The potential productivity gains of digitalisation and the internet of things are being held back by a gap in understanding between operational and IT staff, and IT system capabilities, says Greg Hookings of Stratus. David Fowler reports.
The industrial internet of things coupled with digitalisation and connectivity has promised great advances in industrial automation, and improved efficiency of production processes through predictive maintenance and reduced downtime.
But progress has been slower than expected, according to Greg Hookings, business development manager of computer server and software manufacturer Stratus Technologies. This is, he argues, partly because of the OT/IT gap – a gap in communication and practice between operational technology staff and their counterparts in IT, and the shortcomings of current IT systems.
This is taking place against a background in which the value of data is increasing. Users in industry collect increasing amounts of data from their production processes, but have four important needs. They want to be sure the data is not being tampered with or stolen; they want a computer, network and storage system with no downtime; they need applications that work together seamlessly and are scalable; and they want the ability to remotely manage their technology and predict a failure before it happens.
Today’s IT systems, Mr Hookings said, are characterised by post-failure analysis and limited data collection end points. OT managers want increased efficiency, and reduced or even eliminated unplanned downtime.
But currently OT staff do not have an in-depth knowledge of IT systems; they rely on third party relationships to manage their IT. Conversely, IT staff don’t have a deep understanding of operational needs.
Barriers to progress
If the gap between the worlds of IT and OT is one barrier to digitalisation, another is today’s systems. Current factory systems are reactive, complex and “IT heavy”, said MR Hookings, requiring constant monitoring. Mixed operating systems (Windows, Linux and so on) leave potential holes in cyber security. Each system is individually managed.
A common complaint includes: “IT does a great job of scheduling planned downtime but not when unplanned breakdowns occur”; and OT staff are inhibited from changing any given aspect of the process for fear of causing knock-on problems elsewhere: “Our systems are so old and fragile we daren’t change anything in case it breaks” is commonly heard.
Stratus specialises in IT systems providing continuous availability. Its vision is for the future is “Hybrid OT”, in which OT and IT functions merge or integrate.
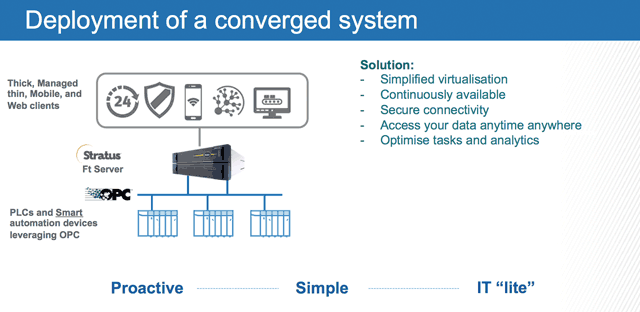
The result is an environment in which OT specialists can drive and own their own automation innovation. Staff combine an OT foundation with IT skills, and are more self sufficient. Objectives are shared and new IT tools are available to help them.
Attributes of a converged system would include less process variability, with fewer process upsets, improved production and lower energy consumption; more consistent process quality, more in line with customer expectations and with reduced waste; and improved performance of production assets, with reduced unplanned downtime.
From an IT standpoint, a converged system would be “active, simple and IT-light” said Mr Hookings, and it would have much simpler architecture. The Stratus ftServer (for “fault tolerant”) is designed with converged systems in mind. Instead of a server for each application, it allows the creation of multiple virtual servers within a single unit, requiring next to no IT skill to manage. “You are able to do a lot more with the one piece of hardware,” Mr Hookings said. This includes predictive remediation, secure connectivity to plant floor devices (via OPC), and access to data from anywhere at any time. Staff resources associated with IT support are greatly reduced.
Whereas standard servers today, or clusters of servers, only allow for failure recovery, not prevention, the converged system has no hardware point of failure.
Even in a critical event, said Mr Hookings, reserve capability allows applications to keep running, providing not back-up and recovery, but continuous availability.
The single package is easy for OT staff to install. All IT maintenance is done remotely.
A number of algorithms running on the server provide predictive failure modelling for the plant processes so that impending failures can be seen before they occur, and the customer can address the problem in advance. Stratus engineers can examine the diagnostics data remotely and advise the customer how to improve the performance of machines on the shop floor.
Even if the IT system crashes, the server has application monitoring and automatic restart so even in a critical event the system can keep running through it.
In the worst case scenario, if the server or a component has to be replaced, the server triggers the process automatically, a replacement is ordered and delivered overnight, and it can be fitted without shutting down the system.
Overall, a converged system will free OT staff from focusing on keeping the process running to thinking about how it can be improved, Stratus argues.
Mr Hookings concluded: “The point is that once you get security on the IT/OT layer, that operational simplicity allows hybrid OT staff to focus on the capabilities of IIoT for innovation.”