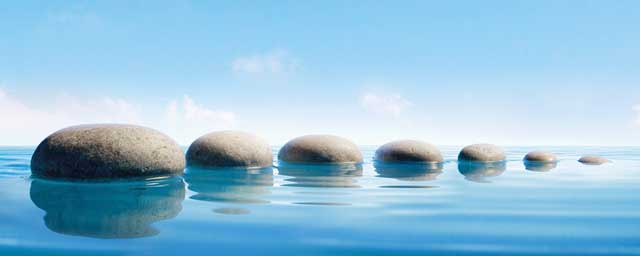
ABSTRACT
Many businesses try to survive without a good strategy to provide the direction for the maintenance function of the business – even though such functions take care of assets that are vital to the business and expensive to replace.
This article outlines a dual factor approach: maintenance strategy involves determining the optimal asset care policies to deliver high reliability plant, and extended equipment life. However, to be successful, it also involves consideration of the various non-technical inputs into the maintenance operations model such as involving all the players in the maintenance team in a deliberate way, managing the funding needed for the improvement effort, benchmarking maintenance performance with your peer operations, and managing the prevailing culture.
Introduction
Many companies have tried to improve the efficiency of maintenance in their plants. Some are successful, but many initiatives do not achieve their expected benefits. One reason for this could be that the company’s maintenance strategy is too poorly defined or that the company operates without any kind of formal maintenance strategy at all.
In fact, there is no clear, universally agreed definition about what exactly constitutes a maintenance strategy across industry bodies, and the guidance about what makes a good one is quite hard to find.
The British and European standard for maintenance management is BS EN 13306:2017, and it makes two key definitions:
Maintenance Objective – The targets assigned and accepted for maintenance activities.
Maintenance Strategy – The management method used to achieve the maintenance objectives.
Although these rather broad definitions leave their actual meanings open to interpretation, they do indicate the broader view of maintenance it is necessary to take to create a robust strategy. While many, if not all, maintenance operations will have documented and business-aligned objectives, it is rare to find a maintenance strategy that goes beyond the substance of the task list and task frequency and perhaps necessary spare parts.
A robust maintenance strategy creates a focus for the maintenance operation and creates a consistent ambition for the maintenance team, aligned to the needs of the parent organisation.
It is useful to consider maintenance strategy from a dual perspective:
- Asset Care Strategy
Defining what the operation’s key physical assets are, and what maintenance regimes they need to function correctly – this covers the maintenance plan tasks, and frequency of performing them. - Operational Strategy
What the maintenance function needs to do to provide the required level of service to the operation. This is much broader, and covers spare parts provision, maintenance planning tasks, funding, training, business processes and procedures.
This model puts, quite properly, the asset at the heart of the maintenance strategy – defining what is needed to achieve its optimum performance; and then around it is defined all the management tasks needed to provide the asset care strategy at the core.
A good maintenance strategy is one that achieves high uptime for key equipment at low maintenance costs. But what works in one industry may not work in another.
In this article, we’ll define seven steps that will underpin a winning maintenance strategy.
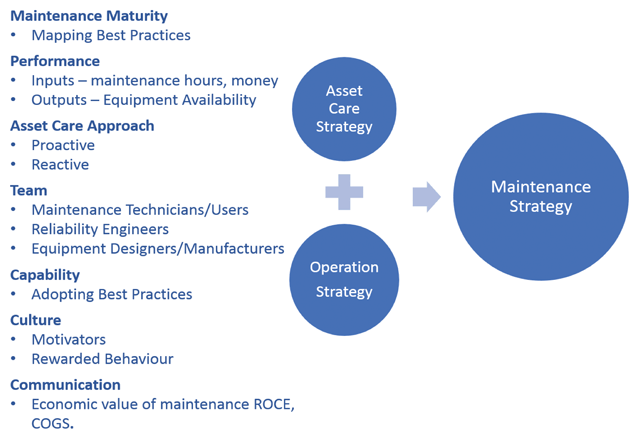
1: Understanding current maturity
The first step in developing a robust maintenance strategy is to understand how mature the operation currently is. The term maintenance maturity describes how well developed an operation’s maintenance processes and systems are, and to what degree they deliver value for the wider operation.
The maturity model shown in Figure 2 shows the generalised progression of a maintenance operation as it gains more and more capabilities. Capabilities are demonstrated by the beneficial use of maintenance best practices, and the overall maintenance strategy able to be employed by the maintenance operation significantly changes with the development of more capabilities.
