ABSTRACT
The authors discuss why industry is still prepared to accept a poor quality of process water filtration, the risks of doing so and why advanced media filtration technology is the answer.
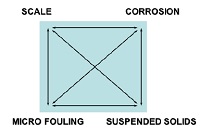
Engineers, manufacturers, utilities, public and private enterprises and commerce in general (in fact, anyone that uses water for temperature control) are, for the most part, quite comfortable in the belief that they are operating an effective and safe water system – but how safe are they really? The general guidance is that a chemical treatment regime must be put in place, with adequate monitoring, and that this treatment programme must provide the control of four key elements, listed in Figure 1, that can affect any cooling water system.
Generally, water treatment chemicals used together with pre-treatment plants will adequately control the potentials for scale, corrosion and biological fouling. But what about suspended solids control? Due to the air scrubbing effect of, for example, cooling towers the potential for suspended solids to increase is always present, and suspended solids contamination can come from many sources, such as wind-blown dust and seeds, pipe work corrosion, system contamination from process, changes in raw water make-up or other local issues.
Of equal importance is the potential for airborne microbiological spores to be sucked into the cooling water, as air is either induced or forced through the tower. Most cooling tower operators are unaware of the number of air born spores that are present at their particular cooling tower location. The types and number of spores will vary on a seasonal basis as well as geographically; there is a distinct difference between rural and industrial locations as well as coastal and inland installations.
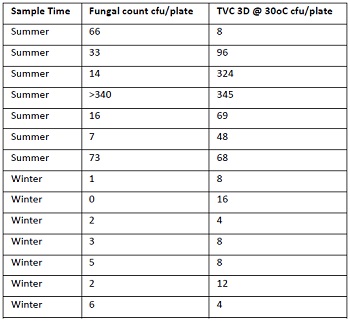
Table 1 illustrates the typical numbers of fungi and bacteria that can be found adjacent to an industrial building. These counts are obtained by leaving agar plates exposed to atmosphere for twenty minutes. Any fungi or bacteria that are then grown are from spores that happened to fall on the plates by simple gravity. By taking into consideration the air flow characteristics of each cooling tower an estimate of biological loading can be theoretically calculated. Typically, in the summer months each cooling tower has the potential to ingest thousands of spores every hour.
A common practice to enhance the performance of the total water treatment programme is the inclusion of side stream filtration, this being the standard practice for the reduction of solid loading in a system. In reality, very few cooling systems are fitted with any form of filtration device, apart from strainers that are usually designed to protect the circulation pumps. Those that do employ filtration tend to be operating larger systems, or have problematic units when, commonly, filtration is retro-fitted once fouling has become established. The majority of medium or small systems tend not to have any filtration, either side stream or otherwise, in spite of widespread support and advice by the HSE and industry specialists. The operational benefits of effective filtration in cooling water are very significant, not only contributing to good microbiological maintenance but also to maximising heat exchange efficiency and reducing maintenance costs.
As in all technologies, water treatment and cooling systems have advanced, so we now have systems that operate with cooling water that will stop production if the temperature or pressure of the water is not within defined limits. Arguably, it should therefore be best practice for good water quality maintenance to be taken into account during the design and planning phase of a cooling water process. Dealing with cooling water fouling is much more difficult and costly than preventing it in the first place, not to mention problems associated with unscheduled down time.
We need to fully understand the implications of what is within the cooling water, but many of us are feeling very safe having installed traditional technologies such as side stream filters. Typically, these are kinetic or centrifugal separators, or other technology such as self-cleaning screen filter, disc filters or even conventional media filters. Such systems, combined with chemical treatment, are accepted as standard practice.
All of these technologies filter to their limits, which is at best around 15-20 micron. When we have examined water samples from many systems they all typically show a solids loading of anywhere from 10 mg/l to 80 mg/l of physical matter (some even more if the make-up water is not mains water, i.e., borehole water, river water or lagoon water). The issue is that when cooling water is sampled with an accurate laser analyser they all show remarkably the same graphic profile. The following two examples illustrate this.
