ABSTRACT
In this economic downturn many businesses are struggling to survive and have a healthy bottom line. A cost reduction programme for their facilities, to offset increased manufacturing costs, may therefore be essential. Apart from the raw materials, the major consumers of these costs in a paint plant are energy, water and industrial waste disposal. Proven cost reduction strategies, focusing on these cost elements, are presented. The objective has been to identify some of the cost reduction opportunities (the majority of which have a payback period of less than six months, require small capital investment and make efficient use of resources) which the business can address to enhance its profit margin. Here, the focus is on energy optimization programmes, and it is concluded that significant savings are achievable through their implementation.
INTRODUCTION
The Valspar Corporation is one of the largest coatings manufacturers in the world. It manufactures large scale paint and resin and is a major supplier of coil coatings, food and beverage container coatings, general industrial finishes, and resin and gelcoats for the composite industry. Due to the global financial crisis many businesses are heavily affected and are struggling to maintain profits. As a result cost reduction has become a constant focus for businesses around the globe.
As we are a US- based company this economic turmoil has heavily impacted our business, and. implementing a cost reduction programme has become a top priority. With the cost of energy, water and wastewater disposal spiraling upwards any means of reducing cost and conserving resources is worthwhile considering. These costs can be easily reduced by a significant margin, simply by efficiently utilizing resources, eliminating the wastes and more thoughtfully managing the processes.
There are many reasons why a company needs to reduce its manufacturing costs, and particularly its energy cost, viz. to –
- Eliminate unnecessary expenses or wasteful spending.
- Increase company value.
- Increase profit margin.
- Conserve resources.
- Increase productivity competition
- Reduce plant maintenance cost.
- Achieve longer plant service life.
- Avoid emissions, including greenhouse gases, through energy conservation.
COST ELEMENTS
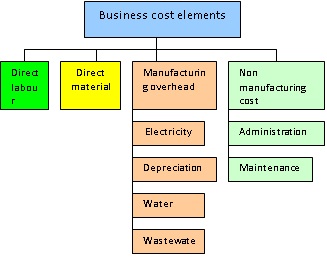
Typically, there are four categories of cost involved in a manufacturing facility, viz. direct labour, direct material, manufacturing overhead and non-manufacturing cost. The focus here will be on manufacturing overhead costs. Manufacturing cost refers to any cost that a company incurs to make product. Manufacturing overheads in our own facility include the costs of depreciation, electricity consumption, water usage and wastewater disposal (see Figure 1).
COST REDUCTION STRATEGIES
A company which does not have a firm and clear strategy to overcome increased manufacturing cost will eventually lose its competitiveness and be driven out of business. The main objective of cost reduction is to maximize profitability. A cost reduction strategy will enable the company to be more economical, by identifying the numerous opportunities available and their potential benefits.
This paper will present the cost reduction opportunities within the manufacturing overheads of our own plant and will include those of energy, water consumption and wastewater disposal. Cost reduction can be achieved through elimination, reduction and modification of manufacturing activities.
ENERGY CONSERVATION AND COST REDUCTION OPPORTUNITIES
In the current challenging economic conditions it is vital for businesses and individuals to reduce energy cost. With today’s ever-increasing pressure to protect the environment, our responsibility to optimize energy usage and efficiency is greater than ever. Climate change is the most important environmental issue facing the world today and it is well-recognized that our use of energy is one of the key contributors to this issue. Reducing energy usage not only benefits a company economically but also reduces greenhouse emissions. Reducing energy simply means using it more efficiently, i.e. by eliminating its unnecessary use.
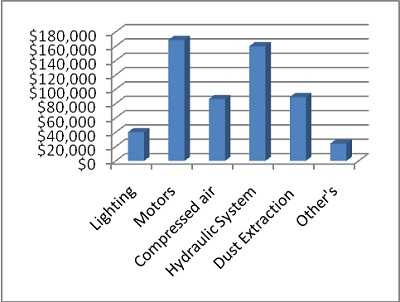
Energy plays an important role in industry and with its increasing cost there has been a search for cost reduction ideas and methods. Reduction in energy bills can be achieved through proper monitoring and optimisation of equipment. Energy cost is one of the major elements of our own manufacturing overhead, the distribution of energy usage in our plant being shown in Figure 2. The total cost of our company’s energy consumption is approximately $567,962, the major part of which is spent on the compressed air system and motors. Many plausible opportunities for reducing this have been identified..
COMPRESSED AIR UTILISATION
Typically, 20 – 23% of the energy cost incurred in a manufacturing unit is that of compressed air. In a compressed air system leaks are a significant contributor to wasted energy. The system at our own facility consists of two rotary screw compressors and a refrigerated air dryer, viz.
