As the flexible factory grows in importance, John Guest business development manager Roger Goodwin looks at how modular compressed air systems can play their part in their future.
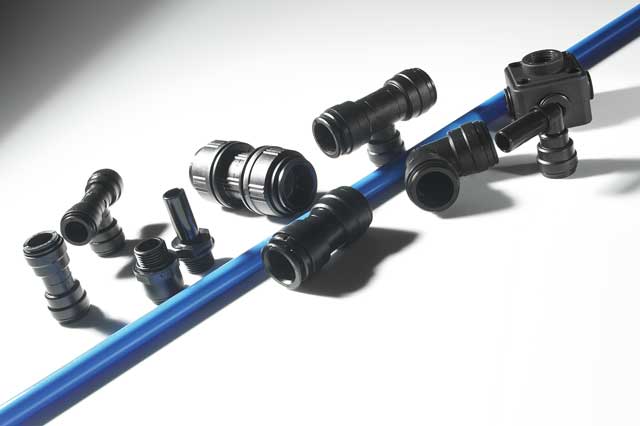
As nations such as India and China continue to develop as manufacturing powerhouses, UK factories must become ever smarter to compete. The UK does not have the labour conditions and investment needed to support behemoth-sized factories to house large-scale mass production lines. Instead, its focus has been directed towards higher value engineering that can be undertaken in small to medium plants. UK manufacturing is moving towards small-run, high-value goods. Factories must be able to accommodate this – and flexibility is key.
Flexible factories
Flexible factories are designed to be reconfigured – with minimum downtime. This makes them more responsive to customers, and greatly reduces supply-chain complexity.
For manufacturers, this allows for a more diversified business, without the costs of retooling or setting up separate production lines.
A good example of this is in the automotive industry. Manufacturers are turning towards increased customisation to attract discerning customers, but this can play havoc with production lead times. A leading car review website found that the average factory order time for cars built to a customer’s specification was 13 weeks.
To avoid losing orders, flexible factories should be able to quickly change assets and layout to accommodate different variations.
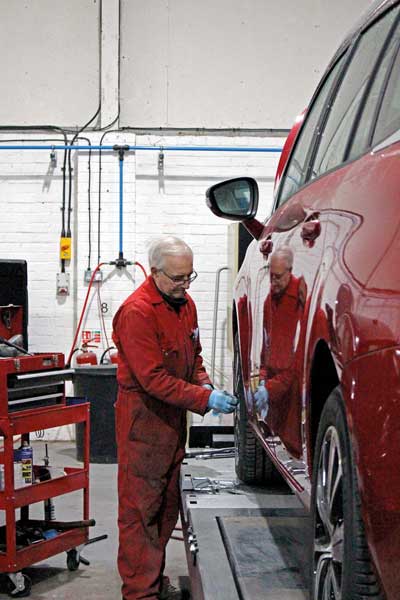
Galvanised systems
One crucial asset for production is compressed air. It is vital for the operation of power tools, wrenches, grippers, suction pads and much more.
Traditionally, compressed air systems used straight lengths of galvanised steel pipes to convey air from the compressor to power factory-wide equipment.
In a flexible factory, compressed air systems must be reconfigured just as quickly as everything else, with minimum downtime.
Achieving this with galvanised pipe systems is impossible. Not only do they require time-consuming cutting, threading and demounting, they are also heavy and cumbersome to work with. Pipes, customarily supplied in 6m lengths, need to be cut to size.
In addition, galvanised pipes are more prone to leaks – a significant source of wasted energy, and cost. In some cases, leaks can waste up to 30% of a compressor’s output. Common reasons for leaks include corrosion, which weakens the seal between joints, or poor installation when pipes are threaded.
Chop and change
To address these concerns, modular push-fit fittings and pipes lead the charge, such as those from the John Guest Air and Pneumatics range. The lightweight pipes are made from rigid nylon or aluminium, providing the strength of steel, but without the problems of corrosion, unwieldiness and leakage. They are also easier to cut to length from 3m stock lengths.
Because of their composition, aluminium and nylon pipes are much cleaner too. The highly engineered fittings and pipes do not rust, minimising the risk of long-term damage.
The modular push-fit system provides installers with a more predictable connection, and enables their skills to be focused on the whole system and its efficiency. The push-fit technology employed means a leakproof seal can be made in minutes.
The true benefit, though, is in the time it takes to reconfigure pipework. Pipes can be demounted from the fittings without tools, and then reused for the next factory layout.
Albert Einstein said: “We cannot solve our problems with the same thinking we used when we created them.”
Compressed air remains as vital to our factories as when it was first used. However, just as the factory and market dynamics have moved on greatly since, so the technology has improved – so manufacturers need to be more flexible in their thinking.
For more about John Guest’s compressed air range, visit: Johnguest.com