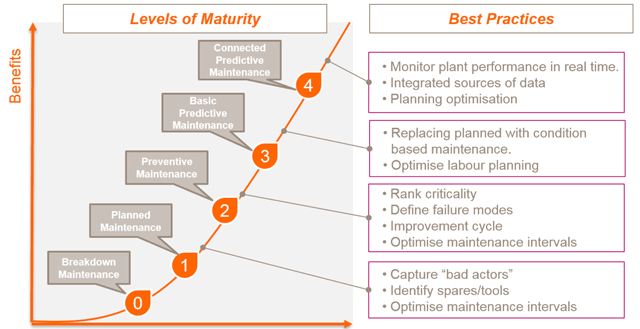
The first strategy that is often employed in a lower capability maintenance operation is to seek to be good at fixing things. Then, as the realisation sets in that this will take the organisation only so far in downtime reduction and efficient resource allocation, more planned activities take place, with the emphasis more on job and workforce planning but still dealing with breakdowns in a rather reactive way.
Adopting a more active strategy demands a higher level of technical capability in reliability engineering, maintenance management and equipment knowledge, so it often develops later in an operation’s progression.
Predictive maintenance, where the intention is to avoid any downtime at all by constantly watching for earliest signs of failure, needs a higher order skill again.
How far does the operation exploit known best maintenance practices, and how does it compare against others along the maturity curve?
An honest assessment of current maturity can be carried out by simply gaining an understanding of maintenance best practices and observing whether the operation uses them routinely or not. Most of the specialist consultancies also have structured frameworks which can be assessed against, at a cost.
As individuals in the organisation learn to do a wider range of things, better results should follow.
2: Know your current performance in detail
In terms of performance of the maintenance operation, the most fundamental measure of success is the availability of the equipment the operation is responsible for. Equipment availability can be translated directly into the key objectives for the business. So, for manufacturing operations, high equipment availability allows more products to be made for sale; and for service operations, high equipment availability allows the continuity of service. A good maintenance operation commonly uses measures such as overall equipment effectiveness and service level.
To really understand performance, however, it is also necessary to grasp its flipside – how efficiently the inputs into the operation, such as money and hours of human effort, are being translated into these output measures.
Some data collection is necessary:
- Understanding equipment availability – When there is downtime, where does the time go, and what causes it? What are the real, underlying or root causes for failure?
- Understanding the inputs – Where does the money go? How much time do people use doing activities that don’t add any value to the goal of achieving the best results?
3: Deploy the right asset strategy
From the perspective of the wider operation, the cost of corrective maintenance usually far exceeds the costs of any realistic preventive maintenance effort. The exact cost ratio differs from industry to industry but when the full cost of service interruptions, lost orders, loss of reputation or government fines or other losses are considered, prevention of failures is frequently more cost-effective than waiting for the failure to occur.
Selecting the right approach to each asset’s maintenance regime is therefore fundamental. On key equipment, the goal should be to deliberately select the right maintenance approach for each type of equipment failure that minimises the overall cost of the failure to the organisation.
There are generally thought to be only three broad approaches:
- Let the equipment fail and then fix it (corrective or “run to failure” maintenance).
- Replace or recondition parts at intervals known to approximate the lifespan of failing components (planned preventive maintenance).
- Detect when the equipment is starting to degrade and replace or recondition at a time convenient to the operation (predictive maintenance).
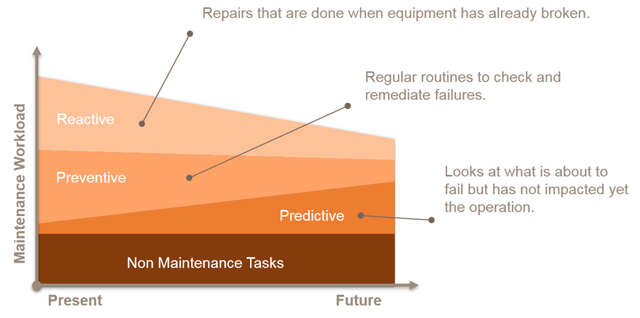
To be cost-effective, the corrective maintenance approach should be selected only when the cost of “fixing” is less than the cost of proactive prevention. Such a case may be where the spare part, or indeed the equipment itself, can be replaced very cheaply, or where the operation can function adequately for a while without the use of the asset. (Air-conditioning equipment for administrative offices is sometimes used as an example needing this approach).
Even then, a true proactive approach for corrective maintenance will already have the right spare parts, access equipment, training and clear responsibilities in place to get the asset back into working order as quickly as possible.
The most proactive approach should be selected for the asset to reduce long term costs by focusing primarily on the wider cost of equipment failure.
The maintenance manager will be only too familiar with the increasing need to maintain equipment in a cost-effective manner. For some organisations, at budget review time, maintenance spending is the first item on the list of cost areas to be culled.
In the long run, it is more sustainable to build reliable processes and then let the previously high cost of corrective work reduce naturally than to undermine a good maintenance regime by cutting maintenance costs without regard to the impact.
