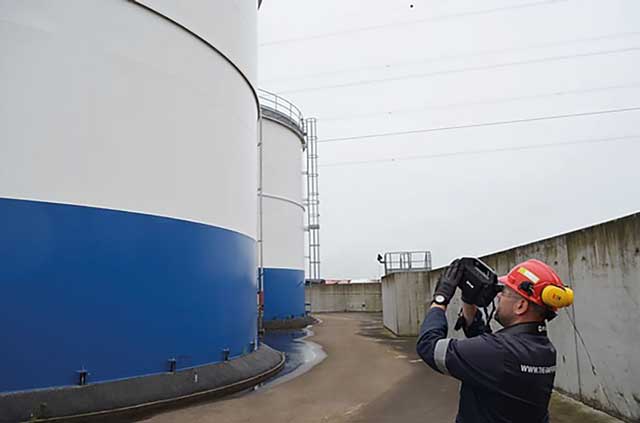
Specialist IR cameras are proving a fast and effective way to monitor tanks and pipework in process plants
Corrosion and exposure to the elements considerably increase the likelihood of gas leaks in chemical liquid tanks and their associated pipework and plant. This presents a big problem because non-compliance with increasingly strict safety and environmental regulations can lead to huge fines and loss of production.
Thermal imaging is already well established as a method for detecting faults and monitoring the health of electromechanical systems, but with specialist infra-red cameras it is also an effective way to spot the source of gas leaks. The technology, known as optical gas imaging, allows thousands of connections and metres of pipework to be monitored in one scan. Any escaping gas is visualised as plumes of smoke on the camera’s LCD, so its source can be easily pinpointed and remedial action taken.
OGI cameras use spectral wavelength filtering and Stirling cooler cold-filtering technology to visualise the infrared absorption of gases such as methane, sulphur hexafluoride, carbon dioxide and refrigerants. The technique allows maintenance engineers to institute safer and more efficient leak detection and repair programmes, not only saving money but more importantly improving the safety of personnel and assets.
Unlike traditional thermal imaging, OGI is qualitative, not quantitative. Because of variation in the environment background energy, an OGI camera alone cannot determine the specific type or amount of gas escaping. And it should also be noted that no single camera will detect all gases, so it’s important to understand the application and its need. For example, a VOC/hydrocarbon OGI camera will not detect sulphur hexafluoride and a carbon monoxide camera will not detect refrigerants.
European inspection company The Sniffers, headquartered in Belgium, is a keen advocate of OGI. It is employed to monitor installations, particularly in the oil and gas, petrochemical and chemical industries, and provide advice on how to reduce emission and energy losses and maintain the integrity of the pipeline network. Its engineers’ prime task is to seek out unwanted emissions. By using OGI they are able to inspect assets up to nine times as fast as with traditional toxic vapour analysers.
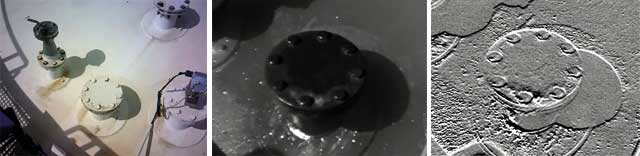
“We’ve been performing leak detection projects for fugitive emissions around the world for more than 25 years, and OGI is now an essential tool for us to get the job done quickly and safely,” explains project leader Bart Segers. “With a TVA probe, you have to approach your target really closely, which is not always possible or even safe. With an OGI camera you can monitor large areas from a safe distance and get an overview of the entire target without having to build scaffolding.”
Another major benefit of OGI is speed. Segers continues: “At a typical site we have to monitor about 500 sources. With a TVA probe, this would take a whole day, but with our cameras (FLIR GFx320 models) I can manage that in just one and a half hours.”
Optical gas imaging is the ideal solution for monitoring a variety of liquids and plant equipment. The camera models the Sniffers use enable its inspectors to visualise around 400 different gases including methanol, ethanol and benzene. As the cameras are intrinsically safe they often allow the company to respond to an emergency without the need for hot work permits. This is another big time-saver and means production can be resumed within a shorter time.
Segers concludes: “We can take digital pictures and an HSM movie with the camera, which comes in handy when you report to the customer. They provide immediate evidence and demonstrate the severity of the leak so appropriate action can be taken.”