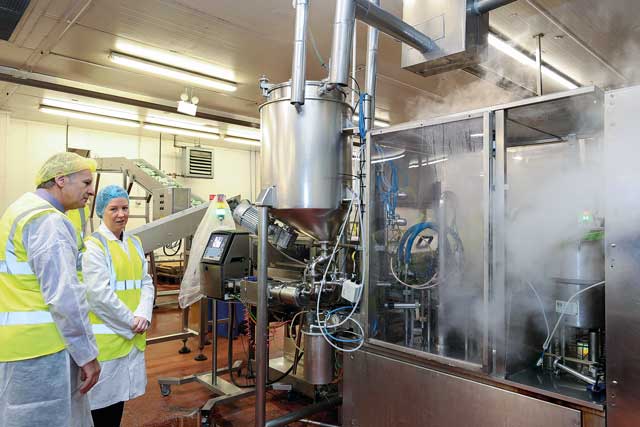
Changing to clean steam in its packing process helped a baby food manufacturer differentiate itself in a crowded market. Francisco Pedrosa, regional clean steam specialist at Spirax Sarco, explains how it was done in partnership with food product packer, Natural Fruit and Beverage Company.
In late 2017, Jamie Walker, manufacturing manager at the Natural Fruit and Beverage Company, a processor and packer of food products into resealable pouches, was approached by a key customer looking to enhance the quality of its product – baby fruit puree sachet pouches. The customer wanted to differentiate itself from its competitors and win future supermarket contracts.
Until then, the customer had been using carbon dioxide for purging and cleaning excess residue before capping the product. It was becoming apparent that, while competitor products were improving in quality, carbon dioxide was offering no room for improvement, and was also an expensive resource.
An alternative method had to be sourced. Mr Walker sought advice from existing suppliers and peers in the industry to see what alternatives were available. After speaking to a number of experts, he decided to follow up on the recommendation to use steam.
Clarity on steam
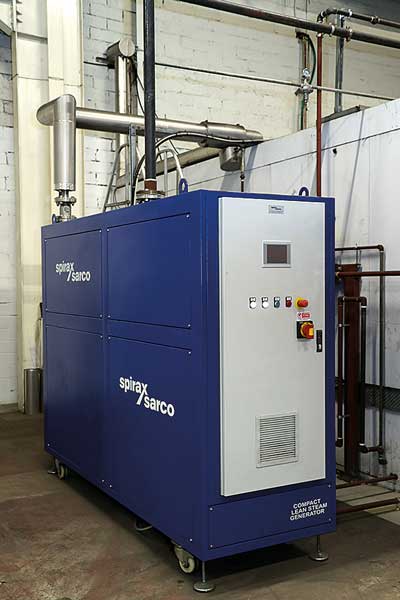
He discovered that there is more to understand than just one type of steam, and this started to raise questions about potential contamination of the pipework running the risk of affecting the consistency of the product. He called on Spirax Sarco for guidance.
Spirax Sarco was invited to make a presentation to the management team. It explained the difference between filtered steam and clean steam, the concept of clean steam as an ingredient, and how it applies in relation to a food safety management system based on Hazard Analysis and Critical Control Point (HACCP) principles.
As a result, Mr Walker was confident that a clean steam solution would be his best option.
Filtered versus clean steam
Filtered steam is often used for direct injection and is passed through a filter which removes 95% of particles larger than two microns. This still leaves 5% of particles larger than two microns, as well as those smaller than two microns, which can significantly affect the final product – leaving it at risk of contamination as well as affecting quality, taste and colour.
Generating and using clean steam in a process means controlling feedwater quality at the source. Rather than relying on a filtration process to extract particles, the production of clean steam uses a secondary steam generator with the ability to control chemical-free feedwater quality.
The design of the steam distribution network, material selection and installation practices are all critical for minimising steam degradation and ensuring acceptable purity and quality at the point of use. For this reason, clean steam requires the use of stainless steel pipework and components that eliminate the potential for corrosion of pipeline equipment made from traditional carbon steel materials.
A clean steam solution
The Natural Fruit and Beverage Company went ahead and introduced an electric compact clean steam generator of 50kW (50kg/h @ 3 bar) with preheating capability and the ability to control feedwater quality.
Since installing the new solution, Spirax Sarco has supported the Natural Fruit & Beverage Company with regular site visits.
There are many companies across the country that use the same processes as Natural Fruit and Beverage Company, and yet do not realise the full potential of clean steam. Spirax Sarco is happy to offer a consultation to advise on where they might be able to improve.
For more information on clean steam, visit:
beta.spiraxsarco.com/global/en-GB/products/clean-steam