ABSTRACT
The costs of compressed air generation and leakage and the identification of opportunities for energy savings in compressed air systems are reviewed. The practical implementation of such measures is then discussed in some detail, and the subsequent rapid return on investment illustrated by a short case study.
Introduction
In order to survive in a tough competitive environment, many companies are searching for ways to make savings in their production. Such savings can often be found in their existing compressed air systems, which have generally been in place for years. Up to 60% of energy costs can be saved through optimisation at both the production facility and system level. However, companies can only achieve this target by considering the compressed air system as a whole. All areas, from generation through preparation and distribution to application, must be taken into account and factored into the choice of subsequent measures. The necessary equipment must also be available for performing reliable analysis and implementation. In many cases, the measures have a positive effect in that they reduce the need for future maintenance. Since potential sources of failure are being eliminated, general process reliability and productivity will increase.
What Are The Costs of Compressed Air Generation?
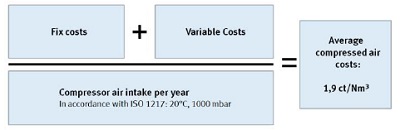
Compressed air costs are normally expressed in Nm³ (at 1.0 bar and 20 °C, according to ISO 6358 or, for many compressor manufacturers, in m³ according to ISO 1217:2009, Annex C). These can be determined using the sum of fixed and variable costs and using the annual delivery output of the compressor station (see Figure 1).
Annual fixed costs include –
- Depreciation of the investment made
- Interest rate
- Space utilisation costs
Variable costs are made up of –
- Energy costs over the full-load periods and no-load times of the compressors
- Costs p.a.of consumables such as oil, coolant etc.
- Maintenance costs
Calculating the average costs of compressed air generation
In practice, the range of values for compressed air costs is between 1.5 ct/Nm³ and 2.7 ct/Nm³. The high fluctuations depend on many factors, the most important being –
- Electricity costs (per kWh)
- Specific output of each compressor, i.e. of the type used
- Use of an intelligent global control system
- Size of the company / of the compressors
- Atmospheric conditions (density) of the air drawn in
The average price of compressed air for a system pressure of 6 bar rel. can be estimated as 1.9 ct/Nm, based on the following assumptions-
- Generation costs of 120 Wh/Nm³ (for 8 bar rel.at the compressor)
- Electricity costs of 12 ct/kWh
- Ratio of energy costs to additional costs of 75% to 25%
Calculating the individual, plant-specific, costs of compressed air generation
Determining the individual compressed air costs per Nm³ for each compressor station is essential for an accurate analysis of the potential savings. They can be determined very accurately by measuring the electricity requirement and the actual delivery rate. The delivery rates specified in the data sheet are often used for this purpose. However, the actual delivery rate measured fluctuates depending on the intake conditions and should therefore be measured at the same time as the energy consumption.
If it is not possible to carry out a precise measurement the compressed air costs can be roughly estimated. To do this, it is necessary to know the technical data for the compressors, i.e.
- Nominal power [kW] and nominal delivery rate[Nm³/h] at the required pressure level [bar rel.]
- Average utilisation rate of the individual machines#
- Working time in the plant
These values can be used, together with the local electricity prices [€/kWh], to estimate the compressed air costs [€/Nm³] and the annual costs [€] for the amount [Nm³].of compressed air used.
In order to determine costs during productive operation, the following steps must be performed –
- Power consumed [kW], the sum of full-load and no-load power
Full-load power = nominal power [kW] × utilisation [%]
No-load power = 30%× nominal power [kW] × (100% – utilisation [%]),
Note: The actual power is generally up to 30% higher than the nominal power; this can be taken into account when making the estimate. - Delivery rate [Nm³/h] during productive operation
Utilisation [%] × Nominal delivery rate [Nm³/h] - Compressed air index [kWh/Nm³]
(Full-load power + No-load power) [kW] / Delivery rate [Nm³/h] - Compressed air costs [€/Nm³]
(1/75%) × Compressed air index [kWh/Nm³] × Electricity costs [€/kWh]
Note: On average, compressed air costs are made up of 75% energy costs and 25% additional costs. - Annual consumption costs [€/a]
Productive working hours [h/a] × Delivery rate [Nm³/h] × Compressed air index [kWh/Nm³] × Electricity costs [€/kWh]
To get a complete picture of consumption, possible leakage costs that may occur in non-productive operation should be calculated using the same method.
