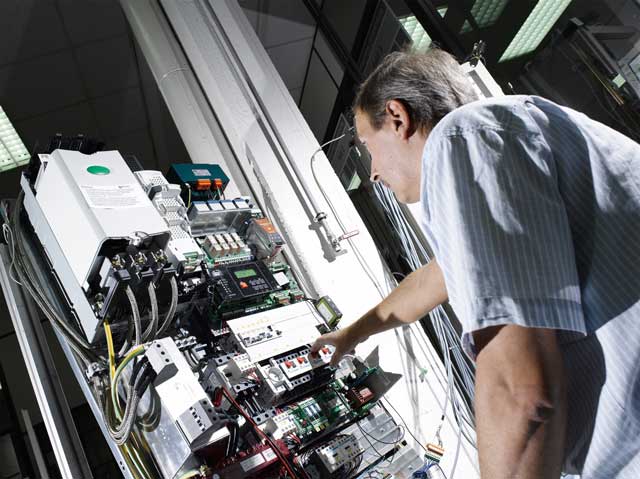
For common engineering systems such as fans, pumps, compressors, HVAC systems, conveyors and elevators, drives provide essential control and efficiency. Stephen Turner, Control Techniques product management director, provides a back-to-basics guide to the most common drive types of today.
Most modern industrial processes or systems function at different speeds. A humble production line conveyor, for example, is likely to be run at a variety of speeds to suit different products. Its motor, therefore, will require some degree of speed control. Similarly, process conditions might demand adjustment of flow from a pump or fan. Using a drive with variable speed capability will improve system efficiency and save energy..
In its most basic form, a drive is a device that harnesses and controls the electrical energy sent to a motor. Electricity is fed into the motor by the drive in different amounts and at varying frequencies, thus controlling the motor’s speed and torque – and subsequently that of the load, such as a lathe spindle, for example.
Drives offering a degree of adjustable speed capability have been around for decades. Before electric motors were invented, mechanical speed changers were used to control the mechanical power provided by waterwheels. The first types of drive to make their way into the industrial arena were purely mechanical, often called variators.
Mechanical drives
The typical operating principle for a mechanical drive was based on variable-pitch pulleys, which were spring-loaded and could be expanded or contracted in diameter by means of a hand crank. Cranking the mechanical drives in this way provided the ability to change output speed in line with requirements.
As with many mechanical devices, however, this type of drive fell out of favour because of a tendency to break down, and general inefficiency. In fact, the efficiency of such drives could sometimes drop to less than 50% if the belt slipped on the pulleys. Another drawback was restrictions in the speed range due to fixed diameter settings.
Hydraulic drives
Typical types of hydraulic drive include hydrostatic, hydrodynamic and hydroviscous. In most configurations, a pump is used to accumulate the necessary operating pressure so that a hydraulic motor can generate its rated power. Speed control is provided via a control valve: the more the valve is opened, the more fluid passes through the system and the faster the motor runs. Hydraulic motors can produce high levels of torque, but there are a number of limitations, not least the need for a hydraulic system, including hoses, fittings and fluid, and all the associated risks of leaks and the need for maintenance.
Electric drives
Electric drives embrace a number of different types, including DC, eddy current, AC and servo drives, for example. Control can be either manual or automatic.
Eddy current drives
This drive type comprises a fixed speed motor and an eddy current clutch. The controller provides closed loop speed regulation by varying the clutch current, only permitting the clutch to transmit sufficient torque to run at the desired speed. Speed feedback is typically provided via an integral AC tachometer. Eddy current drives have lost their place to variable frequency drives in most applications that require speed fluctuation, although they can still be found on certain types of machinery where only simple motion is needed, such as a stamping press..
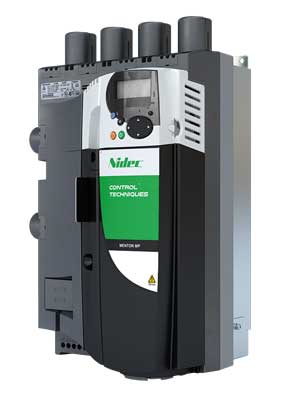
DC drives
Before the advent of the latest variable frequency AC drives, it was DC drives that provided the backbone of industry, probably as far back as the 1940s. Then, DC drives were based on mercury-arc rectifiers, a type of vacuum tube, to provide the required power conversion. The first solid-state devices did not arrive until the 1960s, with the silicon-controlled rectifier (SCR), or thyristor, as accommodated by modern DC drive systems.
