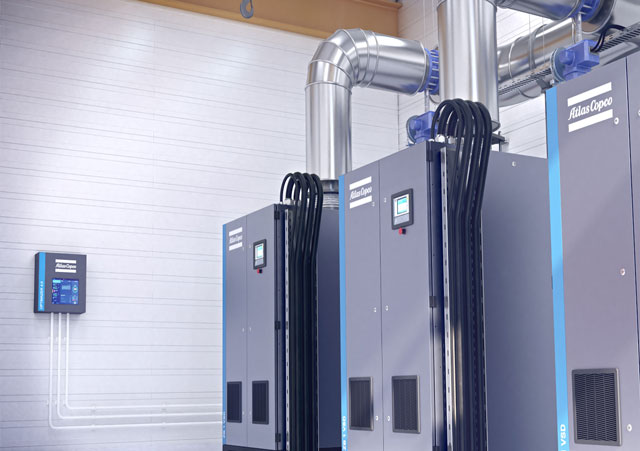
Compressed air networks with multiple compressors and fluctuating demand can be energy wasteful if not properly optimised. Simple control systems switch compressors in and out of service based on pressure setpoints and a predetermined sequence. This caters for demand fluctuations but does not allow for optimisation. But centralised controllers offer optimisation and pressure control with additional benefits too.
The Atlas Copco Optimizer 4.0 is a centralised controller for compressed air networks designed for energy efficiency and ready for Industry 4.0. Here are 5 reasons to consider adopting a centralised controller like Optimizer 4.0 for your compressed air network:
1. Flexible compressor switching
Sequencing controllers use a predefined sequence to load and unload compressors in the network. This can be inefficient from an energy perspective because the next compressor in the sequence may be too large for the change in demand.
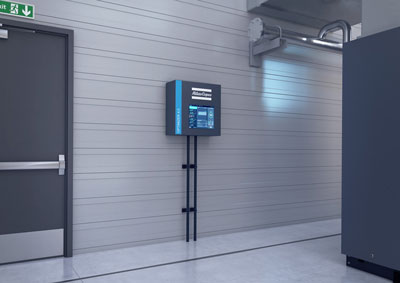
A centralised controller makes flexible decisions about compressor switching. Sudden drops in air pressure will result in a large compressor being switched in, whereas a slow drop in pressure will result in a smaller compressor being switched in. The flexibility also enables prioritisation of newer and more economic compressors and allows equalisation of workload between compressors over time.
2. Optimised VSD operating points
Fixed speed compressors use up to 20% of their full load energy for running the machine without load. Variable speed drives (VSDs) are better because they do not waste as much energy. However, even VSD compressors must be run optimally to maximise the energy savings.
Sequencing controllers keep multiple VSD compressors in an optimum performance zone, but not necessarily at their optimum point. If two VSD machines are running together, one could be running at 70% load and the other at 30%. However, centralised controllers balance the load across multiple VSD compressors so that each machine operates at its optimum point.
3. Contribution to ISO 50001 Energy Management Systems
The ISO 50001 standard provides a framework for managing energy consumption in a systematic way. It is based on the principles of setting targets, measuring results and striving for continuous improvement. ISO 50001 enables sustainable production, energy efficiency and a reduction in energy costs.
Optimizer 4.0 is fully aligned with ISO 50001 principles. The graphic user display shows the energy performance of each compressor as well as the network as a whole. Performance against energy targets can be monitored in real time as well as through historical trends.
4. Industry 4.0 ready
Industry 4.0 is built on the foundation of access to information and cloud-based analysis, which is used to return instructions to local control systems. The simpler a compressed air system is (e.g. a stand-alone compressor with a local control panel), the less accessible Industry 4.0 is. However, an Optimizer 4.0 controller connected to multiple compressors with all their sensors and flexible switching abilities is completely Industry 4.0 enabled.
What makes Optimizer 4.0 especially suitable for Industry 4.0 solutions is the connectivity offered in the solution. The system is accessible from any computer on the LAN and can be directly coupled to the site SCADA system. Cloud based access can also be configured through client firewalls giving expert Atlas Copco engineering resources access to the information for analysis and advice.
5. Multi-vendor compatibility
A challenge of some compressed air networks is the combination of different brand compressors. Compatibility issues can prevent controllers from accessing compressor information and switching them automatically.
The MK5 interface enables systems like Optimizer 4.0 to interact with compressors from other vendors. This connectivity means that all compressors in the network can be switched from a single controller, enabling complete optimisation.
Conclusion
Centralised controllers overcome the limitations of equalising control. They offer the benefits of flexible compressor switching, optimised VSD operating points and compliance with ISO 50001 energy management systems. In addition, their multi-vendor compatibility and Industry 4.0 readiness make them a value adding technology for any air compressor network.
The more complex the compressed air network is and the more fluctuating the demand, the greater the benefits that can be realised through centralised control. Energy savings alone can be used to justify the implementation of a system like Optimizer 4.0.