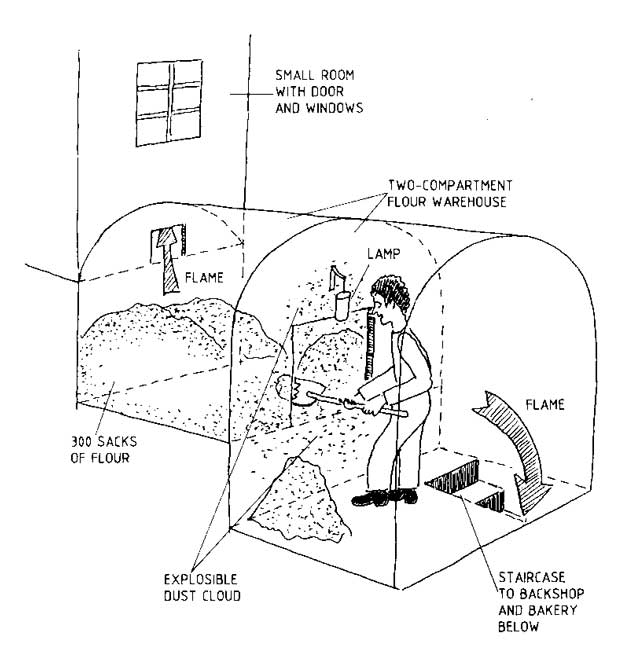
Declan Barry, managing director of ATEX Explosion Hazards Ltd, outlines the essential elements of safe working in potentially explosive atmospheres
The first recorded dust explosion took place in Italy in 1785 and was believed to be due to the dryness of the corn after a good summer. In reality it was caused by a boy shovelling corn dust under a naked light. Recent incidents prove that such misunderstandings are still prevalent today.
If in your workplace there is a risk of creating dust, there is a possibility of creating an explosive atmosphere.
Under the EU ATEX Directive (ATEX 137 updated to 153), and the Dangerous Substances and Explosive Atmospheres Regulations 2002, employers must classify into zones areas where hazardous explosive atmospheres may occur. The classification given to a particular zone, and its size and location, depend on the likelihood of an explosive atmosphere occurring and its persistence if it does.
Areas classified into zones (0, 1, 2 for gas-vapour-mist and 20, 21, 22 for dust) must be protected from effective sources of ignition.
An area is defined as Zone 20 (“Continuous”) if there is a risk of an explosive atmosphere for over 1000 hours per year, Zone 21 (“Occasional”) if there is a risk of an explosive atmosphere for 10-1000 hours per year, and Zone 22 (“Not Likely”) where the risk is less than 10 hours /year, and each has different requirements affecting potential ignition sources.
In many cases zoning alone will not be enough to solve the potential problem.
Basis of Safety
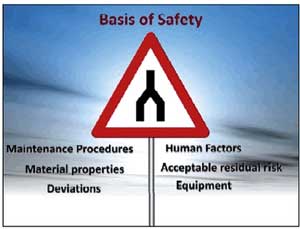
It is important when examining your plant for explosion hazards that you establish your Basis of Safety.
Maintenance procedures should be in place to define methods by which equipment and plant can be safely (for the maintenance team and the plant), promptly and economically restored to safe, effective and efficient operating conditions.
Human factors: Training of maintenance employees should enable tradesmen to undertake maintenance work effectively, so that they themselves are safe and that they do not jeopardise the safety of the plant or the people who work in it.
Material properties: identify the hazard. Is it explosive? Identify its minimum ignition temperature (MIT); minimum ignition energy (MIE); lower explosion level (LEL – typically 30 to 50mg/m3); the explosion severity of the hazard (KST/ Pmax); and its thermal stability (is the hazard exothermic: that is, can it self-heat like coal, wood pellets and milk powder?).
Acceptable residual risk: Is the risk or danger of an event, with all the prevention and protection measures applied, acceptable to the organisation’s targets for, and approach to, safety?
Deviations: Written procedures should be in place which ensure that all modifications are authorised only by competent personnel.
Equipment: Equipment and protective systems in the places where hazardous explosive atmospheres may be present must be chosen in accordance with the categories in the European ATEX Directive 114, unless otherwise provided in the explosion protection document, on the basis of the risk assessment.
Sources of ignition
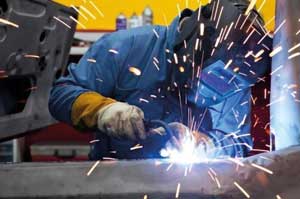
Standard BS EN 1127-1:2011 Explosive atmospheres. Explosion prevention and protection. Basic concepts and methodology includes 14 types of ignition source, from hot surfaces and mechanically generated sparks to stray electrical currents and ionising radiation.
In 1888 J Reynolds & Sons posted a notice which we would now recognise as an early example of an Explosion Protection Document: Never enter any sieve or dusty room with a naked light. Where it is necessary to sweep or dust at night, do it as quietly as possible to avoid agitating the dust. Should any man exhibit carelessness in this respect after this warning, we shall be obliged to dismiss him.
A modern version of J Reynolds advice would include the following:
Organisational measures must be taken where technical measures alone cannot ensure and maintain explosion protection at the workplace. In practice, the work environment can also be made safe by combining technical and organisational measures.
Worker competence: The employer must provide those working in places where explosive atmospheres may occur with sufficient and appropriate training with regard to explosion protection. This includes management to the highest level.
Worker supervision: In working environments where explosive atmospheres may arise in such quantities as to endanger the safety and health of workers, appropriate supervision during the presence of workers must be ensured, in accordance with the risk assessment, by the use of appropriate technical means.
Permit-to-work system: If work liable to cause an explosion is to be carried out in or near a hazardous place, it must be authorised by the competent person with responsibility for this function within the establishment. This also applies to activities which may interact with other work to cause hazards. A system of “permits to work” has proved useful in such cases. This may be implemented by means of a permit-to-work form, which all concerned must receive and sign.
Since the J Reynolds notice is no longer sufficient, you may be best advised to seek the advice of a consultant with the appropriate competence to get you through the mire that is now ATEX/DSEAR compliance.
Further information: info@inburex.co.uk
or declan@explosionhazards.com