• Kaeser rotary screw compressor. Model DSD 141. Variable speed motor drive. Rated capacity 13.62 m³/min.
• Kaeser rotary screw compressor. Model CSD 121. Variable speed motor drive. Rrated capacity 12.01 m³/min.
• Refrigerated air dryer.
The operating pressure for the compressed air system was set at 700kPa, the minimum required being 650kPa, showing that there was a significant air loss due to leaks. One of the most fundamental ways of improving the efficiency of any compressed air installation is to reduce such leakage. Leaks in compressed air lines should be repaired and there should be regular maintenance on the compressed air system. Many plants run at unnecessary high pressure, wasting energy and increasing running cost. on On our own site compressed air is regularly used for a number of applications, including pumps, actuators, pneumatic cylinders and machine tool drives. A compressed air utilisation programme, via the following steps, has been effectively implemented.
Leak detection
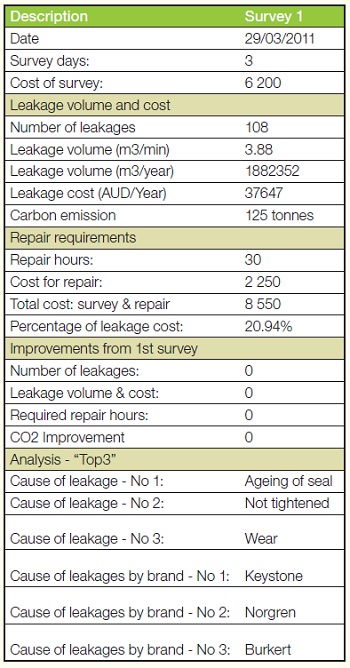
A leak survey on the compressed air system, taking three days (at a cost of $6200) to complete, was conducted by Basil VR Greatrex. All the identified leaks were tagged according to their size. The results are shown in Table 1.
- 48 category 1 leaks (<0.3mm Inaudible)
- 16 category 2 leaks (<0.3 – 1mm Audible)
- 44 category 3 leaks (>1mm Serious)
- Wasted energy cost approximately $37,647
- All the identified leaks were tagged according to its category.
- Part list for the repairs were provided
Energy consumption monitoring
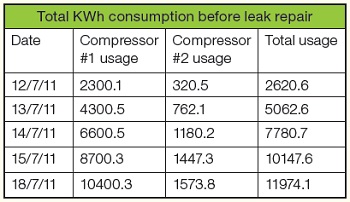
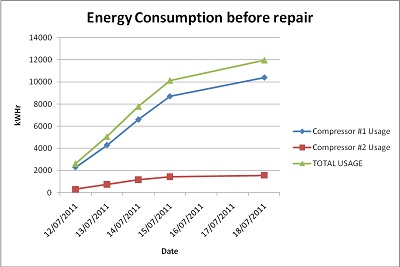
Kilowatt-hour meters were installed, at a total cost of $500, on both the compressors, to monitor the energy consumption before any repairs to the air leaks were conducted, and one week of energy consumption data was collected. The average for the five days was 11,974.4 kWh, equivalent to approximately 684,936 kWh per year, costing $83,905 @ 12.25c/kWh (see Table 2 and Figure 3).
Leak repairs
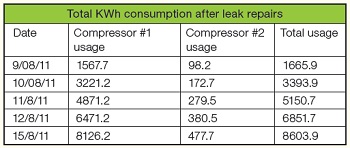
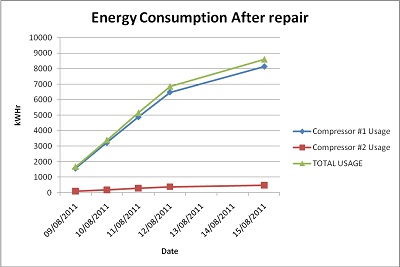
After determining all the air leaks on site, and the cost of energy consumption of the compressed air system, repairs to the leaks (which took two days to complete) were conducted by Basil VR Greatrex at a total cost, including parts and labour, of $9,934. Energy consumption was then monitored for a week and showed a reduction of 28 percent (see Table 3 and Figure 4).
Reduction of system operating pressure
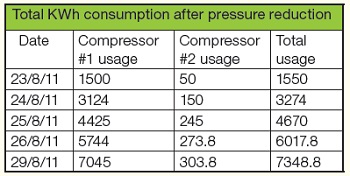
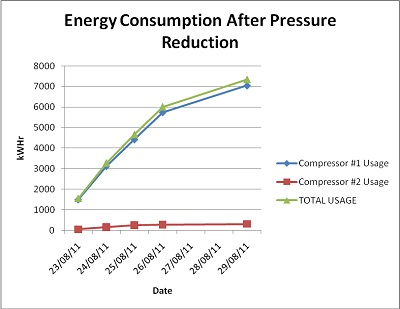
System operating pressure and energy consumption are directly related. Operating pressures at levels greater than the requirement only increase the energy usage. Reducing pressure not only saves in energy bills but also provides other benefits such as reducing leakage rates, increasing system capacity and extending service life of the equipment by reducing stress.. The system operating pressure was reduced from 700kPa to 660kPa one week after the leak repairs. Again the energy consumption was monitored for a week (see Tables 4 and 5 and Figure 5).