How Do Leakages Occur and What Additional Costs Do They Incur?
How do leakages occur?
Just like standby consumption in electric drive systems, it is not (yet) technically possible to avoid leakages in compressed air systems. However, with today’s technology it is feasible to ensure the leakage rate is at an economically acceptable level – by managing the compressed air medium properly and by continuously monitoring leakages. The causes of avoidable leakages are many and varied.
- Installation and systematic errors such as insufficient or excessive tightening of screws and seals, or mechanical damage, e.g. as a result of rubbing tubes.
- General incorrect handling of compressed air components, e.g. as a result of cutting the tubes incorrectly.
- Wear on the compressed air components.
- Chemical stresses due to operating conditions of the components and caused by incorrectly selected materials
How much do leakages cost?
Even small leakages offer the potential for significant savings. Tables 1 and 2 show how much air is lost as a result of leakages with a specific hole diameter and what additional costs are incurred.
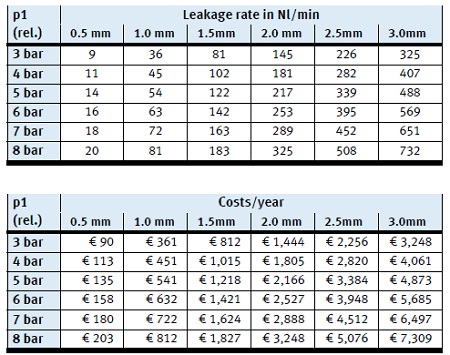
The point at which a leakage is identified as a loss depends on the ratio of leakage to overall consumption. Major leakages – where the air leak is clearly audible – are costly and must be rectified immediately. Medium and small leakages (i.e. with a hole diameter of less than 0.5 mm) are simple to detect using professional leakage detection equipment and should be rectified promptly.
As a rule of thumb, 20% of the detectable leakages in existing systems account for up to 80% of the avoidable costs. It is worth rectifying leakages quickly as every leakage fixed saves energy, and hence costs, straightaway.
Where can potential energy savings be made in compressed air systems?
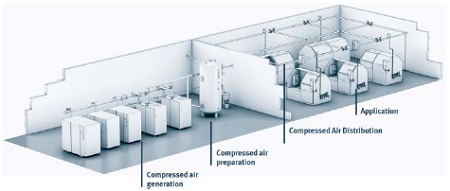
Leakage detection is a fundamental factor in locating potential energy savings. As part of an integrated analysis, all the four areas of a compressed air system (see Figure 4) must be considered, viz.
- Compressed air generation
- Air preparation
- Compressed air distribution
- Compressed air application
The following proposed measures relate to an existing compressed air system which has not been updated in the last five years.
HOW CAN POTENTIAL ENERGY SAVINGS BE IDENTIFIED?
There are various measures for realising potential savings in compressed air systems; these have different effects depending on the particular part of the compressed air system.
First of all, performing a compressed air audit, i.e. a precise analysis of the existing system with a focus on energy efficiency (effective and efficient use of energy), is recommended. In order to develop recommendations for actions that are well thought out, economically speaking, and are designed to exploit potential savings to their fullest, a good audit will examine four different areas: the complete system, compressed air generation, air preparation and actual usage of the air.
It is important that an audit should be adapted to the compressed air system in question, as each system is different and companies’ objectives also vary. The following is a description of what should be taken into account during a good audit, and of its structure.
1. Cost-Saving Measures in Compressed Air Generation Using Energy Analysis
An accurate energy analysis of the compressor station is essential so that a reliable statement can be made about the compressed air costs of the plant or the company, and about the specific potential savings in this area.