DC motors house a separate magnetic circuit called the field, the magnetic field strength of which can be independently controlled by the drive. Interaction between the motor armature and field turns the motor shaft.
The technology for DC drives is widely considered to be mature, but in truth it is still evolving. Today’s advanced DC drive systems are designed to offer maximum motor performance, improved system reliability and the ability to interface digitally with modern control equipment using Ethernet and fieldbus networks. Specific benefits of the latest systems range from easy set-up and commissioning, through drive intelligence and system integration, to flexible machine communications.
A continuing requirement is the modernisation of existing high-power DC installations, by simply replacing the DC drive. This is possible because high power DC motors typically have a long life, and the customer can move to the latest control system technology for a much lower cost without replacing the DC motors.
AC drives
First, the terminology, which unfortunately varies. Generally, the term adjustable speed drive (ASD) is used when speed can be chosen from a number of pre-set ranges. If the output speed can be altered without set steps, the terms variable frequency drive (VFD) and variable speed drive (VSD) have become more prevalent.
VFD/VSD technology originated with wound-rotor induction motor (WRIM) drives, which functioned using slip control. However, along with eddy current drives, WRIM drives have lost popularity because of their inferior efficiency and the increased maintenance of slip ring brush gear.
In their place are the VFDs of today, which in their most basic form function by adjusting the power frequency supplied to the motor. Essentially, an AC drive converts AC power to DC power, which is filtered and converted back to AC power, but with a variable voltage and frequency. In comparison with DC drives, a more compact footprint and lower purchase and installation costs are among the advantages, although not in all applications.
Modern VFDs can help to reduce environmental impact by allowing the use of state of the art high-efficiency motor types. Synchronous reluctance and hybrid-synchronous reluctance motors can replace induction motors in many applications and offer an attractive return on investment through significantly reduced running costs, without sacrificing motor robustness.
The latest AC drives provide high-performance motor control and ultimate flexibility to satisfy the requirements of machine builders, and in other high-specification applications across industry. High bandwidth motor control algorithms are supported by flexible speed and position feedback interfaces. Such drives have been developed so that flexible control systems can be created, either centralised (mounted in the control cabinet) or decentralised (mounted to the motor or nearby wall). Intelligence is the key, with the latest AC drives featuring on-board PLCs and real-time Ethernet to provide fast communication and accurate axis synchronisation.
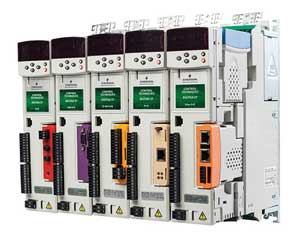
Servo drives
Servo drives, which are inherently linked to servo motors, are today found widely in applications such as CNC machine tools, factory automation systems and robots. The principal difference of a servo system from other drive systems is the precision of the motor feedback, the dynamics of the control and the motion achieved through the application of high-speed control loops.
Servo drives can be divided into two broad categories: simple amplifiers, and intelligent drives comprising built-in motion control. When a simple amplifier type servo drive receives a reference command signal, typically the desired position or speed, from the external motion control system, it controls the power to the motor to minimise the error between the actual position/speed and the reference.
Intelligent servo drives expand on the capabilities of the amplifier type by bringing the motion control capability and usually some level of software programmability on to the drive itself. Such drives can eliminate the need for the external motion controller and significantly reduce the overall cost of the system.
Today’s servo drives offer exceptional power density and a small footprint, to allow them to be installed in compact control cabinets. They have the flexibility to operate both stand-alone and as followers in a system, making machinery that would have once comprised multiple mechanical cams driven from a common line-shaft a thing of the past. They offer the benefits of greatly simplified mechanics, reduced maintenance, higher machine throughput and flexibility of control.
Closing thoughts
As when selecting any engineering device, correctly specifying a drive very much depends on the specific application. Some say that drives have almost become a commodity item in control system design. However, while it is true that some ‘no-brand’ speed control devices can be bought online for very little outlay, variable speed drives and the motors they control have developed dramatically in the past few decades, with their capabilities continuously expanding to bring more value to the engineers that use them. The application of drives will continue to play a strategic part in the reduction of environmental impact and the profitability of machinery.
If any degree of reliability, longevity or intelligence is required, seeking the advice of a reputable drives manufacturer with the capability to provide support throughout the machine lifecycle will always pay dividends in the long run.