ABSTRACT
A case study is presented of the measures adopted when a primary air fan in a coal-fired power plant exhibited, after maintenance, high vibration which led to failure of the motor bearing and eventual stoppage of power production. The measurement of the vibration, the solution of the problem and the message for the maintenance team are discussed.
Introduction
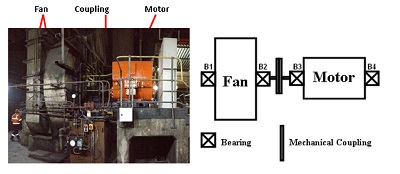
EDF’s West Burton plant is a 2000 MW power generating station, commissioned between 1967 and 1969, and comprising four similarly configured Boiler and Turbo-generator (TG) sets. Each boiler has two primary air (PA) fans used for supplying primary air to the mills and then conveying pulverized fuel into the boiler unit. These fans are generally considered as one of the most critical auxiliary equipments of the generating unit, owing to the fact that operational faults on any of the fans will eventually result in a shutdown of the entire generating unit. Hence the continuous monitoring of such critical machines – in order to detect emerging operational defects at their early stages – is of immense importance. These PA fans are 10-bladed, supported by two journal bearings and driven by 1.2 MW induction electric motors which are also mounted on two journal bearings. Figure 1 shows a typical fan-motor unit and its schematic
Re-Assembly and Vibration Problem
In July 2012 West Burton Unit 3 was taken to a major outage, and when it came back to service in November of that year a high level of the overall vibration readings at the PA fan, bearings, in both vertical and horizontal directions, was recorded. The machine vibration levels were therefore closely and continuously monitored for a period of approximately 16 months (November 2012 to March 2014).
The trend of overall RMS velocity of the vibration at the motor drive end bearing (B3) in the horizontal direction is shown in Figure 2, where it is clear that the change in the vibration is significant after maintenance and re-assembly activities during the outage. As per the ISO 10816-3 code, the allowable and satisfactory vibration limits should be 2.3mm/s (RMS velocity) and 4.5 mm/s (RMS velocity) respectively for this machine, assuming the rigid foundation.
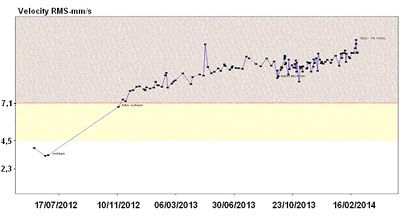
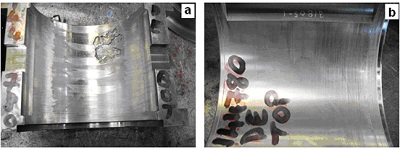
The vibration level was just close to the satisfactory limit before the outage in July 2012. However, it became close to an unacceptable limit (above 7.1mm/s RMS velocity) as per ISO 10816-3 codes. Figure 2 clearly shows the increasing trend in the vibration in November 2012. It is the impact, over the period of fan operation, of this high vibration on the bearings and the fan assembly that led to the failure of the drive end motor bearing, the stoppage of TG Unit 3 in February 2014 and hence the loss of power production. A typical failed bearing of the motor is shown in Figure 3.
Vibration Spectrum Analysis
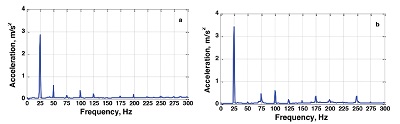
The motor was put back into operation after replacing the faulty motor bearing in March 2014. The vibration measurements, in both vertical and horizontal directions, were carried out after this correction on 24th March 2014, at all four bearings and at its normal operational speed of 1500RPM (25Hz). Once again the overall RMS vibration velocity was found to be 11.7 mm/s. Figure 4 shows typical vibration acceleration spectra at the motor drive end bearing (B3), in both vertical and horizontal directions. It is clear from the spectra that there is a dominant peak at rotating speed 25Hz (1x) followed by small amplitude peaks at the higher harmonics (50 Hz (2×), 75 Hz (3×), 100 Hz (4×), etc.). There is no significant peak at the blade passing frequency of 250 Hz (10×, i.e. the fan speed of 25 Hz times the number, 10, of fan blades). This clearly indicates a case of rotor unbalance.
Investigation and Correction
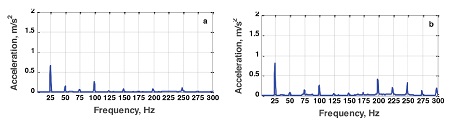
The fan unit was thoroughly investigated and no obvious reason for the high vibration was observed. In-situ modal testing also confirmed that there was no possible source of resonance at 25Hz that would result in high vibration. The closure on the coupling element between the motor and fan shafts may not have been perfectly balanced and so its position might have introduced large rotor unbalance. The coupling was therefore step-by-step rotated during the coupling assembly process in order to observe the impact of this on the rotor balancing and vibration, an impact which was found to be significant. An optimum coupling rotation, determined from this exercise, gave a satisfactory result. The overall vibration reading came down to nearly 3 mm/s (RMS velocity), which was within the satisfactory limit as per the ISO 10816 codes. The measured acceleration vibration spectra, shown in Figure 5, also exhibited significantly reduced vibration at 1×.
Concluding Remarks High vibration (which may lead to failure and plant shutdown) caused by the re-assembly of a machine after maintenance is not unknown, and has been demonstrated in this case study of the re-assembly of an auxiliary machine, a PA fan, of a generating unit. The failure of the machine resulted in stoppage of the complete generating unit and hence loss of power production, incurring an estimated average loss of approximately £200k per day. In this case it was recommended that the maintenance team be made generally aware of this kind of impact and, so that they can re-assemble machines correctly, they should benchmark them before dismantling for maintenance and repair.