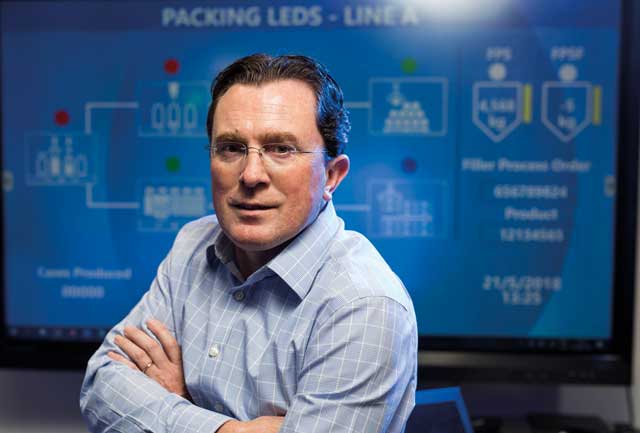
Manufacturing frequently relies on human proficiency and is directed more by senses than by sensors. Smart manufacturing puts precision in the system, removing the variations of manual processes, says Brendan Sheppard of consultant SmartFactory.
A revolution in manufacturing is firmly under way and smart manufacturing is at the heart of the digital transformation that companies are currently undergoing. This revolution is driven by the ability to capture, analyse and act on data, in real time. For most traditional manufacturing companies, data is a by-product of production, but most of this data is discarded without attempting to derive insights from it. However, the convergence of operational technology with IT is allowing organisations to tap into a new level of system integration and allows real-time coordination between people, assets, and things. This is the factory of the future: the Smart Factory.
The technological foundations for the industrial internet of things (IIoT) are not new. Although there has been continuous innovation in manufacturing over the last 20 years, traditional automation systems were usually built on proprietary protocols and lacked the connectivity to link equipment with globally connected IT systems.
The emergence of robust standards such as MQTT and OPC UA permits the interoperability, portability and scalability required for the widespread adoption of IIoT platforms, which will transform manufacturing over the next decade. “Plug and play” integration will continue to reduce the investment required and will dramatically accelerate implementation.
The result is a lean operation that was previously unimaginable, where downtime is predicted and prevented, waste and defects are minimised and surplus production is eliminated. Machines can take corrective actions, autonomously, as operating conditions or raw materials change. The potential benefits of implementing and operating IIOT systems are enormous; however, significant challenges remain.
The barriers to smart manufacturing
Complexity: Implementing an IIoT solution doesn’t have to be complicated. Many manufacturers are very good at innovating with new products, but their production processes haven’t changed in years. When it comes to the IIoT, lots of companies are doing nothing, because doing nothing is better than spending a lot of money doing something and getting it wrong.
The language that has been used in association with IIoT, such as digital twins, cyber-physical systems and augmented reality, has added to the confusion. At its heart, smart manufacturing is about getting people away from paper and spreadsheets and giving them real-time actionable intelligence to optimise operational performance.
Security: The security concerns associated with IIoT platforms remain one of the greatest barriers to widespread adoption. The cultural and priority differences between IT and OT functions continue to produce fragmented solutions for IIoT projects. OT personnel seek product-specific security solutions while IT departments seek enterprise-wide control.
According to a Gartner IoT security report, “By 2020, over 25% of identified attacks in enterprises will involve IIoT, though IIoT will account for less than 10% of IT security budgets”. Companies need to implement a “security by design” policy and to develop specific security practices for the deployment of IIoT devices, focusing on network design and segmentation capabilities, data protection, authentication and security analytics.
People and mindset: The innovation in technology is necessary but not sufficient to disrupt the manufacturing sector. It is critical to look beyond technology at the people and processes in your business. For companies to get the maximum benefit from IIoT projects, an organisation’s management of people and processes must be transformed to create value from abundant data and interconnected systems and assets.
Understanding the value added: The two primary drivers for IIoT solutions are cost reductions and capability improvements. There are plenty of real-life use cases to demonstrate how this technology is being used to make the manufacturing value chain more effective and efficient and to generate business transformations. Companies need to enlist the help of an IIoT expert to create a roadmap for how these digital transformations can be achieved.
Legacy equipment: An additional barrier to IIoT adoption in manufacturing is the nature of capital equipment, which is often expected to perform for decades, with minimal upgrades to the original hardware or software. As IT and OT systems converge, OT can become the limiting factor for productivity and capability improvements. In a globally competitive manufacturing environment, manufacturers must replace or augment their legacy assets with advanced manufacturing technologies to maintain competitiveness as their equipment ages. IIoT analytics can provide the basis for making those investments.
The process of becoming a Smart Factory is a journey and the potential benefits are enormous. Reliance on human mastery limits continuous improvement, knowledge transfer and data-driven decision making. Companies that delay may find themselves outclassed, out-competed and ultimately out of business.
Brendan Sheppard is a mechanical engineer who has worked in the manufacturing of fast moving consumer goods for more than 20 years. He is chief executive of SmartFactory, based in the Nexus Innovation Centre in the University of Limerick, Ireland.
SmartFactory adds intelligence into the manufacturing process to drive continuous improvement, knowledge transfer and data-based decision making, helping companies move away from paper and spreadsheets to adopt wireless sensors and cutting-edge IIoT technology to capture, analyse and visualise KPIs in real time. It works with partners including Turck-Banner, Siemens and Linespex.
www.smartfactory.ie | www.turckbanner.co.uk
www.siemens.ie | www.linespex.com