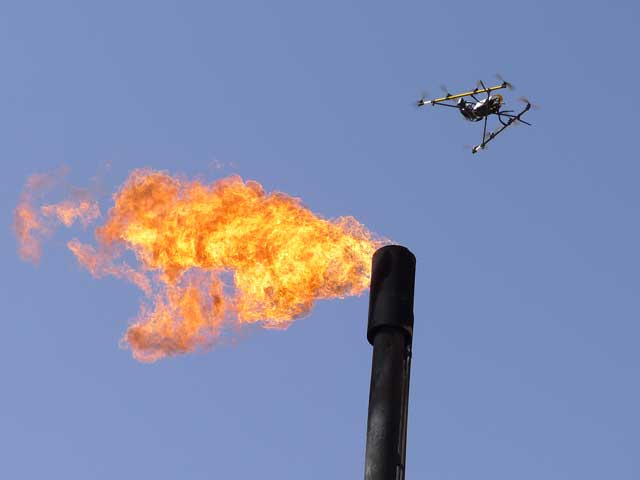
Use of drones in maintenance and inspection can avoid shutdowns and reduce the need to work in potentially hazardous areas, says Phil Buchan, Cyberhawk Innovations commercial director.
Monitoring the integrity of assets is becoming ever more important in the energy sector. The number of assets which need to be managed is huge and continues to grow. There is demand for improved and more efficient maintenance, repair and upgrade decisions, often with time-based regimes being superseded by risk-based ones. This means demands for larger volumes of data and higher quality information to prioritise, plan and execute projects.
Cyberhawk Innovations, based in Livingston, Scotland, has pioneered aerial inspection and survey using unmanned aerial vehicles, otherwise known as drones, and has been using the technology to conduct close inspections of live and difficult to reach structures since 2008.
Structures inspected include live flares, turbine blades, meteorological masts, and transmission towers. Removing the need for access by maintenance staff can avoid lengthy mobilisation processes as well as removing the need for staff to work in potentially hazardous situations.
With a clear, 360-degree view, drone technology has revealed detailed and new information to operators that was previously inaccessible, fundamentally changing the accuracy of inspections.
Drones in action
UAVs are typically used to conduct a “first sweep”, or to scan an asset. This means numerous challenging tasks can be completed in a short time on one mobilisation. The detailed imagery and high-quality inspection reports may show that no further action is needed. However, if repair or maintenance is necessary, personnel will still be required to undertake this work, but may only need to access specific areas identified by the UAV inspection.
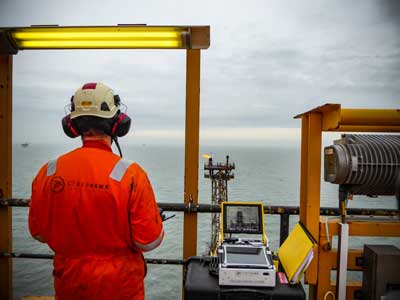
As awareness grows, more and more companies are turning to inspection by UAVs. In the current market, significant cost savings are a key benefit. Much of these savings are gained through the ability to inspect an asset while it is still in operation, avoiding shutdown and production losses which can run into millions of dollars daily. Using UAVs in the first instance means that a shutdown is only required if the data collected identifies a maintenance issue which needs to be addressed.
One client made a saving of $2.3m (£1.7m) by using a UAV, avoiding the need to mobilise an abseiling team and shut down a live flare, which would have taken around seven days to complete.
The health and safety advantages are also significant. Inspections are often required in hazardous areas. Using a drone removes the need for personnel to be placed in potentially dangerous situations.
The quality of data produced by Cyberhawk UAVs is extremely high. The team has the technical skills to fly close to the structures it is inspecting, capture all the relevant data and imagery, and provide engineering inspection reports through its cloud-based visual asset management software, iHawk.
The software converts drone-captured imagery into information which can be used to make quick and effective asset management decisions. Operators can prioritise maintenance by condition, budget, location and more.
Proven track record
Cyberhawk pioneered UAV industrial inspection in 2008, and has built up a strong portfolio of inspections in the oil and gas, wind and utilities sectors. This has included live flares, underdecks, turbine blades, meteorological masts, chimney stacks, transmission towers and so on. Last November the company conducted a nuclear world first, inspecting two concrete PWR containment domes for American Electric Power at the Cook Nuclear Plant. This was the first time a drone had been used to conduct an inspection to the American Society of Mechanical Engineers Section XI Code.
The company is constantly looking to push the limits of what can be inspected. Prior to October 2015, drones had not been flown into confined spaces offshore, but Cyberhawk broke this mould by completing the world’s first internal tank inspection on board a Maersk floating production, storage and offloading installation. This type of inspection is usually conducted using rope access technicians to inspect the internal tank.
Not only did the UAV solution offer dramatic safety benefits during the tank inspection, but also significant cost and time savings. The inspection of the critical components of the tank was completed within a day, in comparison with a rope access inspection, which would usually take between three and four days.
The future
For the future, advancing UAV technology is the next step, ultimately improving the overall quality of inspections and the value of the information provided. By doing so, it will become possible to repeat inspections precisely to measure state of change, leading to more accurate predictions on asset maintenance.