Anticipated benefits from compressed air leak management programme.
- Potential energy savings of $32, 414
- Reduction of 125 tonnes of carbon emission
- Reduction in compressed air running cost
- Increase in equipment service life
- Resource conservation
- Payback period of the programme: 3 months
HYDRAULIC SYSTEM UTILISATION
The hydraulic system comprises two Vickers PVH piston pumps operating in parallel, each delivering 380L/M. The system provides rotational power to the reactor stirrers, mixers and pumps on site. Each pump is driven by a 132 kW electric motor consuming approximately $160,000 of energy annually. The pump pressure is controlled according to the demand from the SCADA system by setting the values which range from 0 – 100 percent. The optimum system pressure to efficiently operate the system is 120bar. Due to its operating characteristics the system occasionally operates at higher pressure than needed when the demand decreases, and requires operator interaction to lower the set point. Unnecessary energy is consumed as a result. It has been identified that approximately 50% of the time the hydraulic system requires its full load.
Cost reduction opportunity
The two hydraulic pump sets don’t need to be operated at the same time. The proposal is to reprogramme and fully automate the system so that:
- The system pressure would be set at 120bar at all times, so no operator interaction would be required. The pump pressure control valve will modulate according to the set pressure.
- The first pump would be on duty at all times.
- The second pump would kick in when the first pump reached 80 percent of its load (300L/M).
- The second pump would stop when the plant demand reduced to 290L/M.
The overall cost of programming, parts and changeover would be approximately $6,000.
Anticipated savings and benefits
- At least 50% reduction in the cost of energy for the hydraulic system could be easily achieved, which would equate to approximately $80,000 annually.
- Pump and motor service life would be significantly increased as a result of not being on full load at all times.
- Currently, the pumps are refurbished annually, costing over $25,000. The maintenance cost would probably be reduced by implementing the proposed changes.
- The hydraulic system reliability would be significantly improved.
INSTALLATION OF A VARIABLE SPEED DRIVE ON THE COOLING TOWER FAN MOTOR
An EWK1260 Superchill cooling tower, with a flow rate of 252L/M, dissipates process heat into the atmosphere. The tower fan is operated by a 15kW fixed speed motor and a kilowatt- hour meter was installed to determine its energy consumption, which was determined to be 132,141 kWh , equating to $16,187 annually. The cooling tower was originally designed on the basis of a wet bulb temperature of 24oC and plant heat load of 3,224kW. Over the years the plant has been downsized by at least 10%, which has meant that there is less heat load compared to that of the original design. The plant is also normally operating at a reduced capacity of at least 70%, further reducing to 50% during the night shift. The wet bulb temperature is an important factor in the performance of the cooling tower. Every time the actual wet bulb temperature is lower than the design figure an energy saving potential exists. The maximum cooling water temperature required by the manufacturing process is 24°C. This goes as low as 15°C during winter, wasting unnecessary energy for the additional cooling.
Installing a variable speed drive on the electric motor of the cooling tower fan would reduce drift and save significant amount of energy. Such a drive would allow the cooling tower fan to run at whatever speed is required to meet the cooling demand. Daily and seasonal changes in the ambient wet bulb temperatures will allow the fan speed to be modulated, reducing energy consumption. It is concluded, from the facility’s operating condition and from feedback from the cooling tower manufacturers that an average of 50% energy reduction could be achieved by installing a variable speed drive. The cost of this would be approximately $5,000.
SHUTTING DOWN EQUIPMENT WHEN NOT NEEDED
The simplest way of reducing energy cost is to shut down equipment when not needed. There are several equipments on site which are unnecessarily operated, i.e. even when not required.
Main dust collector
The main dust collector has a 75 kW motor operating 24 hours a day. It is used for extracting dust when loading the reactors or the high speed mixers. It consumes approximately 605,649 kWh ($74,192) of energy annually. A survey revealed that it does not need to be in operation when there is no powder loading activity, which is for approximately 50% of the production time. An energy saving of $37,096 could be easily achieved by shutting it down atv such times.
Level 1 dust collector
This collector has a 5 kW motor and a 10 kW motor, consuming approximately $14,838 of energy annually. It is used while loading mixers on Level 1. The paint plant is the only user of this equipment and they do not operate during the night shift. There is a potential for saving at least $4,496 by shutting the equipment down during the night shift and restarting it at the beginning of the day shift.
