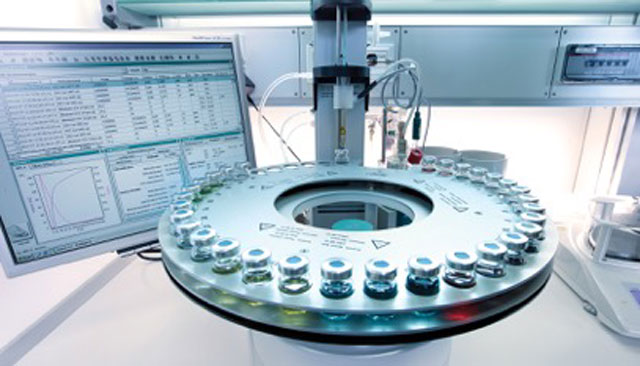
Selecting the right lubrication products and using them in the correct quantities is essential in industry for optimum performance and reliability and longevity of expensive production machinery. For an average production plant, lubricant purchases normally amount to only 3% of a maintenance budget, but lubrication-related activities can influence an estimated 30% of total maintenance costs.
Industrial oil manufacturer Fuchs Lubricants has recently upgraded its Fluids Live monitoring system. Fluids Live is an easy to navigate web-based recording, tracking and reporting tool with integrated KPI measurements.
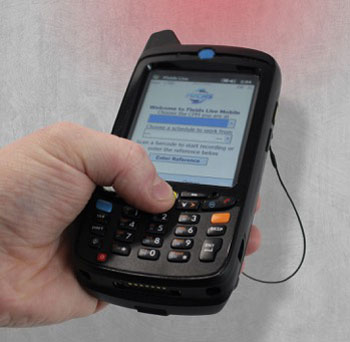
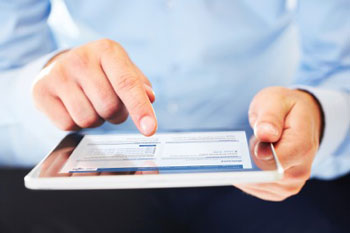
It is designed to provide customers with instant access to key data, allowing faster and more informed decision-making to help maximise reliability through an effective lubrication strategy.
Keith Salt, of Fuchs Lubricants’ industrial division, said: “Fluids Live is proving extremely popular among our industrial customers, with more than 100 manufacturers already signed up globally. It’s all about gathering information of what manufacturers are doing, or not doing, and using it to improve reliability.”
The software is designed by an internal team which also provides the optimum lubricant settings to suit the needs of customers.
“The whole idea is to obtain information from measurements such as oil sampling and vibration monitoring and to ensure we maximise asset care. It’s all designed to cater for increasing skill shortages and to take the guesswork away,” Mr Salt adds.
Fluids Live provides crucial lubrication measurements including history of fluid usage, lubrication routes completed, exception reporting and associated costs of lubricants.
The software is portal driven, allowing management teams from companies in the same group the ability to view other site information and share best practice both locally and globally. Mr Salt added: “Most software packages are sold with licence fees but customers using our lubricants enjoy free use of the software.”
The company stresses that the basic principles of lubrication should not be forgotten, and offers lubrication training to make sure customers’ machinery gets the right lubricant, in the right quantity, at the right time.
“The starting point of an effective lubrication programme always has to be the detailed mapping of all machine lubrication points, their working conditions, lubrication requirements and practicality,” said Mr Salt.