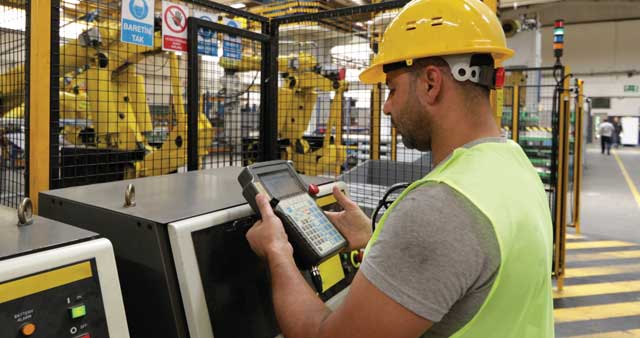
The increasing popularity of Industrial Ethernet places demands on providers of components such as pneumatic valves, where reliable, rugged, high-performance connectivity is becoming essential, says Patrick Berdal, European product manager for controls at Parker Hannifin
Industrial Ethernet is demonstrating an annual growth rate of 22% and currently represents 52% of the connectivity market. In recent years, several IE protocols have been introduced and widely adopted by automation equipment manufacturers because of their advantages over traditional fieldbus networks. The rising popularity and usability of IE can also be attributed to a good degree of backward compatibility and the availability of rugged components (hardwired) that are typically protected from electrical noise.
A further reason for the growth in the global IE market is the emergence of the smart factory, and with it, more demand for connected devices. Smart factories rely on the collection and analysis of data. Data analytics on an IE network make possible increased productivity, predictive maintenance, and real-time control of production.
IE, which can be defined as Ethernet applied to an industrial setting, requires rugged connectors, cables and, most importantly, better determinism – to ensure reliability and guarantee that the network will get workloads to their intended nodes on time. In order to achieve better determinism, IE uses specialist protocols. Several application-layer protocols for IE, such as Profinet, Ethernet/IP, EtherCAT and others, have been widely adopted across industry.
Each protocol has its own set of attributes and so selection is application dependent. For instance, Profinet has the compatibility to support a standard TCP/IP stack alongside real-time channels. Alternatively, ordinary switches and other standard IE infrastructures can be used when using EtherNet/IP, which helps control equipment costs. EtherCAT introduced the principle of pass-through reading (on-the-fly processing), which eliminates single-node targeting and allows for maximum bandwidth utilisation.
These breakthroughs have made IE a major fixture in control systems around the world.
Although there has been a greater take-up of IE in industry, the key for automation equipment developers has been achieving IE connectivity in a cost-effective and simple way. Now, however, any engineer tasked with finding a cost-effective means of connecting pneumatic valves to IE can consider utilising the latest high-capability, high reliability network nodes.
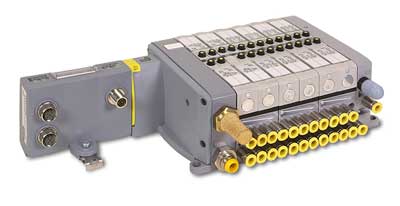
An example is the recently introduced P2M IE network node from Parker Hannifin. Developed with advanced factory automation in mind, the node is easy to configure and cost-effective. As a result, the company’s H Universal ISO Series valve, Moduflex valve and H Micro valve families can now connect to the IE network.
A low-cost node with integrated diagnostics makes network connectivity an alternative to traditional hardwired networks. Solutions of this type should help to reduce complexity and cost at the machine, while supporting the simple diagnostics required for the needs and objectives of smart factories and Industry 4.0.
Parker now offers a full range of IE connectivity options, including EtherNet/IP, Profinet IO, EtherCAT, Ethernet PowerLink, Modbus TCP/IP and CC-Link IE protocols.
Also boosting network connectivity is Parker’s H Series Network Portal, which provides on-machine flexibility for IE application on the H Series ISO valve with Universal manifold. The network portal handles machine digital or IO-Link I/Os, eliminating the need for additional PLC input and output cards or other remote modules. Having the I/O on the valve manifold via the network portal allows for easy and cost-effective centralised machine application, even in caustic, washdown or hazardous areas, or where extreme temperatures are prevalent.
Demanding automation applications, such as motion control and safety, are ideal candidates for IE as both can benefit from the reliability and extra bandwidth that this connectivity solution brings. Low-cost connectivity with integrated diagnostics has at last become reality, further reducing complexity and cost at the machine, while aligning with the needs of smart factories and Industry 4.0.
Looking to the future, IE networks are likely to continue growing and become a mainstay in industrial communications, helping to control industry and infrastructure by connecting different devices, machines, systems and users, regardless of location. The IE compatibility of key automation components such as pneumatic valves is vital if industry is to achieve the full benefits that total and reliable connectivity can bring.
More information www.parker.com or @parkerhannifin.