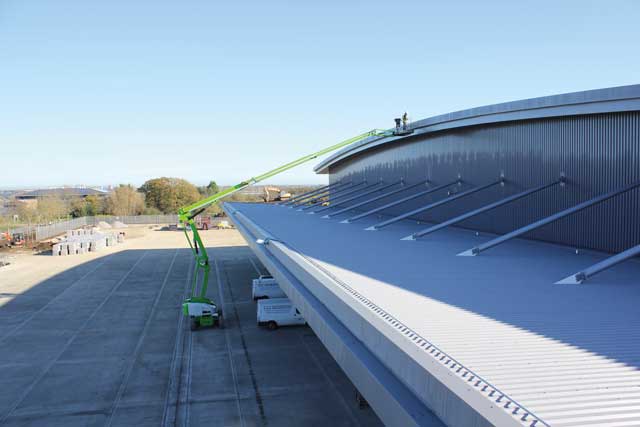
New technological improvements to cherry-pickers are changing the face of industrial maintenance, says Niftylift marketing manager Simon Maher
A cherry-picker is a type of mobile elevating work platform that incorporates a boom to provide outreach to the cage (the operator’s platform). For maintenance tasks, articulating booms offer up-and-over outreach, which is particularly useful for reaching over obstacles such as factory machinery, or racking.
For industrial maintenance, cherry pickers are most commonly self-propelled, meaning that they can be driven from the cage in any boom position. This makes them very efficient for multiple tasks at height, because they don’t need to be lowered and stowed to be repositioned. This saves time, making operators more effective, even when working alone.
Designers are continually seeking to make cherry-pickers more effective. How have cherry-pickers changed and how does this apply to industrial maintenance?
Better performance by design
Using advanced 3D modelling software and techniques such as finite element analysis, Niftylift aims to optimise every aspect of its development process, leading to better reach capabilities; smaller, more compact machines; lower machine mass; outstanding operator safety; and greener power sources.
More outreach, greater access
More outreach is better, but at the cost of extra machine mass. The more an operator can reach from a location, the more work they can do, and the Holy Grail of cherry-picker design is to increase a machine’s outreach without increasing its mass.
Niftylift’s new cherry pickers offer more outreach than ever before, making them ideal for industrial maintenance and inspection.
Compact machines with smaller turning circles can work in more locations. New narrow aisle cherry pickers (with widths of 1.5m or less) can access and work in more restricted locations, making them particularly well suited to warehouse maintenance and working between racking.
Lower machine mass
Reducing a machine’s mass reduces its floor and point loadings. This allows it to work on surfaces with a lower load-bearing capacity, and to be moved from site to site on smaller, more efficient transportation and reduces power consumption during operation.
Niftylift has consistently developed machines with lower than average machine mass, and continues to reduce machine mass on its new models.
Secondary guarding
A significant risk to operators when using a cherry picker, particularly in a busy industrial environment, is “sustained involuntary operation”. This can occur if an operator collides with an obstruction, in such a way as to be forced on to the active controls so the machine continues to move towards the object, potentially worsening the accident.
Many manufacturers have developed secondary guarding solutions to address this. Niftylift introduced SiOPS (Sustained Involuntary Prevention System) back in 2009.
SiOPS is a patented, fully-integrated solution that interrupts all machine movement if the operator is pushed against the controls. Since its introduction, it has been standard on all Niftylift self-propelled machines with working heights above 12m (optional on smaller machines) and is now being introduced across Niftylift’s entire self-propelled range.
SiOPS greatly reduces the risk of injury to the operator and has saved lives, making it an essential feature to expect on any cherry picker being used in the maintenance arena.
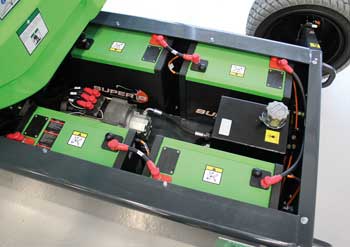
Hybrid and electric power
New environmental initiatives such as the Low Emission Zone in central London and the new Ultra Low Emission Zone (ULEZ) for 2019 mean that the environmental performance of cherry-picker power systems has never been more important.
Hybrids offer lower fuel consumption and emissions, making them a very flexible option for specifiers and operators.
Niftylift introduced a true parallel hybrid cherry-picker with the HR17 Hybrid in 2009, which won the Queen’s Award for Innovatioin 2013. With recent improvements in battery technology and motor efficiency, electric-only power sources are now a viable alternative in a wider range of applications. Its latest maintenance-free absorbent glass mat battery-powered machines offer more than double the capacity of their predecessors, allowing extended duty cycles that can be measured in days rather than hours. This, coupled with better battery monitoring and protection, means batteries last longer, with fewer failures, reducing the running and lifetime costs of the machine.
Cherry-pickers have long offered a safe and efficient method for working at height in the industrial maintenance sector, but these new improvements are now providing measurable benefits both to operators and managers.