The first is what would be deemed clean water with a solids loading of only 6 mg/l, yet the particle count is 18,195. Examine carefully the charts below (Figures 2 and 3). In each, the horizontal axis shows the micron range, 1-5 through to 52-100 micron, derived from a laser analyser used specifically for this type of water evaluation. The charts show the particle number (Figure 3) and also the associated mass of the range (Figure 2). The issue is in the detail, if we look at what a typical side stream filter would remove. Even at an assumed 100% performance at its top limit of 20 micron – well, let us be generous and say 10 micron – the loading removed by mass would be 5 mg/l out of a total of 6 mg/l, some 84% of the total solids load, which is impressive, but in reality not achievable. Up to recent times this would be accepted as good. But we need to remember that existing technologies employed as side stream filtration do not perform at 100% efficiency
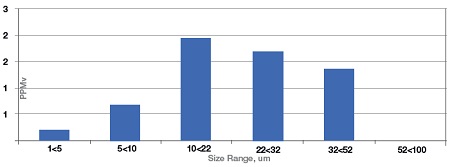
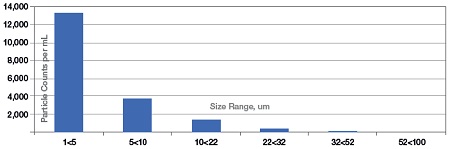
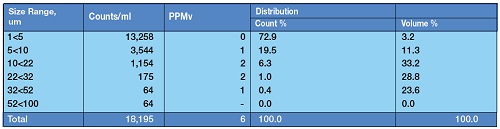
But now let us examine the counts/mL in Figure 3 and in Table 2, what we see is that the distribution of the number of particles in each sector of size is the reverse picture of that of the mass.
This is simple to explain: the larger particle weighs more than the fine particle. E.g. how many bacteria weigh 1 mg? – but it only takes a few grains of sand to weigh 1 mg, so in our first example, a good traditional side stream filtration, while removing more than 84% of the mass (assuming 100% removal efficiency at 10 micron again, which is not normally possible) has only removed some 1390 particle counts from a total count in the sample of 18,195, i.e. an efficiency of less than 8% removal. We therefore have a situation that allows a constant build-up of smaller particles within the re-circulating water.
What is the real adverse effect of these smaller elements, many of which are micro-organisms, on the system? Well, in most systems the process cooling water is passed through the system in pipe work and then, if a cooling tower is present, it is passed over the cooling area of the tower, or through a chiller or heat exchanger. Now even in the best of systems, and most do not fall into this category, the pipe work will be plastic, steel, stainless steel, or as in many systems a combination. All of these pipes have a single thing in common, their internal surfaces are not completely smooth. Looking though a microscope we will see surface inclusions and roughness, which are the very locations that these smaller elements affix themselves to. The larger particles do not as they have a larger surface area and so mass and, as such, are swept along through the system by the water flow.
The process which is happening is that these smaller particles, typically less than 5-6 micron, lodge themselves in the pipe work surfaces and system cooling surfaces. Some of these may well be dispersed by water treatment chemicals but many hold their position (typically in areas of low flow) and start to build up what is, in effect, a slightly smoother surface. These particle holding areas then provide a suitable habitat for biological colonisation which will lead to bio-film formation. These bio-films then provide an enhanced environment for further colonisation and act as a filter for further inorganic salts to build as well. While many of these bio-films are invisible to the naked eye they can increase the corrosion potentials at the metal surface and provide areas for rapid bacterial growth. Biofilms will ultimately provide an environment where water treatment chemicals cannot function, and can enable huge numbers of different bacteria species to proliferate.
