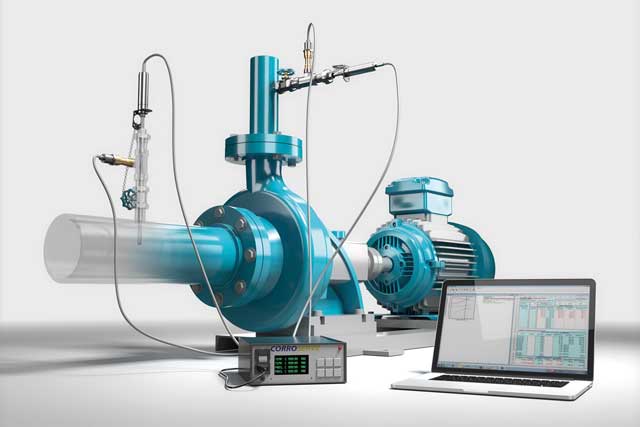
Every organisation that uses pumps seeks to maintain their performance and optimise efficiency. Corroserve pump manager Simon Cappleman explains why thermodynamic pump monitoring is accepted as providing the most accurate measurement of pump performance.
The thermodynamic method of monitoring pumps is based on the first law of thermodynamics. That is, the increase in the internal energy of a thermodynamic system is equal to the amount of heat energy added to the system, minus the work done by the system on its surroundings., In basic terms, the energy losses in the pumping process result in a temperature rise in the fluid.
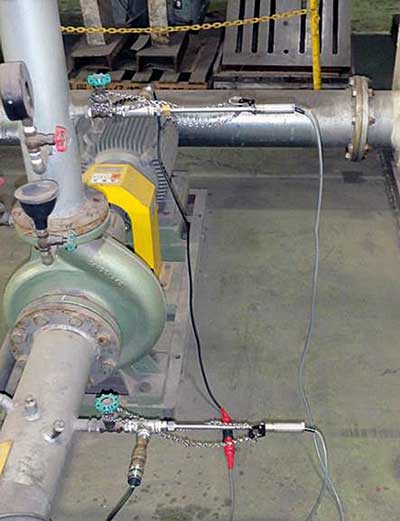
The concept of the centrifugal pump is based on Bernoulli’s principle that there are three forms of energy in a fluid system – potential, kinetic and pressure. Kinetic energy and potential energy are the thermodynamic properties of the fluid system and the two energy quantities of heat and work are required to account for real world conditions.
The thermodynamic method for pump testing requires the following data: temperature of the pumped fluid at pump suction and pump discharge; suction and discharge pressure; motor input power and motor efficiency. To measure the energy losses dissipated as heat, corrections are applied for the specific heat and density of the pumped fluid.
To use the technique in practice, Corroserve’s test engineers use the client’s monitoring system to take readings from a fully open discharge valve until any fluctuations in temperature have settled out. The engineer will then continue to take readings for a predetermined amount of time at set points of the discharge valve until the valve is fully closed. This allows the pump curve to be mapped from the fully open to fully closed position of the discharge valve. The pump curve is then compared with the original test curve of the pump, when any losses in performance or increase in absorbed power will signify signs of wear.

As running clearances open up between the wearing parts of the pump, the leak paths for the pumped fluid increase, resulting in lost efficiency. A thermodynamic monitoring system detects and records these losses more accurately than other test method. During the test a filter can be adjusted to take readings from every 2 seconds up to every 3.3 minutes. This allows the system to achieve a steady reading of ∆T (temperature differential). ISO standards recommend a fluctuation of ∆T less than or equal to 5mK/min.
Corroserve uses the latest thermodynamic pump monitoring equipment to monitor the performance of any Class C industrial centrifugal pump over its working life. The degree of accuracy of the test for centrifugal pumps is to ISO 5198 part III (formerly ISO 2548). The mathematical basis of the software only allows centrifugal pumps to be tested by this method.
The monitoring equipment measures pressure, temperature and power input. This information is used to calculate flow, which eliminates the need for a flow meter. As a result, tests can be carried out on equipment with only short lengths of straight pipe – two diameters – at the suction and discharge. Conventional testing methods require a length of straight pipe equal to at least five diameters.
A TPM data sheet is provided to the pump user: this can be compared against the original manufacturer’s test results when the pump was new. A report is issued showing what efficiency gains could be expected following manipulation of the impeller and after the application of an energy-saving protective coating, Fluiglide.
A vibration test and sound readings are also taken to check for rotor imbalance, bearing wear and cavitation. The user can then make informed decisions about refurbishment and the optimum time for any work to be carried out. The financial investment in testing will be quickly recovered in savings made by reduced energy costs from running a more efficient pump.
Corroserve’s dedicated pump division provides a comprehensive service covering refurbishment, re-manufacture, modification, coating and improved efficiency to many types of pump.