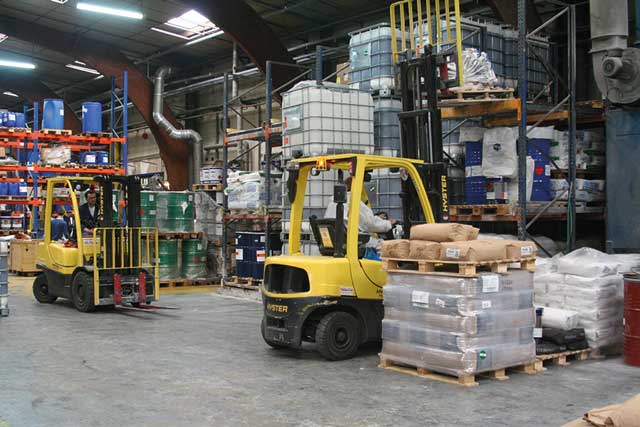
Potentially explosive atmospheres occur throughout the chemical supply chain. Mark Nailer, industry manager for Hyster Europe, discusses solutions to allow compliant and efficient handling.
It can only take one spark or hot surface to cause an ignition in the potentially explosive atmospheres found throughout the chemical supply chain. Heat and spark control are therefore primary considerations for businesses involved in the production, storage and transport of flammable chemicals.
Raw materials
The production and delivery of raw materials to a manufacturer is the first stage. Potentially flammable raw materials are likely to be delivered, pumped and stored in large tanks. Drums and intermediate bulk containers may also be found in areas where forklifts will be working.
This may be a Zone 2 hazardous area, classified under the ATEX regulations covering explosive atmospheres as where a mixture of air and flammable substances in the form of gas, vapour or mist is possible, but not likely to occur in normal operation. To prevent the risk of ignition, it is vital that only explosion protected and rated lift trucks enter such an area.
Hyster Europe works with specialists, such as Pyroban, which conduct explosion protection conversions to help equipment comply with legislation. In Zone 2, the Pyroban conversion of a lift truck combines gas detection with various explosion protection methods such as restricted breathing enclosures – fitted around items such as hot components or those with potential for arcing or sparking to restrict the ingress of flammable gas or vapour – and surface temperature cooling.
It is important for drivers to be aware of the presence of a flammable atmosphere in a Zone 2 area, so trucks operating in Zone 2 areas can be converted with “active” gas detection systems. If certain levels of gas or vapour in air are detected, the driver receives an audible and visual warning, and if the level elevates further, the truck forewarns the driver and safely shuts itself down.
In addition to systems that alert the driver, those using lift trucks in Zone 2 may also need to specify particular tyres, seats, batteries or other ancillary products, to reduce the risk of static electricity causing ignition.
Chemical manufacturing
Raw materials are mixed or processed to manufacture specific chemicals, from pharmaceuticals and cosmetics through to the food, paints or coatings industry. Here, lift trucks are used to transport and feed chemicals into the production line.
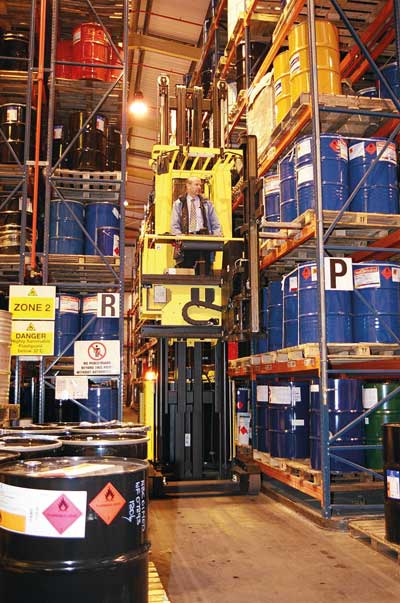
While some manufacturing operations are Zone 2 areas, others may be classified as Zone 1, where an explosive atmosphere is likely to occur in normal operation.
Unlike Zone 2 equipment which shuts down in the presence of a flammable atmosphere, explosion protected trucks for Zone 1 must be specially converted to allow them to work through the atmosphere. This “passive” protection features explosion-proof enclosures and other technology such as frame leakage monitoring and intrinsically safe circuits, essential for maintaining productivity in such areas.
As well as explosive gases or vapours, chemicals in the form of combustible powders or dusts also pose a risk of ignition. To reduce risk, explosion protection modifications are available for materials handling equipment operating in these areas, designated Zone 21 or Zone 22. In dusty atmospheres, an in-cab air filtration system can also be fitted to improve the comfort of the driver.
Chemical warehousing and logistics
Finished chemical products are usually stored in bulk containers and sealed drums in an indoor or outdoor warehouse area.
Explosion protection conversions can be applied to many truck types, including warehouse equipment. This allows operators to select a reach truck or very narrow aisle forklift, even if the equipment will be operating in a potentially explosive atmosphere.
Logistic companies taking on contracts to transport chemicals also need to make sure that the trucks operating in their warehouses and portside stores are fitted with the correct level of explosion protection.
For more information, speak to your local Hyster distribution partner or visit www.hyster.eu.