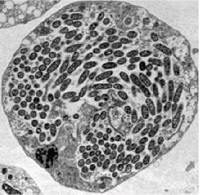
A mature bio-film will be a very complex structure with contains both aerobic and anaerobic bacteria together with protozoa. The inclusion of protozoa is a major factor in the ultimate colonisation of a system by Legionella bacteria. These are protozoonotic in that they live, reproduce and survive within certain free-living amoebae and ciliated protozoa as facultative intracellular parasites. In this relationship, the protozoa are obligate cellular hosts in which Legionella replicate and thrive, as well as gain protection from harsh, natural or man-made, environmental conditions. If the particulates contain iron, this will also act as a major food source for Legionella.
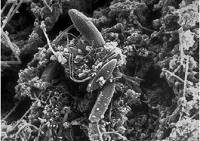
So what is the answer to minimising the potential for these small particles to cause water treatment problems and significant biological issues? It is effective and reliable side stream filtration that can remove these smaller elements and minimise their contamination of the system. Which is why our own company has invested in the design and development of advanced high efficiency media filter technology – which, for a number of years now, has been installed with great success, delivering considerable increases in system efficiency in industries worldwide. Such technology can filter to better than 0.5 micron, fully automatically, and can be installed on a side stream of any cooling system whether a cooling tower or a chiller.
CASE STUDY 1
In a high capacity plastic moulding shop, curing time had risen from an accepted design figure of 12 seconds to 16 seconds. Not much of a difference to the non-industry onlooker. However, to an expert, if you are producing a plastic item every 3 seconds this equates to 1200 units per hour. If the curing time increases by 4 seconds that is effectively an increase of 25%. From the manufacturer’s point of view, production is now down by 25% which equates to a decrease to 900 units per hour, which is a huge loss. In many cases manufacturers will simply accept this loss because they don’t realise where the problem lies, having overlooked process cooling water quality. They then buy more equipment to bring production back up to previous levels, which in turn becomes a vicious and expensive circle.
The solution in this case was to replace the existing centrifugal separators with our own high efficiency filter on a side stream loop to enable the mass water to be filtered to less than 1.0 micron. Following the installation the system water quality improved to the point where the curing time was brought back to its original specification, saving the company the high investment of purchasing another three moulding machines which would have been required to meet orders.
CASE STUDY 2
In UPVC extrusion many clients experience chemical control problems with their large recirculation water systems (200,000 – 500,000 l/hr typical recirculation rates) after a change in EU law banned a traditional component in the raw material used for achieving a smooth surface finish on the product. When the new formulations started to be used there was a major increase in the biological content of the water, necessitating shock dose to very high levels, at very regular intervals. The level of shock dosing was too high for on-site safety so a solution was sought.
The main extrusion line already had main full flow filtration down to 20 micron, so there was little to be gained at this point by installing traditional side stream technology. The solution was to install our high efficiency cross flow filter to enable the removal of solids down to below 1.0 micron.
Many UPCV manufacturers are now using this technology, which has been proven to save money and maintain a high quality of recycled process water, while at the same time reducing scrap and improving productivity, thereby reducing energy per ton manufactured.
In conclusion, by not properly understanding, treating and filtering out the finer particles found in process water, the effect on cooling systems is minimal but bio-fouling is still an issue. By installing the correctly sized side stream high efficiency filter, which should also be self-cleaning, the user benefits in a number of ways:
- Substantial increase in biological control
- Less chemical use but more effective control
- Reduction in the potential for erosion corrosion
- Reduction in the potential for bio-film proliferation
- Enhancement of the efficiency of conventional water treatment chemicals
- Cleaner heat transfer systems
- Reduction of energy comsumption by as much as 20%
- Greater security and peace of mind for the operator and user
INDUSTRIAL PURIFICATION SYSTEMS
For over 30 years Industrial Purification Systems Limited (IPS) has developed experience in the field of industrial and commercial water filtration. Its broad product range of filters enables the company to offer equipment solutions that are not only effective but also commercially and environmentally acceptable. The varied filtration solutions that have been applied world-wide have covered all business sectors: commercial, industrial, manufacturing and public and private utilities.