Objectives that can be achieved with an energy analysis
- Creating consumption profiles of the compressor station(s), documenting the compressed air requirement, including fluctuations in consumption at different operating times.
- Gathering information about the complete system with its power reserves and identifying opportunities for savings
- Calculating the individual, plant-specific, compressed air costs
Implementation
For the consumption profiles, various parameters of compressed air generation are recorded, some simultaneously, over a relatively long time frame (at least seven days). In particular –
- Electricity consumption of the individual compressors
- Actual delivery rates/compressed air consumption
- Air pressure in the central air reservoir and in the compressed air network shortly before application.
It is important that recording also takes place during downtimes and at the weekend.
A special measuring device is used to determine the consumption profiles. The test probes can usually be installed during operation so that it is no longer necessary to interrupt the compressed air supply for the installation.
Using the measured values, the observed data can now be evaluated and interpreted in a qualitative manner in order to qualify the leaks and create a cost analysis. To do this, the utilisation of the compressors (load/noload cycles per hour), the total leakage volume during downtimes, as well as other variables are calculated.
Popular measures for improvement include
- • Reducing the pressure drops and hence the compressor pressure. (Note: A pressure reduction from 7 bar rel. to 6 bar rel. at the compressor results in an average saving in energy consumption of 6%.)
- • Using a higher-order global control system to minimise no-load losses, and using peak load compressors for significantly fluctuating air consumption profiles.
- • Rectifying leakages at the production hall level.
- • Switching off the compressed air supply.
- • Recovering waste heat.
2. Cost-Saving Measures in Air Preparation Using Compressed Air Quality Analysis
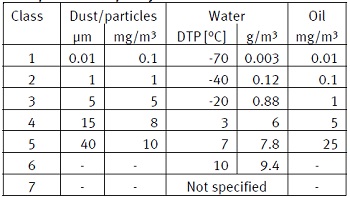
Supplying compressed air applications with optimal compressed air quality is important when it comes to ensuring process reliability. During the air preparation stage, particles (oil, water and contaminants) that are present in the ambient air are removed and the air is compressed into the smallest space possible using a compression process. The compressed air quality is defined in DIN ISO 8573-1 (2010) (see Figure 6).
Components of compressed air applications used in production areas that do not have to comply with high standards require a minimum level of compressed air quality. Well-known manufacturers of pneumatic products such as cylinders therefore recommend an average compressed air quality of 7.4.4 for most of their products (dirt particles max. 40 μm, pressure dewpoint at +3 °C and residual oil content at 5 mg/m³). The same air quality is generally also sufficient for operating quarter turn actuators and linear actuators for process valves. Coarser particles will wash out the life-time lubrication, or cause increased wear and damage to seals. Damage to the seals, corrosion, or blocked cable cross-sections leads to higher costs of both energy and operation. This often results in unplanned production downtime.
To operate position and process regulators, as well as valve control units on process valves, the compressed air is generally subject to higher requirements. Depending on the type of regulator, compressed air qualities of up to 3:4:3 are required (particle size max.5 μm, oil max. 1mg/m³). If the equipment is used in outdoor applications or in unheated storage and production areas, the air must be dried further, depending on the climatic conditions. A pressure dew point of -20°C (class 3) or -40°C (class 2) is standard. This results in a compressed air class of 3:3:3 or 3:2:3.
Compressed air in contact with sensitive products
The requirements of compressed air increase further if it comes into direct contact with raw materials, end products and packaging. This is particularly the case in the food and beverage industry, the pharmaceutical industry and in parts of the fine chemical industry. In the area of dry food and medicine, classes of 2:2:2 or even 1:2:1 can be required. Alternatively, many processes are seeing the application of sterile air, i.e. air that is free of micro-organisms. This is the case in the manufacture of ice cream and in pharmaceutical production. In biotechnological production (fermentation), one application of sterile air is for transferring material between two containers. For the filling of creamy products such as yoghurt, the storage tank of the filling machine is charged with a constant pressure to ensure uniform and reproducible filling.
