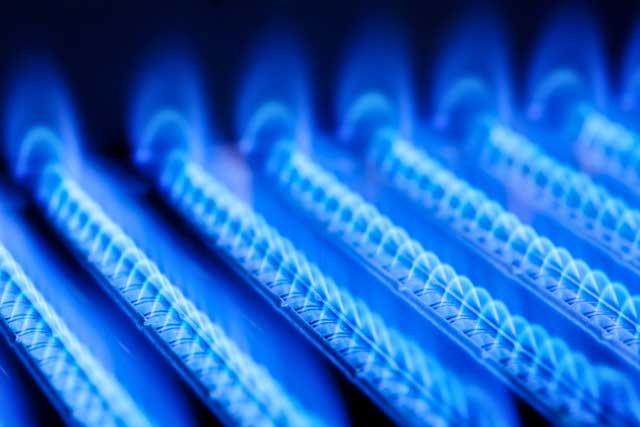
ABSTRACT
Never before has burner technology been as important as it is today. Meeting environmental regulations such as the new EU Medium Combustion Plant Directive and reducing greenhouse gases are challenging.
The demand for cleaner air means that industry needs to take a careful look at its combustion assets and plan for the future.
Any company operating a combustion plant from 1MW thermal input and up to 50MWth will fall under MCPD legislation.
Analysing emissions need not be an arduous task and, in most cases, the use of a modern burner will result in a more efficient system, achieving substantial cost savings and a short payback period.
Introduction
The Government has implemented legislation to force companies to take action on emissions. The MCPD requires anyone with a boiler generating around 1.3 ton/hr of steam or more to monitor and manage their emissions under permit. In summary, any company operating a combustion plant from 1MW thermal input and up to 50MWth will fall under Medium Combustion Plant Directive legislation (including CHP plant and diesel generators).
Typically, more efficient combustion and a reduction in emissions favour energy efficiency, resulting in substantial cost savings with payback in as little as 18 months.
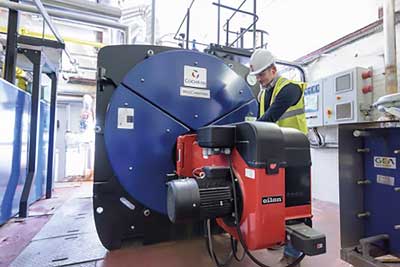
The most important assets in industrial combustion are the burner and boiler combination, and with advances in technology the modern burner has many features that enables it to outperform old equipment. New technology not only supports compliance, it aids efficiency, energy loss reduction and ultimately reduces costs, allowing businesses to be more competitive overall.
The benefits of a modern burner
One of the main advantages of modern burners is the ability to achieve a high turndown ratio of typically 9:1 (more in some cases). Hysteresis losses associated with mechanical drive systems are eliminated. Furthermore, effective mixing of gas and air within the burner head, variable speed drives added to motors, digital combustion controls and oxygen trim systems all work together to complement each other. This combination of technology allows the burner to operate at maximum efficiency at all rates of firing with minimum flue gas emissions.
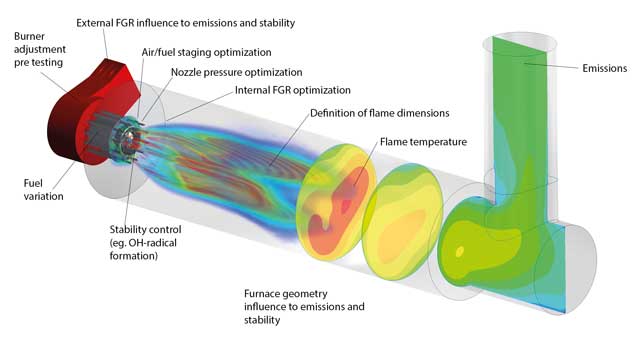
The importance of turndown
Turndown on burners is critical for a variable load. By use of turndown, the energy input can be regulated to match the energy output (or site demand) without the need for stop/start conditions. The most efficient way of running a boiler is to keep the burner firing for as long as possible, if not actually shutting down at all. This reduces the cooling effect due to purging and component wear caused by frequent start-ups, and, more importantly, allows a quick response to sudden changes in load, minimising potential issues with low water level and lockout due to slow response.
It is possible to achieve up to a 10:1 turndown ratio by using an Oilon burner together with an Ecosafe digital controller (a JBC product) coupled to a variable speed drive which modulates burner fan speed, rather than opening and closing a mechanical damper and a fan motor constantly running at full speed. This returns larger savings in power consumption. The Ecosafe digital controller maps the modulation band so that it is possible to ensure that all hysteresis (present in any mechanical linkage system) is eliminated from the drive, from high to low fire, which in turn ensures the burner is firing at peak efficiency throughout the complete range.
