ABSTRACT
The avoidance of serious machine failures through the detection of incipient faults is only the first part of the benefits deliverable by a condition monitoring programme. Better still is to avoid the faults in the first place, by correct installation and operation. And the vibration analyst – through involvement in the processes of design, specification, acceptance testing, repair, alignment, FMECA, and more – can do much to ensure this.
We all know what a great job vibration analysts perform. They are all that stands between a manageable plant and the chaos and mayhem that can result from machines failing unexpectedly. It takes skill, knowledge and experience to be a good vibration analyst. But in many cases they are only delivering half of the benefits they are capable of.
Detecting faults so that catastrophic failures can be avoided is important, but what about avoiding the faults in the first place? If a machine was balanced, aligned, lubricated and operated correctly, and if all the issues related to installation and commissioning were attended to, then a plant would see far fewer fault conditions develop. The vibration analyst may not be responsible for all or, in some cases, any of these issues, but there is a great deal that an analyst can do to ensure that these issues are taken care of. Here, I will explore how the analyst can make a difference.
The benefits of defect elimination
When an analyst detects a bearing fault the question must be asked: why did it occur? Was it due to excessive load on the bearing due to the way it was operated or because of unbalance, shaft misalignment, belt misalignment, resonance, belt tightness or some other reason? Was it because of the way the bearing was installed on the machine – cocked on the shaft or in the housing, or damaged by hammer blows? Was it poorly lubricated, or was the lubrication contaminated, or had the lubricant lost its key properties? Was the bearing damaged by false-brinelling during transportation, or in stores, or while the machine was in standby mode? Was the bearing loose, or were the rolling elements skidding, or was there electrical discharge machining (EDM) damage?
Unless the bearing failed after surviving for its design lifetime, no matter what caused the bearing to fail, the cause was avoidable. And that goes for all other failure modes – broken rotor bars, wear due to cavitation, broken gear teeth, and so on – the root cause was avoidable.
Let’s see how we can avoid those causes.
Reliability spectrum
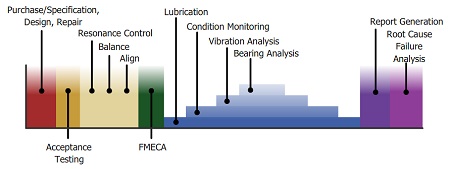
I believe that the ‘reliability spectrum’ (Figure 1) represents all of the areas where an analyst can be involved to improve the reliability of rotating machinery in the plant.
Let’s start from the left and deal with each issue, one by one.
Purchase and specification, design, repair
The vibration analyst is not responsible for the purchase and specification, design and repair of rotating machinery, but it is very important that they use their experience with rotating machinery to influence these functions. If machines that are designed to be reliable are purchased instead of machines that meet minimum requirements, and if repair facilities of high quality are used instead of those that offer the lower price, then there is no doubt that the cost of ownership will be dramatically reduced.
Reliability must be treated as a non-negotiable aspect of the design and selection criteria. Yes, using reliability as a selection criterion will result in a higher up-front cost, but the years of reliable operation (and lower energy consumption, where applicable), will repay the investment many times.
Acceptance testing
In addition to demanding reliability in the purchased or repaired machinery a testing regime must also be specified. As a minimum, specify maximum vibration amplitudes and do not accept the equipment unless it passes the test.
The acceptance test specification will likely need to also specify the operating speed and load under which the test is performed, and the test may need to be performed at your site (if the vendor cannot reproduce the operating conditions).
Resonance, balance and alignment
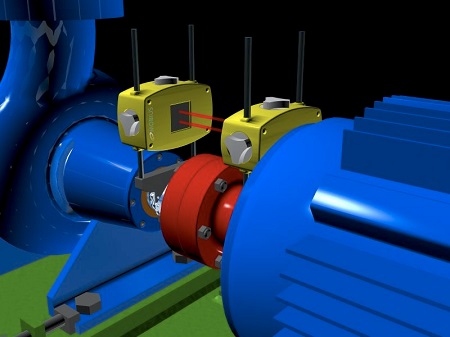
When a machine is precision balanced and aligned, when it does not excite any natural frequencies (i.e. cause resonance), when the belts are tightened to the correct tension, and when it is operated correctly, then it will operate in a smooth condition with minimum load and stress on all of the components – including the bearings, seals, shafts, coupling, hold down bolts, etc. The vibration analyst –
- should be able to perform in situ (field) balancing, and should oversee the ‘shop’ balancing activity,
- may perform the laser alignment (see Figure 2), or should at least check to ensure the machine was precision aligned,
- may not have any control over the operation of the machine; however, they can provide feedback that demonstrates to operators why the machine needs to be operated correctly,
- may not be involved with installing bearings, setting belt tension, and so on, but again can provide valuable feedback so that the people who perform that work do understand how to do it correctly and the importance of doing it correctly.
