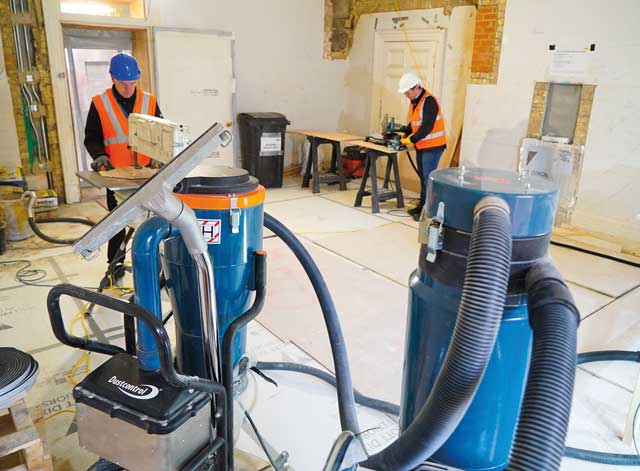
New techniques such as segregation have made controlling and preventing the spread of dust more effective, with benefits for safety and for product quality, says Dustcontrol UK managing director James Miller.
One of the biggest challenges facing the engineering industry is preventing dust migration, especially in large-scale premises where excess dust is prevalent.
Using heavy-duty machinery in such environments can create and encourage the spread of hazardous dust, which presents significant health and safety as well as product quality issues.
Airborne dusts are of particular concern in manufacturing, not only because they can greatly increase the risk of product pollution in the food, aeronautical, automotive and composite engineering industries (to name but a few), but also because they have the potential to affect the health of people working in those industries.
Being exposed to and breathing in high levels of fine dust, often invisible to the naked eye, can lead to widespread occupational lung diseases such as pneumoconiosis, while also significantly increasing the chance of developing other dust-related diseases, such as cancer, asthma, allergic alveolitis and irritation, as well as a whole range of non-respiratory illnesses. Overexposure to hazardous dust for a prolonged period can even cause permanent disabilities and death.
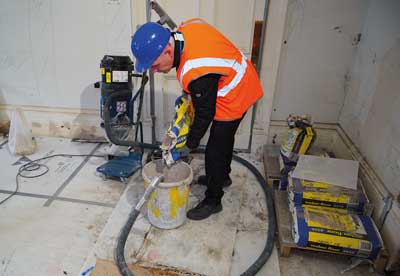
It is therefore essential that efficient measures are adopted for the protection of the workforce and the quality of products, while adhering to the relevant health and safety regulations.
All companies are required to adhere to the Control of Substances Hazardous to Health (COSHH) Regulations 2002, which set out workplace exposure limits (WELs). These limits are legally binding, and businesses must make sure they abide by the limits contained in the Act.
Deeper understanding
As a deeper understanding of the harmful properties of dust is gained, businesses are taking measures to control and confine areas in the workplace where excessive dust is created, and using at-source extraction techniques to minimise the release of airborne dust in the first place, with centralised vacuum systems for cleaning up.
The sectioning-off of a specific room involving dust-producing processes allows other areas of the site to work unhindered. The air in the room itself can then be cleaned more easily because of its smaller volume.
Containing the release of airborne dust in a designated area prevents its spread throughout the workplace, creating the safest possible working environment.
It is crucial, though, to manage the sectioned-off areas to ensure the complete safety of those using them, where high concentrations of dust can be created within small spaces because the dust can no longer dissipate. These areas must be managed with a combination of high-quality dust extraction solutions.
Through the innovation of attaching power tools to extraction units via hoses or nozzles, businesses can remove dust as an issue altogether by capturing it comprehensively at the point of its production. The loading on secondary air cleaners is reduced, making cleaning less onerous, and potentially reducing the prevalence of Atex-rated zones.
Background air cleaning equipment with HEPA-13 filters can then be used as a complement rather than a first line of defence. Within the sectioned-off areas simple techniques of using negative pressure (so that air can flow in but not out) can further prevent migration to other areas, helping to maintain a clean, healthy working environment.
Overall, introducing smaller, more efficiently-sized areas which are used solely for dust-producing practices, and introducing efficient dust extraction techniques, can effectively control and contain the spread of dust, while creating a safer working environment.
Dustcontrol UK has a wealth of experience in helping businesses control and prevent the spread of dust in the manufacturing, engineering, food processing, construction and demolition industries, through providing dust extraction solutions and centralised vacuum systems to fit client requirements.