Asset management in industry is now about much more than regular maintenance. Paul Hingley, Head of Data Services for Siemens Digital Factory, Process Industries and Drives explains how innovative technology is helping all types of industry to interpret production and control data more effectively, to make processes and equipment run more smoothly, more efficiently and for the longest possible time.
In industry, total productive maintenance (TPM) is a system of maintaining and improving the integrity of production and quality systems through the machines, equipment, processes, and employees that add business value to an organisation. Here, data has an enormously important role to play, since by improving the quality and interpretation of what is effectively feedback on how a process or system is operating, improvements can be made, often all the way down the line.
These can include basic operating processes (why have a motor or fan running when it’s not required? Extend its life and save energy by using it only when needed) as well as better safety procedures; advanced condition monitoring of moving elements to predict and advise when maintenance is necessary; and teams which can more fully interpret data in order to improve various processes and increase the reliability of the entire system. Added benefits include lowering energy consumption, reducing carbon footprint, and better automation of analytics so that more monitoring can be done by clever software.
Intelligent maintenance in action
In the water industry, for example, Siemens has introduced a motor management system called Simocode which monitors submersible pump performance and automatically reverses pump actions when criteria are detected that may indicate potential blockages (such as to the pump running at a higher current). By using this system one water company’s pump blockages were reduced by 70% within a year, also saving time for its engineers in not having to attend and regularly sort out blockages. Benefits included a dramatic reduction in downtime for customers, and benefits for total expenditure from a scalable solution with simple deployment and the flexibility of either a networked or stand-alone configuration.
As with many of the latest software programmes using plug-and-play technology, no new software tools have to be learned and no extra time is wasted in learning new software skills. The water company is planning to extend the use of the system to other sites.
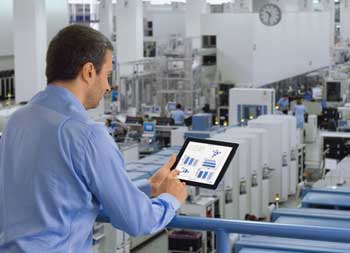
In the construction industry, a global manufacturer of insulated cladding panels with factories in the north of England has the ambitious aim to make all its plants net zero energy by 2020. It opted to use Siemens’ energy performance contracting to reduce the energy use of its plant management systems, compressed air systems and lighting by using an automated monitoring and targeting system. This helped identify a number of additional energy savings that could be made, including on the company’s discontinuous laminator. Considerable savings were made by modifying the operating procedures relating to that plant, with a 60-month payback period on the investment. Super premium efficiency IE4 motors were part of this investment, which is now into year 3, and the savings being achieved are above target because the monitoring and targeting system is working so well.
Whatever the industrial application, and whether energy savings have a faster or slower payback time, making the decision to invest in energy savings produces surprisingly big benefits beyond the initially predicted savings. Data analytics is a natural step in the digitalisation of plants and operating processes, and not only provides far more useful information, but also permits the best predictive maintenance right through to TPM, whatever the process.
Rail asset management
Developed for the rail transport industry, the mobility-specific platform Railigent helps to increase availability, improve efficiency, reduce operational risks and costs and improve maintenance. It includes remote monitoring, fast diagnostics and preventive failure prediction for rolling stock and Infrastructure worldwide. Examples include visualisation of vehicle health status and location; prediction of component failures for gearboxes, bearings, traction motors, doors and power transformers; operation support; analysis of error conditions; prediction of point machine failures; and throughput analysis for rail networks.
Proven outcomes for rail companies are:
- Prescriptive maintenance – with proven availability of over 99%
- Optimised operation planning – with up to 20% fewer delays
- Transparency in real-time – with GPS positioning and hundreds of sensor readings per second for a high speed vehicle
- Root cause analysis – reducing complex fault resolution times by more than 20%.
With Railigent connected to the Siemens MindSphere system (see below) the customer is furthermore able to improve the asset over its entire lifecycle. For example, a rail operator can improve not only the availability of its rail vehicles, but also the operation of stations and optimisation of energy consumption.
Analytics for rotating equipment
To safeguard productivity and availability of production at any time, smooth operation of rotating machines in production environments is the key. An important tool in optimising availability is to establish cloud-based, condition-based maintenance for drives, motors, and gear units, while taking advantage of the manufacturer’s knowledge and expertise. A condition-based maintenance plan allows the user to find the best match of maintenance measures and production plans. Early detection of upcoming faults is essential for an optimised condition-based maintenance plan. Drivetrain analytics running on MindSphere provide the connectivity, analytics and visualisation required in order to take advantage of the latest technology and innovation to maximise the performance of rotating equipment.
MindSphere
MindSphere is a cloud-based open internet of things operating system that is effectively Siemens‘ cloud for industry. It is a comprehensive data-hosting platform that allows the connection of devices and assets at industrial plants in an automated production environment. It securely stores operational data acquired and transferred from these assets. By letting you seamlessly connect with your machines as never before, it makes it possible to improve the efficiency of plants by harnessing the huge volumes of data that these assets generate – and it lets you integrate your own apps and services, too.
Manage MyMachines running on MindSphere monitors machine tools worldwide for their availability and productivity at small or large production sites. With little effort, users can see machine utilisation and performance, and can thus reduce costs and improve service and maintenance. Furthermore, machine tool builders can start developing new digital services. Manage MyMachines interfaces Siemens’ Sinumerik 840D sl computer numerical control system to MindSphere in a simple and intuitive way – with additional Siemens as well as third-party control systems on a master layout of the plant.
With MindApps for industrial cyber security, companies can quickly identify threats, security loopholes and anomalies in their production environment. Industrial control systems become more and more interconnected, which increases the risk of cyber or operational incidents in the field. MindSphere will be a central source for security applications, reports, security alerts and services in the future.
Creating the digital twin
Digital twins are intelligent virtual models that accurately duplicate and simulate the real-world properties and performance of physical products, production lines and processes. Digital twin software and digital services allow digitalisation of the entire lifecycle, seamlessly integrating product, production and service processes. MindSphere connects to real-world devices and processes, and feeds performance data back into a performance digital twin to drive improved decision making and intelligence.
By creating digital twins, a growing number of industrial users are able to improve performance at their new facilities before a single real item has even been commissioned. Throughout the product lifecycle, digital twins continue to make possible tremendous productivity and efficiency gains, providing companies with the means to design, simulate, validate and optimise products, processes and plants in the digital world.
Whether you need to obtain status data from energy meters, moving assets like trains, air conditioners, individual drives and conveyor systems, or any other type of industrial process, establishing digital connectivity can now be accomplished much faster, often without requiring any asset downtime. This enables companies quickly and inexpensively to gather and feed performance data to MindSphere for analytical purposes, in both existing and IoT environments.
The internet of things and digitalisation are already a reality, offering opportunities for product and business model innovation which could not have been imagined only a short time ago. The future opportunities for industry are tremendous.