4: Involve the full team
Recognise that although the technician and reliability engineer are on the front line of equipment maintenance, a much wider team of people are involved in determining the success of the maintenance operation. Each role has a specific job to do in reducing breakdowns and achieving high reliability.
- Front line maintenance staff can provide vital data about continuing equipment issues, such as type of fault, duration of downtime, and remedy. In conjunction with a good maintenance management system that can classify, track and provide data reports this can be an important tool for the reliability engineer to use to improve equipment performance.
- Equipment users have an underrated role in the maintenance team. Keeping the asset clean and ensuring that the equipment they use is running within proper settings are the first steps in good asset management. Later, further along the maturity curve, they can acquire the technical knowledge to be able to detect some types of faults and the skills to fix the simple ones.
- It must be remembered that by the time equipment is in use, the inherent reliability of the equipment has been established. An important number of failures stem from design deficiencies in some way, and the ability to influence reliability is greatest at the early stages of a project. The role of production/reliability engineering, therefore, is to maintain this inherent level of performance, but they cannot often remediate design flaws that may create reliability issues.
- It follows then that the equipment supplier’s own engineers and designers play a vital role. They influence reliability at the design stage through selection of components, layout and configuration of equipment, and can be called on to work with customers to improve reliability issues. A good working relationship with the supplier of equipment is an important determinant of success in any reliability programme.
5: Communicating maintenance strategy in the language of economics
When it’s time to present the strategy to the board, using the right language helps the maintenance manager to build a credible case for change. Engineers frequently find themselves justifying maintenance programmes to non-engineers at senior levels using technical justifications. That approach frequently misses the point that all maintenance strategy often involves essentially economic decisions.
A different approach is needed. Nearly all technical problems at their heart are trying to solve a business issue. So instead of stating what the technical benefits of any proposal will be, start with the business benefits. The technical overview can follow once the economic considerations are accepted.
This is not as difficult as it may sound. It helps to think about “What financial contribution does maintenance make to the operation?” – see figure 4. Examples include
- Avoiding equipment downtime or interruption of service.
- Extending the life of expensive capital assets
- Reducing the number of hours required to complete the same level of maintenance.
- Avoiding risk to safety, product quality or business reputation.
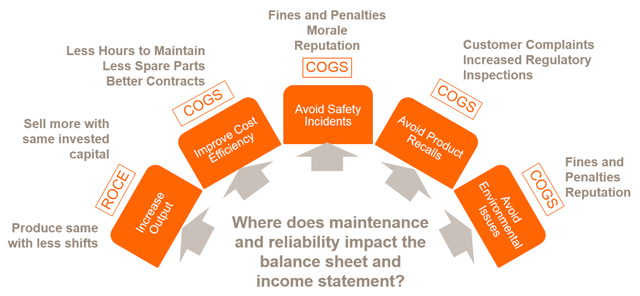
All these contributions can be quantified in hard cash terms. Extending the life of a capital asset, for example, avoids or delays capital expenditure, which has a favourable effect on the business’s return on capital employed. Similarly, efficient maintenance labour planning can lead to a lower requirement for manpower, and therefore reduce the business’s cost of goods sold (COGS). These are key management ratios at the heart of every business and should be used as the basis for justifying any maintenance programme changes.
6: Build Capability
The maintenance operation will always achieve the results that it is designed for. For example, an organisation that predominantly focuses the efforts of its maintenance technicians on repairing equipment will never have the time to take the broader tasks that good reliability engineering needs – collecting and analysing data and performing equipment modifications. Similarly, if there are no maintenance planners, don’t expect well planned and efficiently executed maintenance.
Using a broad capability model helps guide the maintenance manager to know where to focus the improvement programme. Linked to the maintenance maturity, the capability model indicates where best practices are used to accomplish tasks within the maintenance management remit. Best practices are defined as professional practices that are prescribed as being correct or most effective. These may vary among industry sectors and may need the external view of a specialist consultant to help define them.
The assessment begins with defining the main sub-functions within the operation that it needs to perform in order to provide maximum value to the organisation: planning and executing maintenance, managing spare parts and managing maintenance budgets will be general to all maintenance operations but others may be specific to an industry.
Once the main sub-functions themselves are defined, the current level of capability in each of the areas can be assessed by looking at best practices that would be expected to be seen in use to accomplish these tasks. So a high level of capability is shown by observing best practices in place and in full use within the operation. Where there is an absence of best practices, that would indicate a lower level of capability.
One version of this model is shown in Figure 5, where 12 maintenance management tasks are defined, and the operation’s current level of capability is plotted against a level of performance that this organisation defined as what it needed to bring most value to the operation.