To prevent the sterile filter from being overloaded the compressed air should be prepared gradually until it reaches a minimum compressed air class of 3:4:1. During the final stage the sterile filter can then remove all the micro-organisms and other particles. If catalysts are used for the preparation of the sterile air, the incoming oil content can be higher. This is because the catalysts degrade all carbon compounds, regardless of whether the matter is living or dead.
Centralised or decentralised air preparation
If large volumes of sterile air are required in production, the ratio of sterile air to overall air consumption must be determined. In some pharmaceutical plants, entire sections, including process valve actuators and other pneumatic consumers, are supplied with sterile air to minimise risk and for the sake of convenience. This reduces the installation costs that would be incurred with two separate compressed air systems, but drives up the operating costs. Leakages also have a major impact on the costs per m³ of sterile air.
The following objectives can be achieved with a quality analysis
- Checking the compressed air quality and adapting to the required conditions or quality classes, if required.
- Avoiding machine failures.
- Reducing maintenance costs.
- Increasing the service life of compressed air components.
Implementation
- Measurement of water and residual oil content after centralised and decentralised air preparation.
- Determination of the pressure dew point and water content with regard to the absolute air pressure.
- Visual inspection of decentralised air preparation at the point of usage.
- Documenting and evaluating results.
- Identifying measures to improve the compressed air quality, e.g. by using filters or decentralised absorption dryers.
Special measuring devices, such as those produced by the authors’ company, are required to carry out a compressed air quality analysis.
3. Cost-Saving Measures For The Complete System, At The Production Hall and System Level, Using Leakage Detection and Elimination
Systematically identifying leakages in the entire compressed air system and eliminating them makes a major contribution to reducing compressed air costs. Detecting and eliminating leakages is above all recommended for existing, relatively old, systems. Both experience and a range of studies have shown that it is in older systems, in particular, that the greatest potential savings can be made – and are also easiest to find. The integration of sensor technology (for pressure and/or flow rate) into air supply units enables an automatic leakage management system with remote maintenance to be installed.
Implementation
- Systematic check of the complete compressed air system at the production hall and system level.
- Classification of leakages found according to leakage volume, and marking them.
- Documentation of the leakages with all relevant data for leakage elimination, e.g. necessary spare parts, estimated repair time, etc.
- Creation of a plant-specific action plan for leakage elimination.
- Leakage elimination.
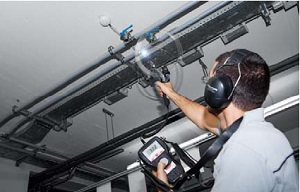
Leakage detection is carried out using ultrasound detectors and can usually be performed during operation. This special equipment is needed so that even small leakages are audible during operation.
In most companies, leakage detection is performed by an external service organisation. The professional service providers will collect detailed data during this, so that the leakages can then be eliminated quickly and systematically.
Ideally, the observed data obtained from everyone involved – including maintenance personnel, operations and plant managers – should be made available centrally via a database, where all measurements are documented. These can also be used for evaluations and periodic comparisons.
4. Cost-Saving Measures
Compressed air consumption analysis
Knowing the compressed air consumption of the production hall – and hence of each machine – is a vital prerequisite for optimally designing and configuring the compressed air supply and distribution at the system level.
An optimal configuration of the piping and tubing in the system, and providing components for decentralised air preparation, help –
- to avoid pressure drops caused by a shortfall and the associated reduction in productivity,
- to put an end to unnecessary energy consumption due to oversupply.
The latter issue arises when the control pressure in the decentralised air supply unit is too high if, for example, there are excessively high flow resistances in the system, or if too many filter stages are being used without producing the required compressed air quality.
A further advantage is that if the consumption of each individual system is known, then sizeable deviations from standard consumption act as early warning signs, e.g. of an existing or developing fault.
