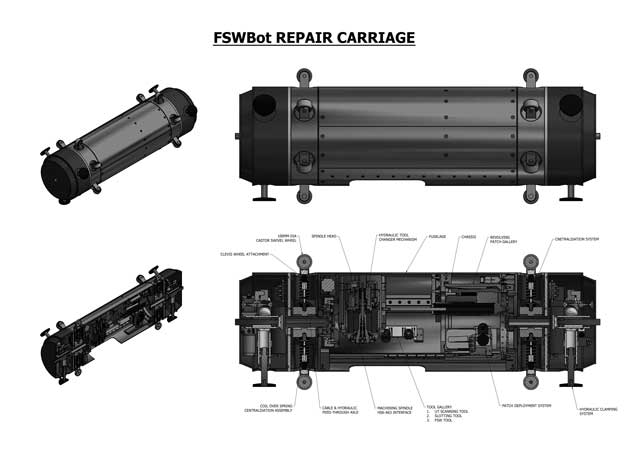
A company leading the development of robotic technology for repairing pipelines from the inside is seeking input from organisations and industry sectors which might have an interest in using the system. The technology is expected to revolutionise performance and improve safety in a range of industry sectors.
The FSWBot, or friction stir welding robotic crawler for internal repair and refurbishment of pipelines, is being developed by a consortium led by Cumbria-based Forth Engineering, with funding from Innovate UK. The technology was showcased last month at a British Manufacturing and Fabrication in the Offshore Energy Industry event in Aberdeen.
The project, which also includes TWI, J4IC, Innvotek and LSBU as consortium members, received funding last year to develop a proof of concept system. The aim is to integrate technology including friction stir welding, milling, patch deployment and ultrasonic NDT on a robotic system to make repairs on pipelines without the need to close the pipeline down.
Friction stir welding is a solid-state welding process which generates enough frictional heat to soften or plasticise metal without melting it, allowing metal components to be forged together at the joint between them. This project will demonstrate that a patch weld can be made in a steel pipe under oil, and that a representative FSW system can be made small enough to operate in a 36-inch diameter export pipe.
Forth Engineering has in the past developed tools and solutions for the nuclear industry. It believes the FSWBot will have applications in any industry in which the only solution to a problem is seen as sending a person into an extremely hazardous area.
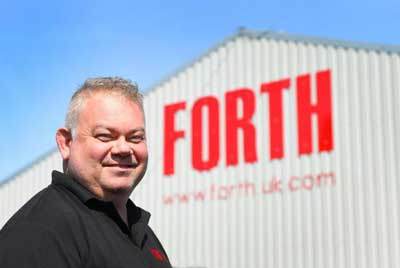
“There’s a fantastic opportunity for businesses and organisations in the UK and across the world, whether that’s nuclear operations, oil and gas, renewables, or others, to make use of this technology and to share their challenges so we can develop the FSWBot in ways to help them,” said Forth managing director Mark Telford. “We are very keen to talk to any businesses or organisations faced with that type of challenge to discuss with them solutions to the problems they face.”
The FSWBot is envisaged as being a five or six-segment PIG type vehicle, which will be inserted at the production end of the pipeline and will travel with the oil flow to a pre-designated spot to perform the repair. One segment will carry the FSW machine and a steel patch dispenser, with the other segments carrying the navigation, control system, communications, non-destructive testing and power storage or generation.
On approaching the defect, the FSWBot will slowly advance until the FSW system is in place over the defect. It will lock itself in place and confirm that it is correctly located.
An on-board turbine will harvest energy from the oil flow in the pipe. Once energised, the FSW unit will use a milling tool to cut away the corroded area and prepare a pocket in the pipe wall into which a steel patch will be dispensed.
The FSW unit will weld the patch in place and mill it flush with the pipe wall so it will not cause turbulent flow. FSWBot will then use NDT packages to inspect the weld, before unclamping itself and moving downstream. The project is due to be completed by the end of January 2021.