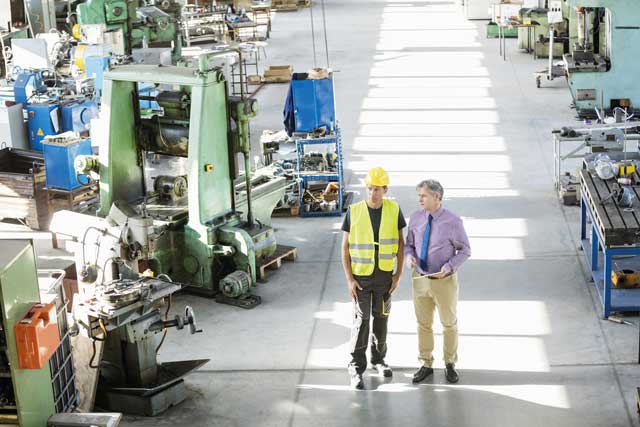
Many organisations may believe they are implementing this philosophy but in reality have only embraced a watered-down imitation, says Roy Davis, director of Manufacturing Productivity Improvements
Since its introduction to the western world almost 30 years ago, Total Productive Maintenance (TPM) has become a commonly used phrase or acronym among maintenance professionals.
Over that time the meaning of TPM, as conceived by its founding fathers such as Seiichi Nakajima, has often been misinterpreted and diluted so that many of the maintenance community are guilty of misusing the term.
When I first encountered TPM in the late 1980s and subsequently visited Japan to witness TPM in action, I was somewhat overwhelmed by the difference between TPM and traditional western approaches, not just to maintenance but to manufacturing operations in general.
Here was a philosophy based on the development and engagement of people from the factory floor to senior management. All aspects of the acquisition, operation and maintenance of machinery and equipment were incorporated in an all-embracing approach to the achievement and sustainment of world-class operational and maintenance performance.
The three main components that collectively make up TPM are:
- Total approach: an all-embracing philosophy which deals with all aspects of the facilities employed in all areas of an operating company and the people who operate, set up and maintain them
- Productive action: A highly active approach to the condition and operation of facilities, aimed at constantly improving productivity and overall business performance
- Maintenance: A very practical methodology for maintaining and improving the effectiveness of facilities and the overall integrity of production operations (1).
In Seiichi Nakajima’s book Introduction to TPM (2), one of the first books translated into English on the subject, he describes the “12 steps of TPM development” which included five main subject areas. These were later developed into the five initial pillars of TPM as illustrated above.
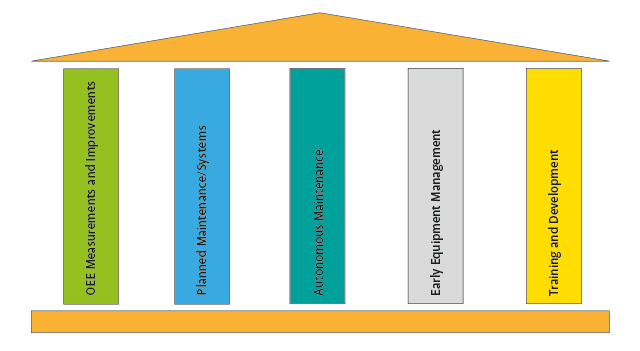
These were further developed and detailed in his subsequent book TPM Development Program (3) and have been used by many organisations as the main pillars or building blocks of their TPM programme. Over the years many variations on these five original pillars have been developed by organisations and consultants to suit their specific requirements, but the validity and logical approach of using the five pillars is still sound.
For each pillar there is a particular methodology for its development and implementation and there are number of tools, techniques and steps that have been employed by organisations to achieve the objectives of each pillar. The approach showed how they were all integrated and necessary to establish a total system for productive operation and maintenance.
I find it disappointing that almost 30 years on this message has not been received, or perhaps it has been firmly placed in the “too difficult” pile by many organisations. What is also frustrating is that many companies purport to be implementing TPM when clearly they are not, or at least are only trying to deploy a particular pillar or technique, often a “watered down” version of the original.
Examples of this include:
- Sites that refer to their “TPM” which is no more than operators being given a list of very basic machinery checks to carry out. Often these have not been supported by adequate training, have very little buy-in from production and become just a tick-box exercise which gradually falls in to disrepute
- Sites that employ “TPM Co-ordinators”’ who have little or no understanding of the principles or practices of TPM and whose primary purpose is to distribute planned maintenance work orders to maintenance or production personnel, chase up their completion and then enter them into the CMMS when completed.
- Sites that have a “TPM Programme” which is basically a maintenance improvement project aimed at developing planned maintenance documents with, on some occasions, production operator involvement.
What these attempts appear to totally miss is that TPM is a bottom-up initiative which relies on the motivation and participation of all operational personnel. There are also business implications attached to the implementation of TPM which need to be understood.
- TPM is aimed at effective operations, not just efficient manufacturing. The business has to come to terms with the characteristics of effective operations and realise that machinery does lie idle at times, operators can be involved in activities other than operating machinery, and maintenance activities are essential.
- At the very heart of TPM lies the encouragement and enhancement of factory floor personnel. The traditional relationships between shop floor and management have to change from distrust and confrontation to mutual understanding, trust and team working. This will not happen overnight, but will happen for TPM and as a result of TPM.
- TPM is oriented around factory floor machinery and equipment but it will have a profound affect on the whole company.
In summary, businesses are very much missing out on the benefits that a proper application of TPM could bring and are unfortunately, as a result of lack of understanding or lack of will, effectively pretending to apply what is an excellent world class approach.
References:
[1] Productivity improvements through TPM –
Roy Davis. Prentice Hall. 1995.
ISBN 0-13-133034-9
[2] An introduction to Total Productive Maintenance –
Seiichi Nakajima. Productivity Press, 1988.
ISBN 0-915299-23-2
[3] TPM development program –
Seiichi Nakajima Productivity Press, 1989
ISBN 0-915299-37-2