Failure Mode Effects and Criticality Analysis [FMECA]
Before we can discuss the condition monitoring activities it is essential that the failure modes of the rotating machinery are understood. You must determine which technologies can be used to detect the early signs of the failure modes, and you must understand what the P-F interval is (i.e. how much warning you will get). With this information you must add the criticality analysis – what is the importance of the machine and what will be the effect of the machine failing? Each condition monitoring test performed costs money, and that expense must be weighed against the probability of detecting the fault and the financial (and other) effects of allowing the machine to fail.
It is only after such an analysis that you can be sure that your condition monitoring programme will provide the financial benefits that are required to justify the programme.
Lubrication
Correct lubrication has such a dramatic effect on the reliability of a machine that it simply cannot be overlooked. The vibration analyst may not be involved in the lubrication process, or the analysis of the lubricant, but as with other areas of the reliability improvement programme, the analysts must at least be another voice that continually stresses the need for machines to be lubricated correctly.
Lubricants must be selected, stored, and dispensed correctly, and contamination must be minimized. It is also critical to periodically check whether the lubricant is still fit for the purpose, and that there are no signs that a fault condition has developed.
Condition monitoring
Obviously, the condition monitoring programme is very important. But there is one point that must be stressed. There is an unfortunate habit – an undue focus on bearing fault detection above everything else – that many vibration programmes have developed over the past five or ten years. Detecting and correcting unbalance, looseness, misalignment, resonance and a wide variety of other conditions are often overlooked because it is believed that these conditions (unless extreme) will not cause the machine to fail. Instead, the analyst uses (often limited) bearing detection techniques and simply waits until the bearing shows sign of wear, and then action is taken at the latest stage possible.
As already stated, if the other conditions, such as unbalance, misalignment and resonance were detected and corrected at an early stage the analysts would see far fewer bearing faults – and the organization would save a great deal of money (and the safety record would also improve).
Report generation
One of the reasons why many condition monitoring programmes fail is the weakness of the reporting process. The following are just some of the problem areas.
- Reports are unclear – they do not clearly state what is wrong with the machine nor do they indicate the urgency of the recommended maintenance action.
- Reports are not accessible by the people who need them; it is essential that all decision makers and other affected parties are informed about machine condition at the appropriate time.
- Reports don’t utilize all of the available data; data from oil analysis, motor current analysis, infra-red analysis and the ultra-sound program should be used to provide one, integrated, informative, actionable report.
Root cause failure analysis
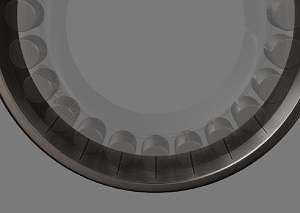
When you consider all that has been written in this article, root cause failure analysis is the most important aspect of all. Too many analysts make their report and believe that their job is done. That could not be further from the truth. The analyst should check the machine and make sure that the diagnosis, and the stated severity, was accurate. When a bearing is removed from a machine it should be retained, opened (carefully), and the raceways and rolling elements studied so that the root cause may be determined (see Figure 3). The history of data should be reviewed in order to investigate whether there were earlier signs of another fault condition (unbalance, misalignment, resonance, etc.) that may have lead to the failure of the component (a bearing, for example) in question. All of the data should be studied carefully for tell-tale signs of the root cause of the failure.
Conclusion
Monitoring the condition of rotating machinery with vibration analysis is an essential part of any cost reduction (and safety improvement) programme, but the best results are achieved when the condition is improved. An investment may be required to make the necessary improvements, but employee job satisfaction (and safety) and corporate profitability will be the beneficiary.