Keeping a handle on lubrication is easy, right? All you need to do is make sure the right lubricant is used in the right amount and at the right time. Not so fast; if only it were that simple.
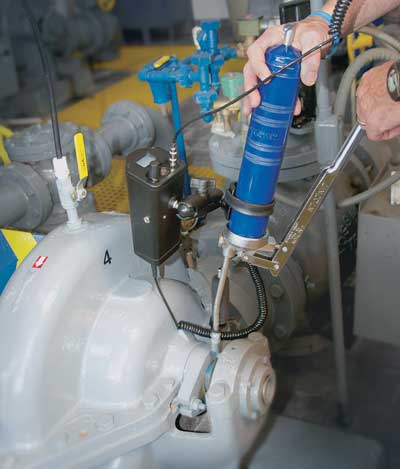
It has been estimated that 60-90% of all bearing failures are lubrication related. Bearing failures most often lead to unplanned downtime which can impact production as well as affect all related components around the bearing. Downtime is costly. Since the most common cause of bearing failure is lubrication related, it’s clear to see that lubrication is serious business. And for the longest time, that “serious business” has been conducted in a way that on its face makes perfect sense – but in fact borders on the haphazard.
Time-based lubrication leads to over-lubrication
Many technicians, unfortunately, have relied on “preventive”, time-based lubrication alone. That is, every x months, the grease gun comes out, and the bearings are lubricated. But by relying solely on time-based lubrication, or even a combination of planned maintenance and temperature readings to serve as a proxy for lubrication status, one runs the risk of something just as bad, if not worse: over-lubrication. In fact over-lubrication has been reported both anecdotally and in presentations at various conferences to be the primary cause of premature bearing failure.
Relying on time-based, periodic lubrication assumes bearings need to be greased at defined time periods. Often this evolves into a well-intentioned guessing game at best. Adding more lubrication to a bearing that is already adequately greased is a real risk.
How ultrasound improves lubrication practices
Ultrasonic equipment detects airborne and structure-borne ultrasounds normally inaudible to the human ear and electronically transposes them into audible signals that a technician can hear through headphones and view on a display panel as decibel (dB) levels. With this information, a trained technician can interpret the bearing condition in order to determine what, if any, corrective action is needed.
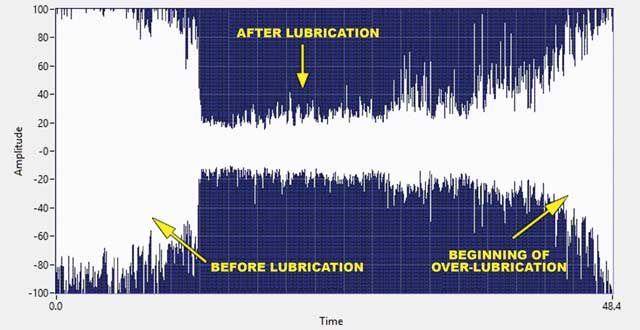
Figure 1 is a Time Wave Form of a recorded ultrasound of a bearing in the process of being lubricated. The approximately 1-minute sound file shows the bearing before and after lubrication. Notice the obvious reduction of ultrasound noise on the sound spectrum – this would also be clearly noticed by the inspector listening to the bearing via the headphones. The sound would get smoother as the bearing was lubricated.
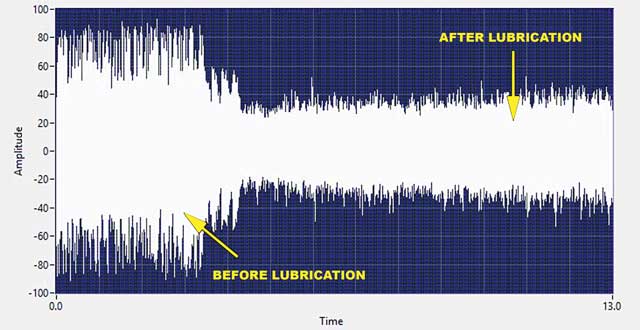
Figure 2 shows the bearing dB and amplitude increase as more grease is added and the threshold of over-lubrication is reached. This can be avoided by listening to the bearing with an ultrasonic instrument, or keeping an eye on dB levels.
How to get started
- Select your ultrasound instrument
The first step is to use a proper ultrasound instrument. There are instruments especially designed for bearing lubrication and that can even be attached to a grease gun. - Establish baselines
It is necessary to establish a baseline decibel level and get a sound sample. This is ideally done when moving through a route for the first time, by first comparing dB levels and sound qualities of similar bearings. Anomalies will be easily identified. - Trend your bearings
Once established, each bearing can be trended over time for any changes in either amplitude or sound quality. Generally speaking, when the amplitude of a bearing exceeds 8 dB and there is no difference in the sound quality established at baseline, the bearing needs to be lubricated. To prevent potentially disastrous over-lubrication, the technician will then apply lubrication a little at a time until the dB level drops. - Collect Data
To improve efficiency, it is good practice for the technician to note when the equipment was last greased and how much grease was used, to calculate roughly how much lubrication is used per week. By using ultrasound to lubricate each and every time, the technician produces historical data that can be used as a guide from previous calculations, helping the department to determine whether the lubrication schedule can be modified, perhaps saving staff-hours, and whether the manufacturer’s suggested lubrication amount is accurate (if less is needed, there’s cost-saving potential).
Chris Hallum – UE Systems Europe
Regional Manager UK & Ireland
+44 7930 352 188
chrish@uesustems.com
www.uesystems.co.uk