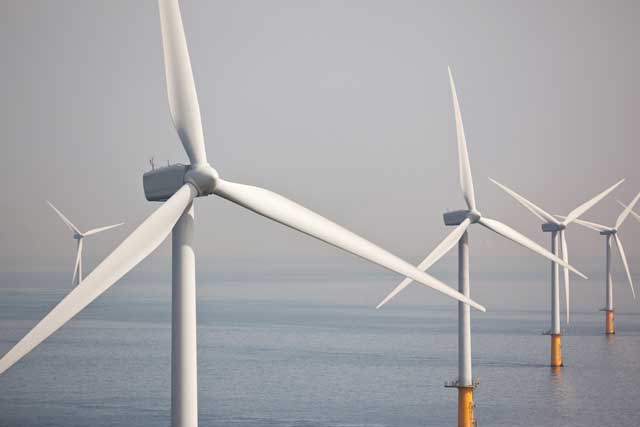
Industry 4.0 technologies including drones are making maintenance of wind turbines in extreme environments easier and safer, says Richard Tucker, general manager B2B lubricants and supply chain technology, Shell.
Recent industry innovations, such as the introduction of drones, have signalled that Industry 4.0 has well and truly arrived in the wind sector.
Drone maintenance is already starting to make a big impact elsewhere in the energy industry. Shell uses drones to inspect flaring stacks at some of Europe’s biggest gas plants and to check gas-safety levels at natural-gas terminals. As the push for more renewable energy sources continues, it seems fitting that the wind sector is up next for the data-based maintenance revolution.
Wind turbines are often located in remote, hostile environments, so an effective maintenance strategy is key to minimising unnecessary human-machine intervention and reducing costs and safety hazards. Drones can help to achieve this in a number of ways.
- By making turbine inspections easier, safer and faster: companies are using drones to inspect and carry out testing in a way that’s faster and less risky, even in extreme environments. With the latest models processing thousands of images while the drone is still in the air, engineers can fault-find faster and with greater accuracy, without exposing themselves to harsh weather conditions or unnecessary risks. The combination of stable and sophisticated airborne drones with artificial intelligence and advanced wind farm analytics is set to revolutionise turbine maintenance.
- Carrying out routine maintenance tasks: applying a repair to the right point of a 39m blade that’s 100m up in the air is never an easy proposition for a human engineer. Now technology company 3M is teaming up with drone specialists Camp Six Labs to develop drones that can apply the wind protection tape used to protect blade surfaces from erosion and minor damage, while the operators keep their feet on the ground.
- Deliver heavy payloads: the Griff 350 can carry payloads of up to 150kg. Such heavy-duty drones can greatly simplify the task of getting tools and equipment to the right part of the turbine, making maintenance of even the tallest wind turbines easier and cutting the risk of injury.
- To fight turbine fires: fire is one of the leading hazards in the wind power industry. And fire-fighting in remote locations at high altitudes can be extremely difficult. Using specialised fire-fighting drones, crews can be on site and take effective action faster than ever before.
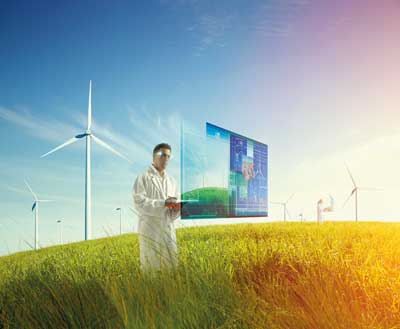
Technologies such as drones are bringing a range of new and more efficient ways to tackle maintenance challenges. But to achieve the potential savings attainable, it is essential that these are paired with complementary measures such as proper equipment lubrication.
A recent Shell Lubricants survey, based on 350 interviews with power sector staff in seven countries, showed that 73% of power industry professionals thought using Industry 4.0 technologies would lead to fewer equipment breakdowns. However, as these technologies become more commonplace, lubrication must remain a crucial part of the maintenance regime: 43% admitted often experiencing breakdowns as a result of ineffective lubrication.
The use of high quality lubricants is vital to helping minimise downtime and increasing wind turbine output, and at Shell our specialists work closely with customers to see that they have the products, the training and the expertise they need to handle lubricant products and optimise operations.
By combining the quality consumables and components with emerging technologies, AI fault-finding engines, and intelligent sensors using big data to connect, the industry will be able to improve wind turbine efficiency just as demand for wind power booms.
For more insights see www.shell.com/business-customers/lubricants-for-business/sector-expertise/power-industry/wind-power/what-will-the-wind-power-industry-of-the-future-look-like.html
e: productinfo-uk@shell.com