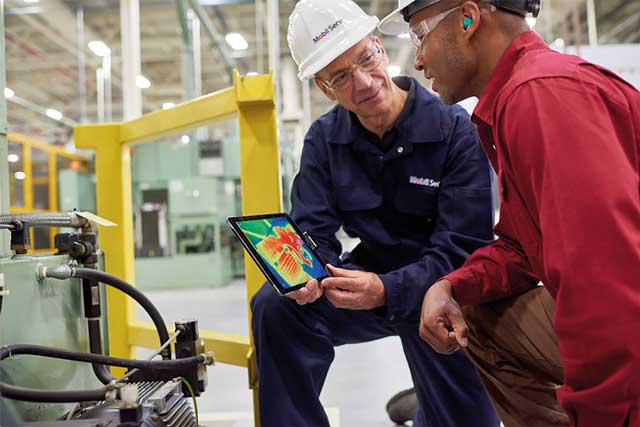
Lubricant expenditure represents a fraction of the cost of running industrial machinery but, if done correctly, a small investment can offer a valuable return. Exxon Mobil EAME offer advisor Inken Reuser explains
Lubricants used in industrial machinery and processing equipment are often exposed to high temperatures and pressures for prolonged periods. Depending on the application, there are also risks of contamination from production debris. These factors can adversely affect lubricant performance, which risks unscheduled maintenance and avoidable downtime.
It is therefore important to select the most appropriate lubricants for specific industrial applications.
However, the selection process is far from straightforward – it is essential not only to consider the quality and performance of an oil or grease, but also to take into consideration the requirements and challenges of the specific application.
So what needs to be taken into account? A good first step is to understand the differences between synthetic and mineral lubricants.
Synthetic vs mineral lubricants
Synthetic and mineral lubricants are both made from fractions of crude oil, but synthetic products are further refined using chemical processes, which provides them with highly valuable characteristics. This means they can provide a range of performance benefits including:
- Longer oil life
- Wider operating temperature range
- Resistance to deposit formation
- Better wear protection
- Greater resistance to oxidation (thickening)
Taken together, these features can help extend equipment life. It is therefore worthwhile considering a switch to synthetic lubricants, depending on the application.
Viscosity index
Another key consideration when selecting a lubricant is its viscosity. Choosing the wrong oil grade can increase equipment wear and energy consumption, while reducing lubricant life. Put simply, when temperatures rise, viscosity falls, and when temperatures drop, viscosity increases. The degree to which this happens to an oil is called its viscosity index (VI).
A low VI can result in an oil having insufficient resistance to temperature changes, which can have a detrimental effect on its performance and can result in costly and avoidable wear. Synthetic lubricants with a high VI can help protect industrial machinery and processing equipment across a wide range of operating conditions.
Most applications have specific viscosity requirements, so plant managers should always check the original equipment manufacturer’s recommendations. However, it is also advisable to talk to your oil supplier’s field engineers in order to make sure you are using the best performance lubricants, including a possible switch to synthetic grades.
Proof of performance
Hydraulic oils are a common lubricant in many industrial processes, and significant benefits and savings are potentially available if an inferior grade is currently being used. For example, Kotronis Plastics, a Greek manufacturer of polypropylene containers, cut energy consumption, safely extended oil drain intervals and reduced cycle times by switching its injection moulding machines to a superior hydraulic oil.
The manufacturer had wanted to cut costs and reduce its environmental impact, and approached ExxonMobil’s local distributor, Novitron, for suggestions on how this might be achieved. The oil supplier suggested switching its 40 Sumitomo Demag El-Exis SP 250 injection moulding machines to Mobil DTE 10 Excel 68, a high performance hydraulic oil. Historical data for Sumitomo Demag machines suggested this could provide both productivity and environmental gains.
Mobil DTE 10 Excel 68 was initially trialled on a single machine. The results showed improved cycle times, a 2.23% cut in energy consumption and an extended drain interval of more than 20,000 operating hours. The total available cost saving, when extrapolated to all 40 machines, was estimated at €17,000 (£15,000) annually.
Machinery health check
Even when using the most appropriate lubricants it’s still important to analyse their performance in order to help maintain processing equipment at optimal operation. For this purpose, ExxonMobil has launched Mobil Serv Lubricant Analysis (MSLA), a new used oil analysis service. By assessing the health of a lubricant it is possible to detect developing issues before they become a problem and maintain peak operational efficiency and productivity.
Small change, big difference
Overall, lubricant expenditure represents a fraction of the cost of running industrial machinery, but if done correctly, the investment offers a valuable return. Not only can it improve energy efficiency by maintaining the desired viscosity, it can also help protect equipment, reducing maintenance costs while also extending oil drain intervals. In turn, that reduces waste lubricant disposal, helping improve a company’s overall environmental credentials.
Given the size of the overall benefits, it is important to choose a lubricants partner that not only provides the most suitable products but one that also backs this up with in-depth technical knowledge and support.
https://www.mobil.com/industrial
Technical help desk: thd@exxonmobil.com