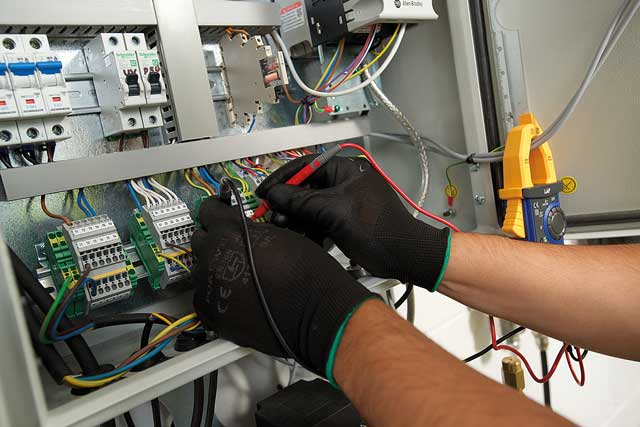
Companies operating processes where airborne moisture content is critical are discovering the value of Humidity Solutions’ innovative remote monitoring service. By David Fowler.
Remote monitoring for humidification and dehumidification equipment is being offered by Humidity Solutions as part of its planned maintenance contracts.
The independent humidification specialist has been offering the option for just over a year, and says the service is proving valuable for remote sites and for production processes where environmental conditions are critical.
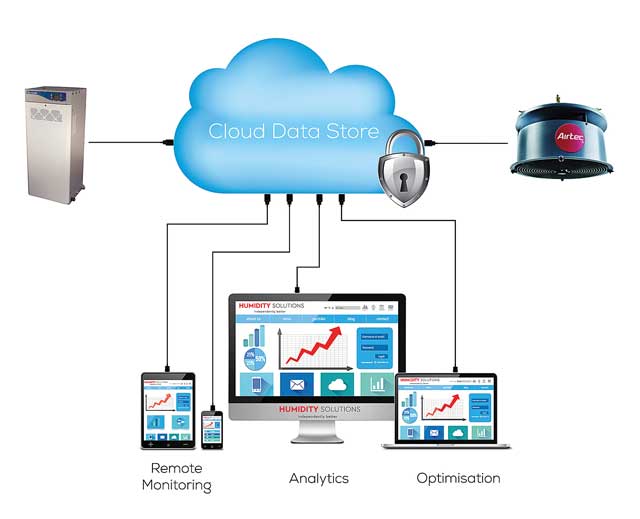
After sales director Rob Luddington says: “A key driver is that remote monitoring allows you to schedule services when the equipment needs it. Whereas in the past we would service a unit at, say, six monthly intervals under a maintenance plan, with remote monitoring we can adjust the timing based on the hours the unit has actually run.” So if a unit runs for more hours in the winter than the summer, timing of services can be adjusted accordingly.
He adds that another driver is the data that is produced. “We’re finding customers want data,” he says. “If a problem arises with their process they can refer back and see what the humidifier was doing at the time in question.” Pharmaceutical processes, for example, may need to be able to validate that production took place within a specified humidity range.
“I expected it to be about optimising service schedules, but the data side is more valued than we expected,” says Mr Luddington.
An example application is a malt store – a grain silo in Elgin, Moray. The company’s engineering manager is responsible for a number of sites of which this is the only one in Scotland. A 100% relative humidity fog is maintained at the base of the silo. If the process goes out of specification a whole batch of grain worth hundreds of thousands of pounds could be lost. In the past, if any problem arose the engineer would have to go to Scotland to rectify it. With remote monitoring the system “can give complete visibility of what’s going on,” says Mr Luddington.
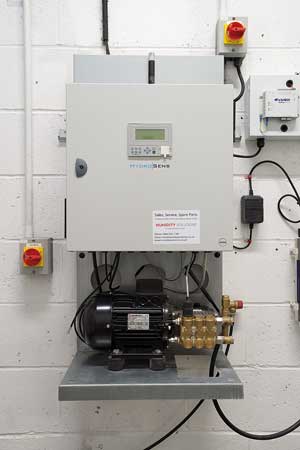
Monitoring has been made possible because the cost of technology has dropped significantly, he says. A router is attached to the unit’s controller which connects to the internet. Staff at Humidity Solutions’ 24-hour service desk can log on at any time to interrogate the unit. If a fault arises an alert appears on screen immediately. Customers also have the option of being notified by email automatically, and data is also stored in the cloud.
Mr Luddington says that often there is only a “soft” fault – the unit may have automatically shut down because of the water supply being interrupted, for example. He says: “Often we can reset it remotely, and the machine will then continue to operate normally.” By the time the customer receives an email alert and logs in, the problem may already have been solved.
If a site visit is needed, it is usually possible to diagnose what is wrong and make sure the engineer takes the right part, avoiding having to make multiple visits.
Parameters including supply air temperature, relative humidity, return air temperature and unit status can be viewed and logged. The communication is made via Modbus protocol and a graphic displays the data.
Other applications, says service engineer Eddie Capraro, include a medical supplies firm making indicator strips for urine analysis, where it is critical to production to maintain humidity between 10 and 15%. Monitoring was also installed for a printing firm, where the humidity is controlled to optimise ink setting and to prevent the paper curling through being too dry. Humidity has to be kept within tolerance or the presses stop automatically. “With remote monitoring we can pick up on anything that’s wrong and warn the customer that production is in danger of going out of specification,” Mr Capraro says.