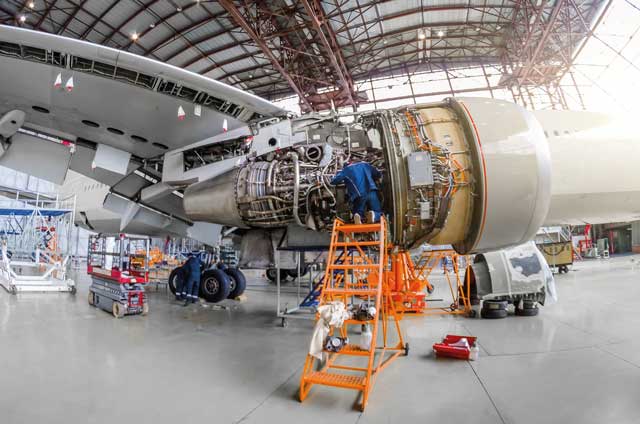
Does reliability centred maintenace still have a role in the age of the internet of things? Sandy Dunn, managing director of consultant Assetivity, believes its underlying principles continue to make it relevant.
When reliability centred maintenance (RCM) first came on the scene, it started a major shift in the way that people thought about preventive maintenance and the way that they went about developing preventive maintenance programmes. With its roots in the aviation industry of the 1960s, it may be tempting to think that RCM has “had its day”, and is no longer relevant in the age of the industrial internet of things (IIoT) and predictive analytics.
However, RCM contains some underlying concepts and lessons that remain just as relevant today as they always have, and RCM itself is continuing to evolve to meet the challenges of the digital age.
Three fundamental principles
While there are a number of “standards” for RCM – with differing levels of prescription regarding the decision-making process for preventive maintenance task selection – all these standards and processes have, at their heart, three key principles that I believe are universal and will prove to be timeless, regardless of the advent of newer technologies.
Principle One – We don’t do maintenance for maintenance’s sake. We do it to avoid the consequences of failure.
The purpose of preventive maintenance is not to avoid equipment failures. Instead, It is undertaken in order to avoid the consequences of those failures. This wide-reaching principle leads us to understand:
- That it is quite possible (and may be optimal) to have different preventive maintenance tasks for identical equipment operating in different areas of a given plant, depending on their operating context and consequences of failure
- The value of condition-based maintenance. Predicting when something is about to fail does not prevent the failure – but it does allow you to avoid or mitigate the consequences of that failure (normally by conducting a corrective maintenance activity before the item fails in-service).
Principle Two – To be effective, the preventive maintenance programme must be aimed at addressing failure modes – the causes of equipment failure.
It is necessary to understand the underlying causes of failure in order to make sure that a preventive maintenance programme is effective. Once again, identical equipment operating in different conditions may have different causes of failure.
Principle Three – Most items don’t wear out
The work performed by Nowlan and Heap when developing RCM indicated that most items do not wear out. They found that there were six failure patterns, and the proportion of components that they studied that complied with each failure pattern is illustrated below.
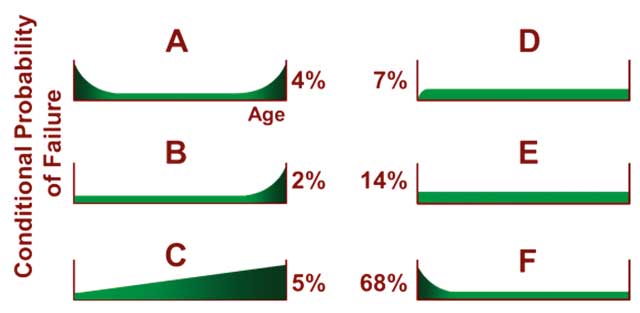
The results of the study generated a paradigm shift in the way engineers think about equipment failure. If items do not wear out, we cannot prevent failure by replacing them at a set point.
Indeed, in the majority of cases (failure pattern F), fixed time replacement makes things worse. So it is necessary to understand the underlying failure pattern that is associated with the cause of failure in order to identify the most appropriate preventive maintenance action.
RCM, IIoT and predictive analytics
The three principles outlined above are, I believe, timeless and universal. However, some other elements of RCM and its application will need to evolve in the context of IIoT and predictive analytics algorithms.
First, while RCM has always embraced the analysis of available reliability data in its decision-making process, it does not require this data. One of its strengths is that sensible decisions can often be made in the absence of extensive data.
However, the advent of IIoT means that much more (and better quality) data will become increasingly available to RCM analysts and teams for their use. In my experience, few RCM practitioners effectively use this data as an input into the decision-making process, and the quality of decisions suffers as a result. Many RCM practitioners will need to become much more familiar with the mathematical and statistical aspects of reliability analysis than they currently are.
Second, as mentioned earlier, RCM has led to a much greater focus on condition-based (or predictive) maintenance as a strategy for avoiding the consequences of equipment failure. In a traditional RCM approach, failure modes are assessed one at a time; for each failure mode, if a condition-monitoring task is feasible, a single “condition” is identified to be monitored – for example, vibration, noise, oil condition, and so on. However, with the advent of IIoT and predictive analytics algorithms, a number of conditions can be monitored simultaneously, and various combinations of these conditions could be the trigger that instigates a corrective action.
At present, traditional RCM decision diagrams do not explicitly consider the use of continuous asset health monitoring, how to determine the alarm points resulting from multi-variate regression models or those based on machine learning, or how to determine the required response times for any ensuing corrective action being initiated in response to an alarm generated by one of these models. RCM decision processes will need to evolve to incorporate and embrace this new reality.
Conclusion
In my view, RCM, and the three core principles embedded in it, remain vitally important for determining the optimum preventive maintenance programme for a given item of equipment in its present operating context – especially when dealing with simpler, non-heavily instrumented equipment.
As regards its application to equipment fitted with real-time equipment health monitoring sensors – particularly if the data from these sensors is used to power sophisticated predictive analytics models – it has some conceptual application, but in practice may need further extension and development to deal with these emerging technologies.