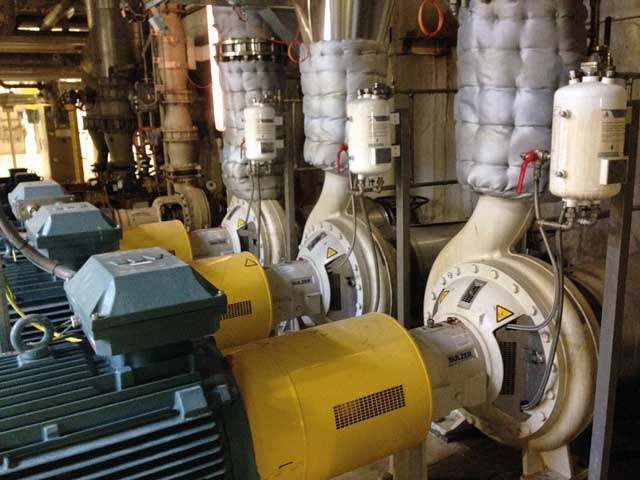
A seal energy audit can help companies meet sustainability targets as well as improving pump reliability and reducing operational costs. Tom Grove, chief executive of AESSEAL explains how.
Mechanical seals account for a tiny percentage of the total power consumption of any one pump. It’s therefore easy to see how this component can be overlooked by managers seeking to target energy losses and improve efficiency.
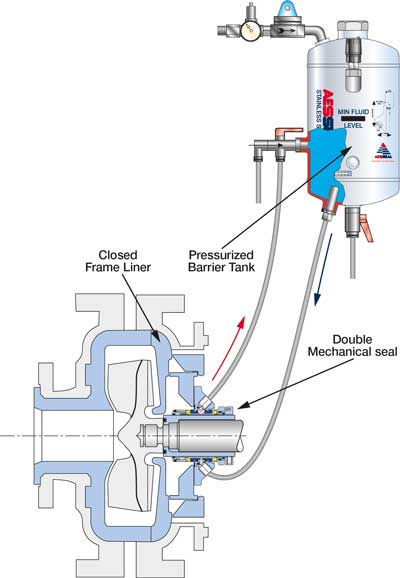
With the exception of gas-injecting seals, a large proportion of mechanical seals in all industries are set up with a clean flush liquid to provide lubrication, prevent overheating and maximise their reliability and lifespan. The flush liquid is provided from a separate seal support system or “piping plan” – and the energy that can be lost if the piping plan is inefficient can be substantial.
With hot processes, cool liquid from a flush system is injected into the process stream, so that the process stream must be reheated to compensate. Some piping plan configurations remove part of the process fluid and cool it in a heat exchanger before reintroducing it to the process stream, which all requires reheating. Evaporation may also be required where cool liquid has been added to the process, again leading to increased energy use. The judicious selection of piping plans is therefore of great relevance across all industries looking to optimise efficiency and reduce costs.
Businesses committed to the ISO-50001 standard for energy management systems recognise the mechanical seal as a potential culprit when seeking to identify unnecessary power consumption.
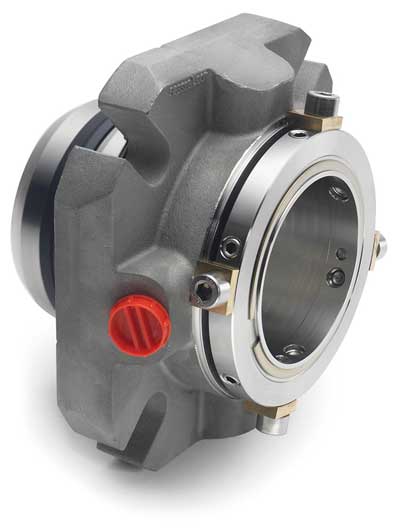
A simple and low-cost way to identify the potential energy waste is by carrying out a periodic seal energy audit. This involves inspecting each piece of equipment, recording seal arrangement, support system configuration, process data and seal system parameters such as water flow and temperature. Existing plant data is collected and heat flow calculations performed, making it possible to calculate the energy impact of each individual mechanical seal on the plant, identify where energy use is high and review options for reducing it.
An audit report is then produced, providing the company with potential opportunities for a more efficient piping plan configuration, the investment required to upgrade and the potential returns. This provides a “quick-win” overview, identifying opportunities which can bring about significant reductions in energy use for minimal outlay, while also improving the efficiency of seal and support systems and, consequently, pump reliability.
For companies which elect to upgrade to the environmentally friendly “continuous loop” seal support systems developed in recent years, energy conservation goes hand in hand with water conservation. These manage water sustainably by employing an integral vessel to store flushing water for continuous recycling. The barrier fluid is circulated to and from the mechanical seal by the thermo-siphon effect, a method of passive heat exchange which circulates the fluid, minimising waste as well as providing more efficient cooling.
Seal energy audits can provide an important communication bridge between the plant maintenance reliability personnel, who often make decisions about piping plans in isolation, and operational stakeholders responsible for energy consumption, who might have limited knowledge of how seal piping plans affect wider energy use.
Investment in a seal energy audit can bring long-term reliability improvements, cost savings and concrete environmentally sustainable practices. They should be central to any responsible company’s maintenance plans.