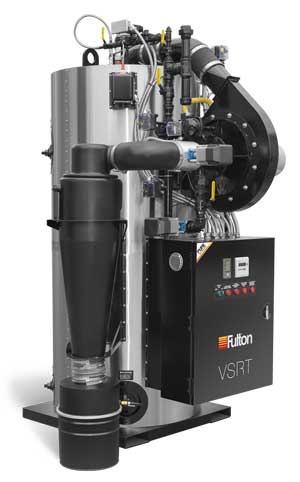
Aiming for higher efficiency, lower emissions and ease of maintenance, Fulton set out to rewrite the rules of boiler design in developing the new VSRT. David Fowler reports
Boiler design has changed little in the past 50 years or more – indeed some aspects of conventional designs can be traced back to the nineteenth century.
But when boiler and heat transfer specialist Fulton came to design its new range of steam boilers it decided to start with a clean sheet.
“Instead of taking the current design and trying to improve it, we went back to first principles with a new team of engineers and designers,” says Carl Knight, Fulton UK managing director.
The result is the new Fulton VSRT (vertical spiral rib tubeless) steam boiler, which promises high levels of efficiency, low emissions, high steam quality, ease of maintenance, and a compact footprint.
The new range is expected to find a market in similar applications to current vertical boilers, notably food manufacture, microbreweries and distilleries, and other processes such as pharmaceuticals, as well as in laundries and dry cleaning. Initially available in outputs up to 960kg/h, the range will be expanded during the course of this year.
Fulton pioneered the vertical tubeless steam boiler in 1949, and one of the requirements for the new design was that it should also be tubeless, for robustness. ”When you introduce tubes you introduce the likelihood of increased thermal stresses and, without the correct water treatment, scaling or oxygen pitting. Each tube has to be welded into place and each weld is a potential weakness,” says Mr Knight.
But for the VSRT, the tubeless approach underwent a rethink.
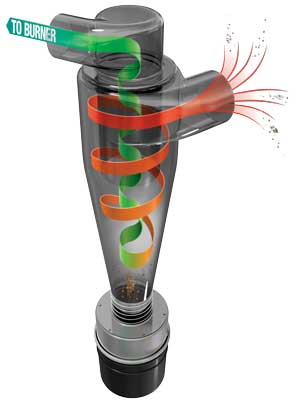
A helical heat exchanger was adopted to allow the maximum length for heat transfer in a small area.
The design team was led by Dr Carl Nett, formerly of United Technologies, the parent company of jet engine manufacturer Pratt & Whitney. He brought “a completely different set of ideas and methodology” to the process, says Mr Knight. Heat transfer and expansion were fully modelled using computational fluid dynamics and finite element analysis to make sure the design worked in practice as predicted in theory. “Thermal stresses are low and there is virtually zero expansion,” says Fulton UK sales and marketing manager Leigh Bryan.
Design objectives also included improved emissions and a higher efficiency than current designs. Efficiency of 2.5 percentage points above current designs is promised over the boiler range in standard form, as are ultra-low NOx emissions. This is thanks to a new approach to burner design. Fulton worked with world-leading mesh burner manufacturer Beckett Burners and its subsidiary Worgas to optimise the boiler and burner design together as a system for each model. “In the past, the manufacturer designed the boiler and then turned to a burner manufacturer to match it,” said Mr Bryan. “For the VSRT, the burner design is matched to each boiler in the range.” This allows high turndown ratios from 6:1 up to a genuine 10:1, depending on the model.
NOx emissions are said to be an ultra-low 20ppm. The boilers will meet not only the 100mg/m³ NOx requirement of the EU Medium Combustion Plant Directive; the entire range will also meet the planning requirement for new commercial developments from the City of London 2015-2020 air quality strategy of less than 40mgNOx/kWh.
And the range up to the 60 model (960kg/hour) will operate on gas pressure of 18mbar (standard mains pressure is 20±1 mbar).
One of the company’s biggest markets in the US is for dry cleaners and laundries, where lint and fluff has to be prevented from getting into the burner. Fulton has designed a new cyclonic air filter that moves combustion inlet air in a spiral to separate lint and other airborne particles (10 microns or above) and drop them into a canister which can easily be removed, emptied and replaced. Unlike traditional filter media, this is achieved without a pressure drop or reduced flow rate.
Maintenance is also designed to be simple. There are no refractory materials (or fire bricks), which are commonly used around the burner as a heat shield and need to be replaced every five years. The heat exchanger is fully wetted along its entire length.
Standard insulation is employed to insulate the jacket, where commonly a not particularly effective layer of refractory would be used. All this contributes to light weight and low surface temperatures. Because the boiler is tubeless there is no need for periodic ultrasound testing of welds. The VSRT simply needs to be pressurised to 1.5 times standard working pressure at intervals. All this will contribute to keeping lifetime costs low, says Fulton.
Water level control is accomplished using a tuning fork/guided wave system, a technology which has been in existence for many years but has generally been confined to boilers in applications such as power stations because of its relative cost. Its accuracy is not impaired by foam or a build-up of dissolved solids.
The VSRT is available to order now in capacities from 160-960kg/h, with plans to expand the range to 4000kg/h (2.5MW) later this year, covering around 80-90% of the market. “By next year we will have the full range, which will easily comply with the MCP directive and City of London air quality strategy, available for applications right across Europe,” says Mr Bryan.