Emissions released in combustion
The main pollutants released by a natural gas flame are carbon monoxide and oxides of nitrogen (NOx). Carbon monoxide is colourless, odourless and tasteless and can be toxic to humans and animals in concentrations above 35ppm. It is formed in flue gases due to factors such as lack of oxygen, a cooler furnace flame temperature, too short residence time inside the furnace, exaggerated air/fuel staging and insufficient mixing.
Oxides of nitrogen comprise mainly nitrogen monoxide (NO) and nitrogen dioxide (NO2). NOx is the most strictly regulated emission in burner applications because of the serious damage it can cause to the environment. This includes acid rain, smog and ozone formation (a potent respiratory hazard near ground level).
NOx emissions are derived from three possible sources: nitrogen present in the atmospheric air used for combustion; fuel-bound nitrogen in liquid and solid fuels (but not gaseous fuels); and gaseous fuels which contain nitrogen-based compounds such as ammonia and hydrogen cyanide. In natural gas combustion, only the nitrogen in the combustion air needs to be addressed. In light oil combustion, fuel-bound nitrogen will influence the total emission level, and in heavy oil combustion fuel-bound nitrogen will play a dominant part.
Formation of NOx emissions
NOx is formed in two ways, thermal NO formation and prompt NO formation.
Thermal NO formation: The bounding energy of the N2 molecule is so high that combustion air oxygen (O2) cannot break it in normal combustion conditions.
Formation of NO happens as a result of the reaction path actuated by a single atom O- radical or, when residual O2 is decreased, an OH- radical is operates as an oxidiser.
The amount of generated O- and OH- radicals is exponentially proportional to flame temperature, thus resulting in high temperature dependency for the whole process.
Studies show that NO formation is not significant below 1400°C, but in temperatures above 1600°C it is by many times the dominant formation mechanism.
Prompt NO formation is a result of nitrogen reacting with hydrocarbon radicals to create hydrogen cyanide (HCN) which through further reaction paths oxidises to NO. It is only relevant in the flame reaction zone when the combustion is not yet complete and the required hydrocarbon radicals are available. In conventional burner applications, the prompt NO contribution to the total emission level is no more than 5%. In low NOx-applications, where the flame is relatively cool, the prompt NO contribution becomes more relevant and should be taken into account in the burner combustion performance design.
Reduction of CO and NOx
Complete carbon monoxide burn out could be promoted by altering the conditions that help to form it. However, CO formation conditions are often in conflict with NOx formation conditions (so reducing one will encourage formation of the other). Variables which will promote CO and NOx reduction are choosing a larger boiler or adding more residual oxygen. Unfortunately, burner manufacturers are unable to do this and there are some downsides, such as associated investment and operational costs. Instead, burner manufacturers set out to find an optimal balance between CO and NOx formation.
Optimal balance conditions depend on a variety of circumstances such as fuel and furnace properties, and with correctly designed burner adjustments the flame is able to conform to the changing furnace conditions.
Emission reduction methods – NOx
Air and fuel
Using air and fuel distribution, air and fuel staging or internal flue gas recirculation (using recirculated flue gas as a diluent to reduce flame temperature) will achieve an NOx reduction of approximately 40-60%, depending on the method.
NOx reduction by external flue gas recirculation
For this method, the required components are a combustion manager suitable for FGR applications, a flue gas damper with actuator, a temperature transmitter, a flue gas inlet adaptor, an oxygen sensor and a recirculation pipe provided by the client.
Electronic fuel/air ratio control system
Accurate burner control will result in substantial fuel savings. This method is by far the most efficient and encompasses burner control and security functions, fuel/air ratio control and fan motor variable speed drive control. Its additional functions are boiler cold start protection, boiler temperature limitation, a PID controller for capacity control and O2 control with an O2 module. It will allow results to be seen, as it communicates with external systems and is supplied with a fuel flow meter and combustion efficiency calculator.
O2 control and variable speed drive
Using the electronic fuel/air ratio control system will reduce O2 levels from 4% to 2%, which corresponds to roughly 1% higher efficiency.
To demonstrate this, a 10 ton/hr steam boiler without O2 control or a variable speed drive, running 18 hours a day on natural gas and at a power level of 6ton/hr, would have an efficiency of 87.5% with an O2 level of 4%. Its gas consumption would be 8,071 m3/day or 2,421,300 m3/year.
The equivalent steam boiler with O2 control and a variable speed drive would have an efficiency of 88.5%, with gas consumption of 7,635 m3/day or 2,394,000 m3/year.
Substantial savings would also be made by the variable speed drive on the electricity consumption of the fan motor, reducing it from 89,100 kWh/year to 41,700 kWh/year.
This would equate to a combined saving of £10,200 annually.