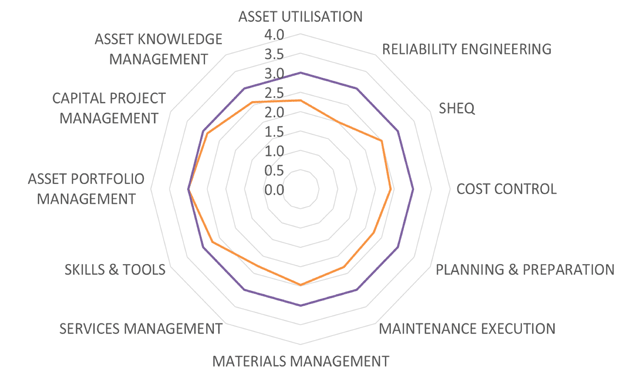
It is important to be clear about what capabilities are required for the accomplishment of the maintenance objectives. Best practices are only useful where they contribute to the performance of low downtime of key assets or allow the work to be done more efficiently. For example, a best practice of detailed failure analysis used in the petrochemical industry may not be appropriate in low profit margin operation.
The actions required to close the gaps then form one part of the operational maintenance strategy.
7: Understand the culture change
There is a vital cultural element to any type of improvement activity and ignoring it can often be the reason improvement initiatives unexplainedly fail.
Cultural change can be difficult to grasp unless you break it down into pragmatic steps. Figure 6 shows the relationship between culture and maintenance maturity (developed by Ledet and others [2]).
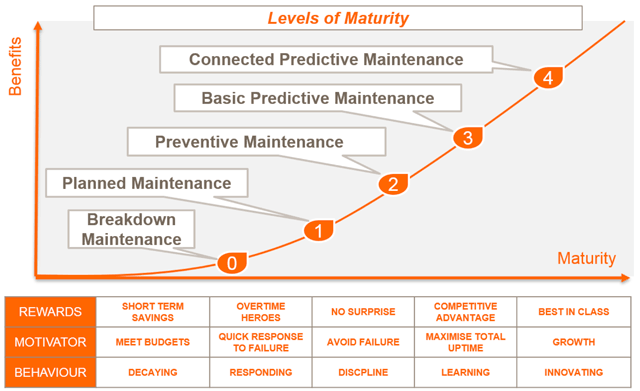
There are some easy-to-grasp elements, however:
- Motivators – What does the organisation want the culture to be, and how does that fit with the behaviour that the people in the maintenance operation see? This is described as the motivators of the maintenance operation, and it is clearly bound up in the behaviour of the operation’s leadership. The importance of short-term budget adherence is played against the longer-term results of a proactive operation. People can easily see when there is a mismatch between the real motivators and the stated objectives of the company. It is clearly not effective for an organisation to say that high equipment reliability is important and yet not give people the time and resources to do what is necessary to prevent equipment failing.
- Rewards – What does the maintenance operation visibly reward? Constantly rewarding people for returning broken equipment into use but ignoring the engineer who diligently works at preventing breakdown will not result in a proactive maintenance organisation – it just causes frustration. Proactive operations are those that visibly and loudly “applaud” when a long-term reliability issue is prevented from recurring, and are seen to divert resources to tackling the key reliability issues rather than short term cost cutting.
- Behaviour – What is the resulting behaviour of the operation? As capabilities are acquired, and better results seen, this spurs on the reinforcement of a proactive culture. This generally results in more people being dedicated to conducting preventive maintenance tasks, and eventually the creation of the space to test, experiment and learn from mistakes that brings true innovative improvement.
The maintenance maturity of an operation and its culture are directly linked, simply because it is not normally possible to develop the range of capabilities necessary to be a high performing maintenance operation without the supporting cultural focus, rewards and recognition.
By choosing the right rewards, and the right motivators, an organisation can promote the organisational culture that it wants to see.
Conclusion: Becoming the proactive maintenance operation
Defining an effective maintenance strategy for an organisation is a wider task than simply deciding how to maintain each individual asset.
Although the reliability and safety requirements of the organisation’s assets should be at the core, a robust strategy also defines what capabilities the maintenance team needs, and aligns all the efforts of the equipment designers, users and maintainers towards a proactive maintenance culture.
When strategy, capability and culture come together the results can be a proactive maintenance operation that provides strategic advantage in the marketplace and adds real financial value to the parent organisation.
References
[1] Figure 2 – taken from slides from IMaintain Conference 22 March 2012 from Accenture – Marc Hoppenbrouwers (Accenture) and Marc Couturier (SAS) titled Analytics opens a new dimension for maintenance (Breakfast Masterclass)
[2] Figure 6 – adapted from Ledet, W.J., Making the move toward a learning organisation – a classic journey of change. 2002
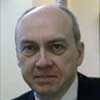
Paul Adams
Maintenance Strategy Manager, GlaxoSmithKline