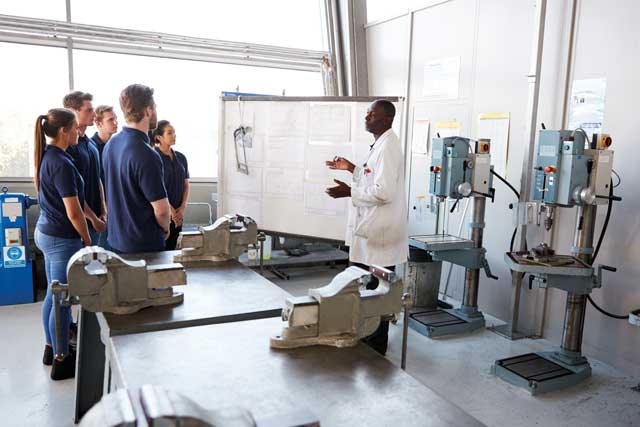
Many companies continue to report difficulties recruiting engineers. But, says DAK Consulting director Dennis McCarthy, many organisations need to ask themselves whether they’re making the best use of the skills they already have.
In a survey by the IET [1], nearly half of engineering firms said that hard-to-fill vacancies had meant delays in developing new products or services, while 45% said they experienced increases in operating costs.
It is widely accepted that the economy would benefit from an increased supply of engineers entering the labour market. “Engineers are the people who can create practical solutions to our 21st century challenges of sustainability, housing and an ageing population. And we need more of them,” said Sir James Dyson. But is this the full story?
A recent survey by McKinsey found that around 7 out of 10 companies haven’t formally defined their science, technology, engineering and mathematics skill gaps and that only around 1 in 10 organisations have implemented a plan to deal with them.
So what questions should managers be asking to become part of this elite 1 in 10 organisations?
1. What percentage of time spent by current skilled staff is fully productive, and how good are your processes to systematically improve on that?
In one company we found that less than 50% of time spent by engineers was fully productive. In our experience, this is the norm rather than the exception. It is also common to find that 25% or more of routine maintenance tasks are unnecessary.
2. How well defined is the ideal engineering team skill profile, where are the gaps and how good is your company at developing the skills it needs?
That includes transferring lessons learned and helping engineers to acquire new capabilities. Organisations that do this well can reduce time to achieve local area competency levels by as much as 75%.
3. Are you keeping pace with technology?
The pace of technological progress is so rapid that traditional academic education cannot keep pace with developments in memory, sensors and artificial intelligence. This is an area where in-house learning using practical projects is essential. Organisations that do this well focus on “pockets of automation” using multi-disciplined teams, including front line engineers.
In addition, studies show that when developing skills, attitude trumps IQ. So add to the above questions:
4. How well does your organisation encourage a positive attitude to learning in the workplace?
Skilled personnel are not usually tempted to change jobs for financial reasons alone. They tend to be motivated by opportunities for self-development and job satisfaction. Surveys show that training and development are key job satisfaction factors for nearly 70% of STEM workers. Food for thought if you want to keep the engineers you have!
Total Productive Manufacturing
It may come as a surprise to some that all four of the above areas are within the scope of Total Productive Manufacturing principles and techniques.
Often incorrectly characterised as simply operator maintenance, the TPM road map systematically removes the causes of reactive management to release engineer and management time to focus on higher value-added activities. Within the TPM process, education and training is used to ratchet up equipment effectiveness, by refining working methods and standards to prevent breakdowns and systematically remove the causes of common problems. Through this process, cross-functional front-line teams become engaged with learning through their involvement with task simplification.
Such cross-functional team-based projects not only develop engineering skills, but also provide a vehicle to develop innovation, project management and leadership competence. The investment in time results in a bottom line return worth between six to eight times the cost. Perhaps the biggest benefit is the impact on the way skills are applied and future capabilities are developed.
There is no doubt that without skilled workers, it is hard for a business to grow, especially in the manufacturing and technology sectors. These are challenges that Total Productive Manufacturing and aligned tools like fast-track RCM are designed to overcome.
Reference
[1] Skills and Demand in Industry 2016 survey, the IET
Dennis McCarthy, DAK Consulting 01491 845504
www.dakconsulting.co.uk