The right mindset is a crucial element in achieving truly continuous improvement, says Dennis McCarthy of DAK Consulting
As a young industrial engineer I read case studies of organisations which had made giant strides in performance improvement and assumed that following their achievement, as in fairy tales they all lived happily ever after. It wasn’t until I visited Japan and saw companies that had achieved significant year-on-year gains for over 25 years that I began to understand what “continuous improvement” really meant.
Despite a track record of improvement one such company, a lighting manufacturer, had stumbled when bringing in automated processes. It took two years of systematic effort to get one of its four lines to operate with zero intervention over an eight-hour shift. It took a further year to get the remaining three lines to operate to the same standard.
This is the reality of continuous improvement. It is a voyage of discovery. At the start of the company’s journey no one in its industry had achieved this standard of process control. The mindset that drove its effort to break new ground was one where continuous improvement meant “never-ending”. The shop floor reality was that each step towards the goal of zero intervention was a step into the unknown. How did it achieve what others had failed to.
First, underpinning this mindset was a management team that recognised the commercial advantages of an operation where they could run additional shifts to meet demand, without extra labour. In addition the process would produce fewer defects and use less material. They were able to engage enough of the organisation with the vision to make progress.
To guide them on this voyage of discovery, they used OEE (overall equipment effectiveness). Just as the management mindset to continuous improvement was important, the mindset of engineers to the word effectiveness in overall equipment effectiveness also had a significant impact.
OEE is a percentage arrived at by multiplying together the individual percentage figures for equipment availability, performance (percentage of theoretical production capacity achieved) and quality (see box overleaf). It is a measure of how well a process performs against expectations. The power of OEE is not in looking at past data but in combining its ability to forecast OEE improvement potential; to set realistic and achievable improvement steps; and to define the tactics to achieve each step.
Engineers in the company used OEE to guide efforts to systematically achieve four levels of effectiveness:
- Levels 1 and 2: Stabilise effectiveness (consistent OEE with less than 1% breakdowns);
- Levels 3 and 4: Optimise effectiveness (increasing OEE with reduced levels of planned intervention).
To support progress towards each level of effectiveness, total productive manufacturing sets out focused improvement toolsets for each area of hidden loss (such as breakdowns).
The table below sets out OEE summary standards illustrating the four levels of competence in each OEE hidden loss area.
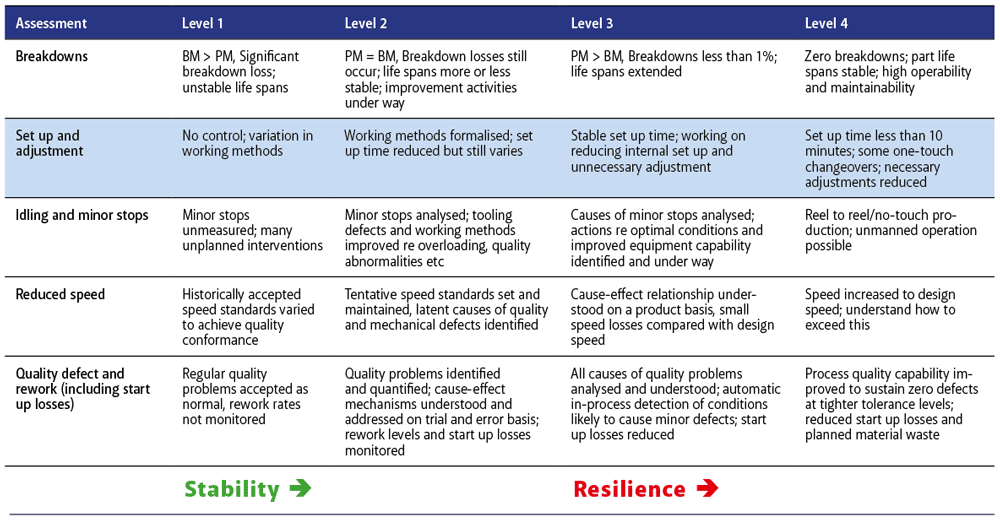
In this case, significant levels of intervention had been needed as part of routine operations. This was in part due to knowledge gaps about the shop floor reality which had been overlooked when specifying the automation approach. An OEE analysis identified set-up and adjustment losses as the improvement priority. That led to the use of TPM focused improvement tactics as follows.
- Observe adjustments made (both planned and unplanned);
- Remove unnecessary adjustments, standardise necessary ones;
- Improve procedures and workplace organisation to reduce stop time and improve tool and work setting;
- Categorise necessary adjustment needs (accumulation of errors, lack of rigidity, lack of standardisation, etc);
- Systematically reduce each adjustment category.
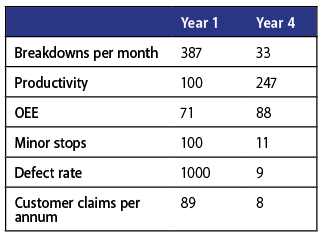
Achieving the gains entailed workplace learning projects in small cross-functional teams to improve methods, develop capabilities, share knowledge and lock in the gains in a process led by engineers in pursuit of a commercial goal. The results over the four years are shown in the adjacent table.
What I learned from this company was the power of combining OEE as a measure to identify potential and track progress with the systematic approach set out by TPM focused improvement toolsets.
With the right mindset, managers and engineers can work together to achieve true continuous improvement. Mindset is also the main reason that fewer than 1% of organisations do that.
Calculating OEE
Availability: Out of the 100 planned run hours the process ran 80, therefore the process availability is 80%. (The 20% of non available time will be due to either breakdowns or set up and adjustment time.)
Performance: The theoretical capacity of this plant in the 80 hours run is 100 units but only 75 were produced so the performance (when running) is 75%.
Quality: Out of the 75 produced only 60 were produced right first time so the first time quality rate is 60/75 or 80%. Overall equipment effectiveness is 80% × 75% × 80%, that is 48%.
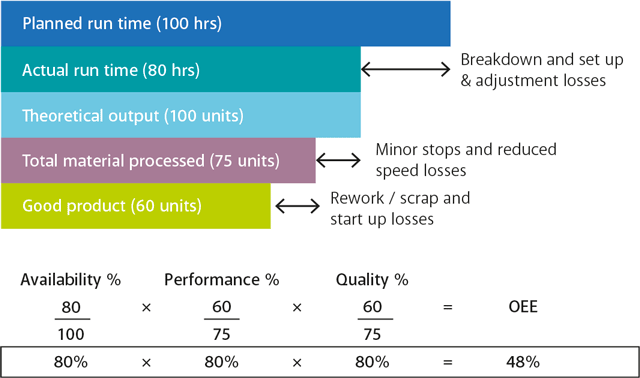
Dennis McCarthy is a director of DAK Consulting.
www.dakconsulting.co.uk | 01491 845504