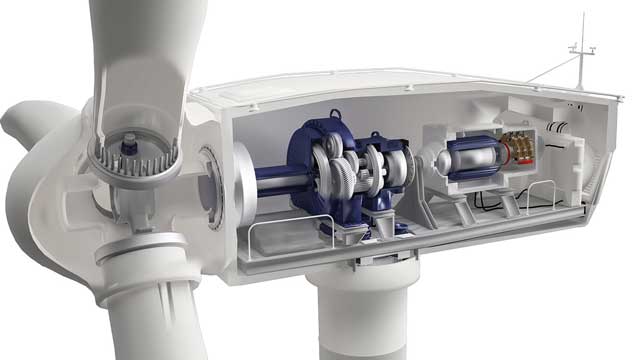
Precision sensor technologies are proving their value in condition monitoring of operational windfarms, says Chris Jones, managing director of Micro-Epsilon UK.
Active monitoring using precision sensor technology is not only being used in the production process of wind turbines and test rigs, but also in the real-time monitoring of turbines during operation. Innovative sensor solutions are now available that make possible reliable measurements and targeted evaluation of critical data. The technology helps customers by preventing repairs, reducing failures, reducing costs and helping to predict maintenance cycles. Compared with manual inspection, where inaccuracies can arise through tiredness or mood, sensors can provide high precision, reliable, repeatable measurement results 365 days a year..
Offset measurement of the coupling ring
The average hub height of a wind turbine is 130m. Above 100m, huge wind loads act on the rotor blades, housing and tower. Therefore gearbox and generator have an elastic bearing, and couplings in wind turbines must balance the relative movement of the two. To measure the offset of the metallic coupling ring, non-contact eddy current displacement sensors can be used to determine the distance, in turn allowing measurement of the load profile.
Monitoring is required in order to avoid unnecessary wear of couplings, bearings and shaft seals or, in extreme cases, serious damage to the wind turbine. Eddy current sensors allow measurements to be carried out in different directions – on the axial, radial and tangential axes.
Some suppliers offer temperature-compensated versions that provide high measurement stability, even in strongly fluctuating ambient temperatures. The sensors are factory-calibrated for ferromagnetic and non-ferromagnetic materials, which eliminates the need for field calibration of the sensor.
Compared with inductive switches and sensors, eddy current sensors provide a higher bandwidth and so are suitable for precise detection of high speed movements.
Gap measurements in bearings
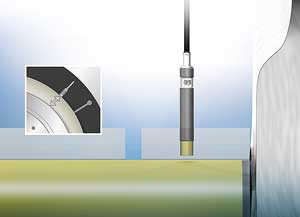
Hydrostatic bearings are used in wind turbines. The task is to monitor the gap size between the bearing surface and the shaft where the oil film prevents direct contact. If there is a malfunction in the hydraulics, the oil pressure can rise and, in extreme cases, the gap will close. This would lead to damage of the bearing and a possible turbine failure.
A sensor mounted horizontally to the bearing shoe measures through the oil film and the plain bearing directly onto the shaft. Non-contact eddy current displacement sensors can be used, which are robust, compact and have an integral controller. As well as offering excellent resistance to lubricants, high pressures, and extreme temperatures, the sensors allow rapid commissioning and can be retrofitted to existing wind turbines.
Air gap generator monitoring
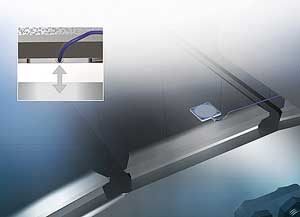
With very large generators and electric motors, it’s important to determine the radial run-out of the rotor inside the motor compared with the stator. Due to imbalances during operation, which could be due to wear caused by extreme wind and weather conditions, the rotor might touch the stator, which could lead to catastrophic failure. Non-contact optical and capacitive sensors are used to measure the distance between the stator and rotor and to monitor the rotor gap while the motor is running. Non-contact capacitive sensors provide long-term stability, reliability and temperature stability.
Other monitoring tasks
Gearbox temperature can be measured during operation. Heating up of gearbox components may indicate a potential problem with a component.
Draw-wire displacement sensors can monitor the position of the air flaps which control the cooling air supply. Eddy current displacement sensors can measure the distance between the wind turbine nacelle and the tower, which allows early recognition of any fluctuations.
Non-contact laser triangulation sensors are ideal for measuring the distance between the tower and the foundation.
Overall, sensors are playing a powerful role in maintaining the health of wind turbines, both offshore and on.
t: 0151 355 6070 | e: info@micro-epsilon.co.uk
www.micro-epsilon.co.uk