Recent advances in the design and manufacture of spare parts, including digitalisation and new manufacturing techniques, have led to a significant reduction in the time taken to create spare parts, say Pharic Smith, head of engineering for parts retrofit and Siegbert Hardock, head of tendering for parts retrofit at Sulzer.
Important assets such as pumps, compressors, expanders and turbines are designed to offer a long service life. But at some point, new parts will be required to maintain reliable operation. In some cases, the original equipment manufacturer will be able to supply spares, but in others, it may be necessary to source the parts from a third party.
The durability of the equipment means that decades may have passed since the machine was originally manufactured and this can lead to additional difficulties. The original manufacturer may no longer be in business, or the lead time on an original part may be more than expected.
Best of both worlds
Fortunately, there have been significant advances in modern parts manufacturing technology in recent years. The introduction of computer numeric control (CNC) has brought considerable improvements in machining precision, along with the advent of 3-dimensional drawings. Additive and hybrid manufacturing have led to huge time savings when creating casting moulds as well the components themselves. Maintenance engineers looking for new components suddenly have a range of solutions that can deliver parts in record time.
If the original engineering drawings for a component are not available, the part will have to be reverse-engineered. Depending on the complexity of the part, this can require hundreds or thousands of measurements to be taken to create a new drawing.
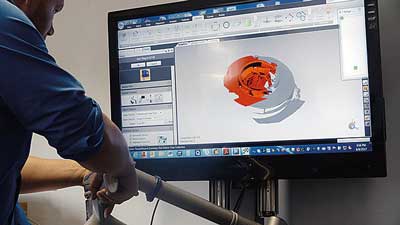
Using 3D laser scanning equipment, a new drawing for a complex object such as a pump impeller can be created in minutes. Better still, improvements can be made to the original design: upgrading materials, applying modern coatings or improving efficiency by applying computational fluid dynamics to optimise performance.
Breaking the mould
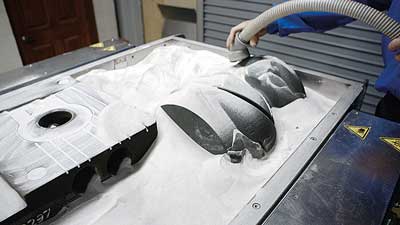
Larger components are often created by casting metal in a sand mould, which would traditionally have been made using a wooden template. Today, 3D CAD can be used with a 3D sand printer to rapidly build a mould.
An alternative process is to use a multi-axis CNC robot milling tool to create a precision mould from a solid block of sand. This takes just a few hours, as opposed to a few weeks, as would be required to create a traditional wooden pattern. Lead times can be drastically reduced, especially when the various aspects of the process are well connected, or even better all on the same site.
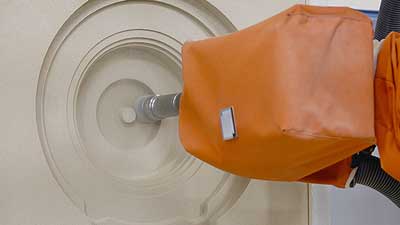
Having created the basic component, the machine shop needs to apply a precision finish using CNC lathes, milling tools and grinders to produce the final dimensions and surface finish. These can be optimised for the application and to ensure a perfect fit when the machine is reassembled.
Rebuilding and renewing
Where parts are worn or eroded, it may not be necessary to create a completely new component. Hybrid engineering, which combines additive manufacturing and precision machining, can be used to rebuild existing parts to their original dimensions.
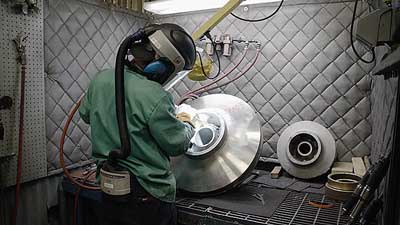
Processes such as laser metal deposition can be used to add material that has an excellent bond but with minimal heat build-up, reducing stress within the component. The final dimensions are then achieved using multi-axis CNC machine tools.
Every part manufacturer should have extensive testing facilities including non-destructive testing (NDT), material analysis, chemical analysis and heat treatment reports. These are crucial in determining the exact specifications of the new component and ensuring that they meet the required standards.
Local specialist engineering
Investing in the technology and machinery to deliver precision new parts is just the first step. The service requires a global network of service centres capable of understanding the intricacies of each project and communicating directly with the specialist parts manufacturers. Sulzer has developed such a network, along with the expertise and knowledge to deliver high quality new parts quickly.
Further information: www.sulzer.com
Email: daniela.haldenwang@sulzer.com | T: + 49 7251 76 202