Objectives
- To determine the actual compressed air consumption of individual machines as a basis for the optimal design of the compressed air supply to the machine.
- To determine the leakage loss of individual machines.
- To determine various characteristics in order to provide comparability over a relatively long period and lay the foundations for system monitoring.
Implementation
- Measurement of the exact consumption of compressed air by individual machines and applications during both downtime and operation.
- Analysis of various characteristics, viz.
- Consumption per machine cycle,
- Average consumption per minute,
- Average pressure,
- Max./min. pressure,
- Max./min. air flow rate.
- Evaluation and documentation of the measurement results.
Here too, special measuring devices are used. The measured data must be stored for subsequent evaluation.
Machine energy efficiency analysis
In addition to data from the compressed air consumption analysis, the following information must be collected so that the energy efficiency measures can be precisely evaluated and determined-
- Compressed air components (in particular air nozzles, sealing air) and pneumatic drives used,
- Sizing of components and connecting components,
- Technical requirements of the application (force, speed etc.)
A systematic review of the systems’ energy efficiency (i.e. each application’s usage of compressed air in line with demand) must be carried in order to identify economically worthwhile and technically feasible optimisation measures.
Objectives
- To analyse compressed air applications for possible energy optimisation potential.
- To identify worthwhile and technically feasible optimisations.
- Identification and analysis of compressed air applications pertinent to energy use.
Implementation
The twelve energy efficiency measures shown here are helpful. These can be implemented, and should at least be considered, for all compressed air systems and also for systems with electric drives:
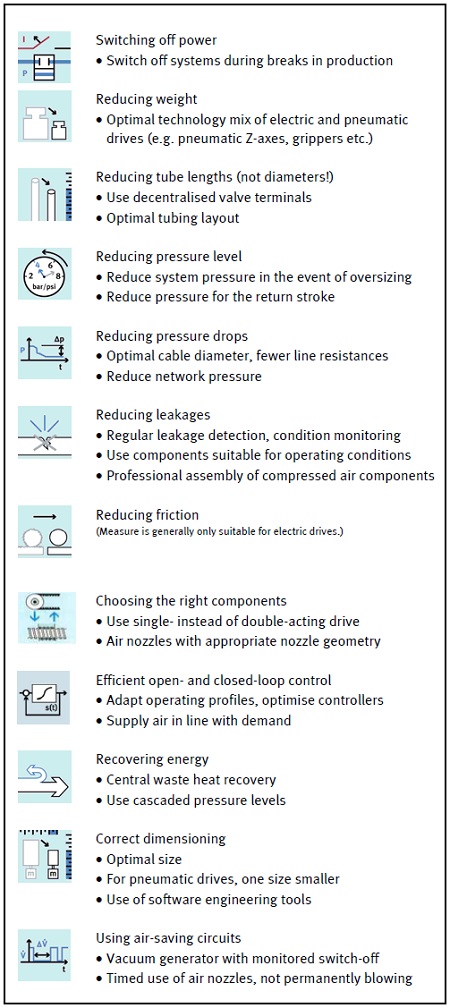
WHO SHOULD TAKE WHICH ENERGY EFFICIENCY MEASURES?
There is no universal answer to this question. The measures must be defined individually for the respective plant or company. Which measures are worthwhile depends on various factors, such as the state of the compressed air system, the extent of utilisation, etc. In the area of machine energy efficiency analysis, these are directly dependent on the application. Moreover, the individual measures should always be reviewed in relation to the total consumption in order to ascertain the economic efficiency of a particular optimisation measure.
A good provider will first of all ask the customer for their requirements and objectives, and then start by determining, in consultation with the customer, the top three measures in consultation with the customer.
In our own organisation this takes places as part of a ‘pre-audit’, during which, the basic data is determined to build up a picture of the status of the compressed air system. The needs of the customer are thus identified and any further approaches or measures can be planned accordingly.
HOW QUICKLY WILL THE COST-SAVING MEASURES BE AMORTISED?
