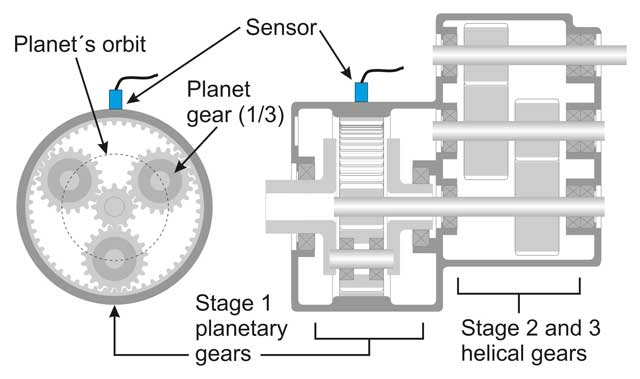
The planet gears in the geartrain of a wind turbine are critical components – but because of their slow rotational speeds, it is not simple to detect the vibration that normally signals a fault. Mike Hastings, senior application engineer of Denmark-based Brüel & Kjær Vibro, describes how a more sophisticated technique has evolved.
Nearly all wind turbines are delivered with some sort of condition monitoring system for the purpose of increasing availability and reducing the life cycle cost of the turbine. There is, however, a significant difference in the value these systems provide to the operation and maintenance of assets, such as how raw data is processed, stored and accessed. Just as importantly, however, there is also a difference in:
- How early and reliably faults are detected
- How reliably faults are diagnosed and observed
- How useful is the actionable information that is given
This is an especially important consideration when monitoring low-speed drivetrain components such as the blade bearings, main bearing and – the topic of this article – the planetary geartrains. Successful performance of a condition monitoring system in this case is based heavily on the system supplier’s expertise. since the techniques and algorithms are refined from experience.
Challenges
Converting the slow rotational energy of the blades (10-16 rpm) to the generator speed (1320-1680 rpm) is accomplished by a three or more stage gearbox. The planet gears are the most difficult to monitor in the gearbox. If not properly monitored, a failed planet gear could result in catastrophic failure of the entire gearbox.
The vibration energy contribution of each planet gear and their associated bearings during operation is small in relation to the other components. Moreover, the length of the vibration signal transmission path between the orbiting plant gear and the fixed sensor varies considerably during its path around the ring gear. This results in a signal that makes it difficult to extract fault information.
Solution
A monitoring technique has been developed for detecting and diagnosing planetary gear/bearing faults, based on the experience of monitoring thousands of wind turbines, which combines automated processes with manual diagnostic analysis. It boils down to a four point strategy:
Detection – The vibration data is processed and filtered into multiple descriptors, not a single descriptor. Together they focus on different aspects of detecting and tracking machine component fault symptoms, which are extracted from the signal. These include narrow and broad band measurements, tooth passing frequency measurements, crest factor (peak value of the signal divided by its root mean square value), and others. In addition to this, an intelligent alarm management strategy is employed that automatically analyses all the descriptors and issues an alarm only if all weighted alarm criteria are fulfilled for the different descriptors.
Classification – The diagnostic specialist evaluates the alarm and determines the type of fault, its severity and expected lead-time to service. The severity of the detected fault also determines how closely the trend will be followed (for example, using an automatic trend alarm). The customer is informed at this stage.
Tracking – A different set of descriptors are used for automatically tracking the development of the fault. The alarm management system dynamically analyses the rate of change of the fault as it trends in comparison with what is expected. An alarm is issued if there is a deviation.
Action call – A recommendation for a date for stopping the turbine for replacement is made based on using as much of the remaining life of the planet gear and bearings as possible with minimal risk for failure. There are many factors that go into this assessment, such as the initial detection evaluation, how the fault developed, whether there are indications of component interaction because of the fault, whether the fault is localised or distributed, and so on.
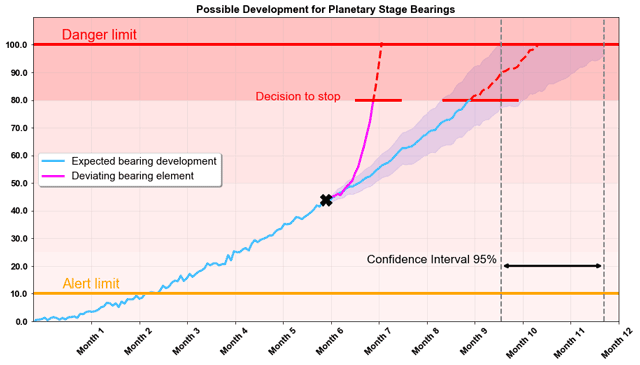
Conclusion
The descriptors and algorithms used in the automatic and manual diagnostic work are based on statistical analysis of thousands of wind turbines. An important part of the success of this monitoring technique, therefore, is to continuously refine the monitoring solution as more experience and technology is gained. This requires close cooperation with the wind park maintenance staff. The result is that, over a period of several years, hundreds of planet gear or bearing faults have been successfully detected and catastrophic events avoided by using this strategy.