Other ways to save energy
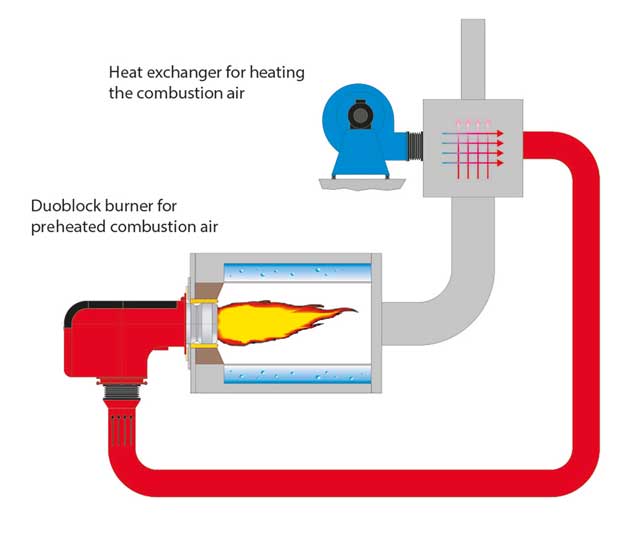
Installing a heat exchanger for heating the combustion air will give 4% higher efficiency when combustion air is preheated to 100°C. Also, liquids and gases which had previously been considered waste have been used as combustible fuels, with many processes having side streams for this purpose, such as for biogases in breweries.
It is also possible to fire two gases simultaneously. For example, biogas plus LPG or natural gas will fire at a simultaneous firing capacity range of 10-100%, and the start-up of a burner can be achieved by either LPG or biogas.
Case study – food manufacturer

A new burner with digital combustion control replaced an old mechanical burner with a mechanical linkage in a food production process. Installation of energy saving equipment was part of the scope. The site required the decommissioning and stripping down of the old structure and the installation of a new Oilon burner with an Ecosafe digital combustion control system, including an O2 trimming system giving up to 7% fuel saving. Following on from this, an economiser was installed to gain a further improvement of around 5.92%.
The reduction in gas cost at the burner, calculated on 80% overall boiler efficiency, 8,000 hours annual operation at maximum continuous rating, and a gas cost of 2.2p/kWh gives a substantial saving of £38,124.
Case study – hygiene product manufacturer
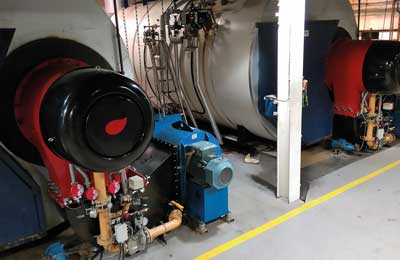
The site required the decommissioning and stripping down of the old, obsolete burner which was installed on the three-pass steam boiler rated at 20,000 kg/hr, and the installation of a new Oilon burner with Ecosafe digital combustion control.
The new Oilon dual-fuel fired burner achieved a turndown of up to 8:1 on gas, with operating NOx levels below 100mg/m3, compared with the old system which only had a turndown of 3.5:1 on gas, and operated at high O2 levels towards the bottom of its modulation range.
By reducing excess oxygen levels from 8% to 3.5% at low fire where the burner operates for the majority of time, fuel savings of 2% were achieved.
The Medium Combustion Plant Directive
The proposal was originally published by the European Commission in December 2013 and forms part of the new Clean Air Package, introduced to help member states reduce their emissions and meet revised ceilings being negotiated under the NEC Directive. It will plug the gaps between plants covered by the European Ecodesign Directive 2009 and the Large Combustion Plant Directive, and sets emission limit values for NOx, sulphur dioxide and dust.
The requirements also include the measuring and reporting of carbon monoxide in low air quality zones. Specifications for any new plants will need to meet the criteria.
It is estimated that over 15,000 plants in the UK will be affected and will be required to comply with emissions limit values. It is anticipated that 75% of those will be between 1-5MW and regulations will affect boilers (80%), engines and gas turbines.
From 20 December 2018, all new plants must be registered and have permits from the Environment Agency, and test emissions to show compliance with the ELVs. Existing plants above 5MW have until January 2024 to register, but must comply with ELVs by January 2025.
Existing plants below 5MW must be registered and tested for emissions by January 2029 and have until January 2030 to comply. It is worth noting that if burners are replaced and potentially exceed 50% of the original asset value of a package boiler, the MCPD may define it as a new asset under the regulations.
JBC has invested time and resources in order to advise its customers on how and if MCPD affects them and what their options are. For help, advice and updated information on MCPD contact info@jbcmail.co.uk, putting “MCPD Advice” as the subject header, or contact 0113 220 3830 and ask for Matthew Schofield/Pete Nicholls.
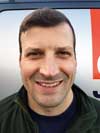
Pete Nicholls
Technical manager,
JBC Industrial Services