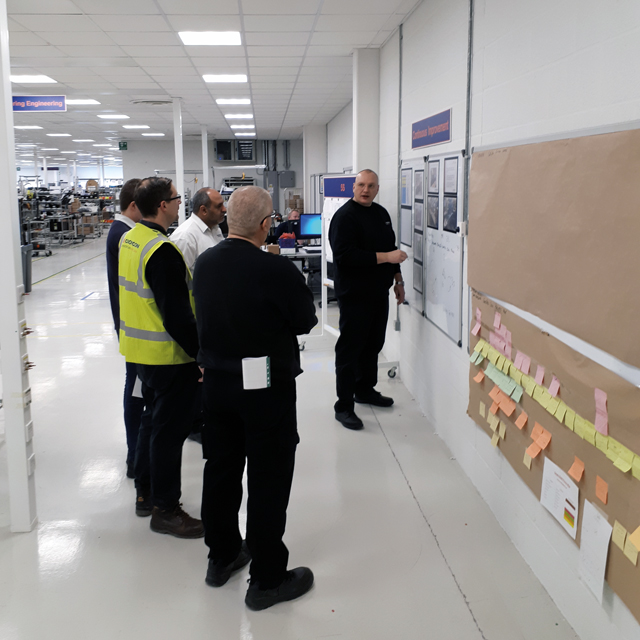
Lean training can show companies how to boost efficiency and improve productivity, says Neil Fedden, owner and managing consultant of lean business specialist Fedden USP
The manufacturing sector is ideally suited to benefit from lean training, which has become increasingly popular as companies strive to keep costs down while increasing productivity. It helps to achieve sustainable business benefits by improving process efficiency, reducing lead times, removing wasted activities and improving problem-solving capabilities. Once embedded, it will bolster a company’s bottom line. It is not unusual for companies to see potential savings of £50,000 resulting from a lean workshop.
A popular workshop delivered by Fedden USP in conjunction with MIT Skills is the Lean Business Improvement Techniques Adult Apprenticeship programme, consisting of six days of training followed by 12 months’ project support.
Lean principles
Some of the topics covered include principles of lean operations – how to differentiate between which activities add value and which ones are classified as waste; and process flow analysis and process mapping, which are focused on improving productivity by showing operational teams how to identify the steps involved in a task, and how to simplify the activity to eliminate or reduce waste in the process.
An example of the use of this technique occurred in a project at Crowcon Detection Instruments in Oxfordshire, in which the team used tools such as waste walks, process mapping and standard timings to develop a current state process map. Production manager Mark Guest says: “The teams are taught how to identify waste, with games used to teach them about the benefits of ‘flow’ versus traditional batch and queue. They review the current state and identify steps that add no value, which can be removed. A future state process is created that flows instead of batching and this can lead to significant improvements.” Crowcon achieved a 48% increase in volume and 50% reduction in lead time on one manual assembly line. A second project yielded a volume increase of 41% on another manual assembly process, without any alteration to the staffing of the line.
Other topics include effective improvement teams. This is particularly important in process mapping, where impressive results have been achieved by creating a multi-disciplinary team (such as supply chain, design, service engineers, and so on) who all bring different perspectives on what can be done to improve the process.
5S and workplace organisation techniques explains how the organisation of equipment and materials to minimise the movement of operational staff can lead to typical productivity improvements of 15% and reduce cash tied up in stock. 5S is a structured way of tidying up operational areas and, more importantly, maintaining discipline to keep it that way.
Staff-led continuous improvement techniques. This makes sure that the improvements achieved are not only sustainable, but that members of staff are equipped to identify future improvements. This is the cultural change that will makes sure the organisation continues to evolve and stay ahead of the competition.
Improvement project
The workshop also provides delegates with an opportunity to gain a nationally recognised qualification by identifying a specific improvement for their own business, which is then approved and put into effect by the company over a 12-month period, with mentoring support from Fedden USP.
Fedden USP is currently working on a three-year lean efficiency programme with Crowcon. Operations director Frazer Mackay worked with Fedden USP at his previous company, Siemens Magnet Technology, where 268 ideas from employees were put into action, yielding more than £1.3m in operational savings and over 11,900 production hours saved.
Mr Mackay plans to offer all 108 employees in the operations division at Crowcon some form of lean training over the next two or three years.