Based on experience, amortisation periods are usually between one and two years. In most energy saving projects the return on investment (ROI) was achieved within this timeframe. The deciding factor for a quick ROI is the prompt implementation of the measures identified.
HOW CAN THE SAVINGS BE GUARANTEED IN THE LONG TERM?
Once a compressed air system has been optimised and brought up to date, it is important to safeguard its energy efficiency and hence the cost-efficiency. There are two ways to do this.
On the one hand, by arranging service and maintenance contracts, e.g. regular leakage detection, compressed air quality analysis, maintenance of individual machines. A difference is generally made between –
- preventive maintenance (tightening fittings, lubrication),
- inspection (checking for damage), and
- corrective maintenance (replacing components).
Alternatively, there is the option of transferring know-how from the service provider to the company in question by suitable training. This way, knowledge can be built up and secured within the company.
WHO CAN IMPLEMENT THE COST-SAVING MEASURES?
To make the most of the potential savings that have been established, it is recommended that the identified measures are carried out promptly. This is because every day represents a cash saving. However, there are often not enough resources available for a company to implement all the measures in-house. In many cases staff do not have enough time, or the necessary measuring devices and corresponding know-how are not available. The measurement results must be interpreted correctly, spare parts sourced, and replacements identified for products that are no longer available. In brief, many different aspects have to be borne in mind to get close to the optimum in terms of energy conservation.
It is helpful to have a partner who is familiar with compressed air systems and the latest technologies and has the corresponding knowledge. Ideally, the service package includes all services – from audit, through engineering, right through to implementing the optimisation measures and providing staff training. The service package should be certified (e.g. in accordance with ISO/DIS 11011). This ensures that suitable and qualified measurements for energy saving are performed.
SUMMARY
An integral approach to optimising energy usage in a compressed air system has a range of benefits for its operator, viz.
- Reduction in energy costs and, as a result, in operating costs,
- Reduction in costs for maintenance and servicing,
- Increase in process security,
- Reduction in unplanned production downtime and associated costs,
Which measures will be worthwhile depends on the circumstances and on the operator’s objectives. However, numerous studies and research projects have shown that leakage detection and elimination are in particular, a low cost way of making a significant contribution to reducing compressed air costs [2, 3]. Like any other technology, compressed air systems are efficient if they are used and maintained professionally
A PRACTICAL EXAMPLE
Customer: Global food manufacturer.
Measures: Leakage detection and elimination at plant level.
Initial situation
- Plant: approx. 50,000 m²
- Installed compressor output: 410 kW
- Compressed air consumption: 40 m³/min
- Production hours: 8,000 hours/year
- Compressor pressure: 6 bar rel.
- Compressed air consumption: 16,475,000 m³/year
- Average price for compressed air: 1.8 ct/m³
- Compressed air costs: € 295,000/year
Result of a compressed air audit
- Identified leakages: 296
- Total compressed air loss:1.63 million m³/year
- Leakage loss: € 29,265/year
- Reduction in annual CO2 emissions: approx. 160 t
- Total project costs (including spare parts): € 31,000
- Reduction in compressed air costs: 10%
- Saving in euro: 29,265/year
- Amortisation time: 13 months
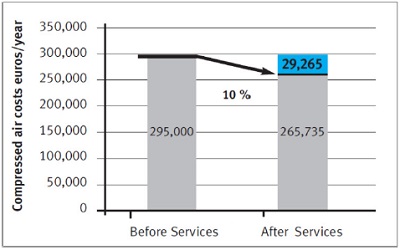
REFERENCES
- EnEffAH project, Energy efficiency in production in the drive and handling technology field, (2008-2012).
- Study, Compressed air systems in the European Union, Fraunhofer Institut ISI (2000).
- Research project, Innovation Alliance Green Carbody Technologies (InnoCaT). Fraunhofer Institut IWU (2013).
Juergen Billep juergen.billep@festo.com
Heiko Fleischhacker heiko.fleischhacker@festo.com