Stairway pressurised fan
This is driven by a 3 kW motor which operates 24 hrs a day throughout the year. It consumes approximately $3,777 in energy annually.. The stairway needs to be pressurised during emergency fire evacuation and does not require to be running at all times. The proposal is to link the fire evacuation alarm to the fan motor starter so that it will only start when fire alarm is activated. This would bring a saving of $3,777 annually.
WASTE WATER COST REDUCTION
The manufacturing process generates a significant amount of waste water, costing the business approximately $800,000 annually. This cost comes mainly from the compressed air condensate disposal, industrial waste disposal and forklift scrubber tank water disposal.
Compressed air condensate cost reduction
The compressor units generate approximately 73,000 litres of condensate annually. This is disposed offsite as waste water due to the oil contamination, costing a total of $26,900 in disposal and handling cost. An oil separator has been installed to remove the oil so that the waste water complies with the EPA requirement before discharge into the sewer line. The cost of the equipment needed, and of its installation, was $3,136. The payback period for this project is 1.4 months, and the annual savings $26,900.
Forklift scrubber tank water cost reduction
The site has ten flameproof forklifts. Each has a 40L scrubber tank attached as part of the flameproofing. . Each day, the tank is emptied and refilled with new water, which is part of its service requirement. A total of 100,000 litres of water is thus discharged, which is then disposed as wastewater, costing the business approximately $35,000 in disposal and handling cost. The water mainly has carbon deposits, so the proposal is to filter the water before discharge to the sewer line. The cost of the filtering unit is approximately $5000, which would bring a potential saving of $35,000 annually. The payback period for this proposal would be 1.7 months.
WATER CONSUMPTION REDUCTION
The provision of water incurs one of the major costs in most manufacturing plants. Our own operation consumes a total of 15,292 kilolitres of water annually, costing $44,304. Most of it is used in the manufacturing process, e.g. in providing de-ionized water, for cleaning vessels and for cooling. It is surprising to know that a significant amount of water is used for toilet flushing. There are 14 toilets on site and they are all single flush, consuming 13L per flush – or approximately 1,690 kilolitres (at cost of $3,380) annually. Water conservation is the most cost effective and economically sound way of reducing our demand for water. Saving water also means saving the energy needed for its pumping and treatment.
The proposal is to replace all the single flush toilets to dual flush. A dual flush toilet consumes an average of five litres per flush. The cost of the changeover would be approximately $4200 (with a payback period of 2 years). The anticipated savings from this would be:
- An annual saving of 1,040kL of water consumption.
- An annual saving of $2,080 in the water bill.
SUMMARY OF COST REDUCTION STRATEGIES
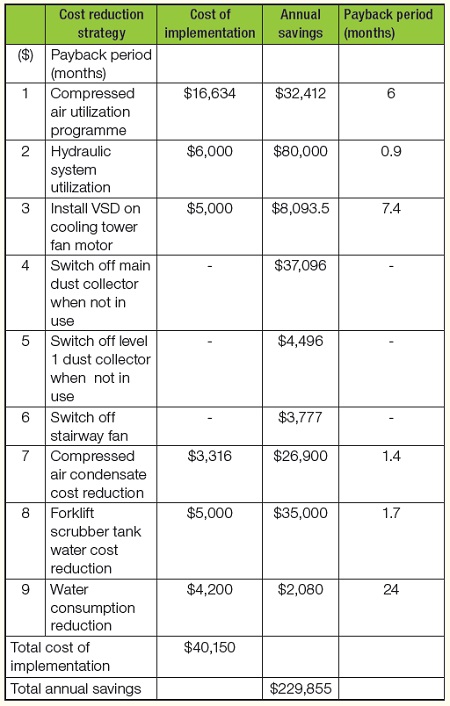
The total cost of the initial capital investment required for the proposed cost reduction changes is approximately $40,150, which would be capable of generating an annual saving of $229,855 (see Table 6).
CONCLUSION
Effective cost reduction programmes are essential for an organization to survive and grow. The proposals presented require small initial capital investment with a potential for considerable savings. Some of the proposals do not require any capital investment and can be easily adopted as steps towards improving the business profit margin. Cost reduction strategies not only financially benefit the business but also ensure conservation of resources for future generations. The average payback period of the proposed cost reduction ideas presented is approximately four months.
FURTHER READING
1. Studebaker J M, Maximizing eEnergy savings and minimizing cost. Fairmont Press, 2002.
2. Bannister K.E, Energy reduction through improved maintenance practices. Industrial Press: New York, 1999.
3. Burger R, Cooling tower technology: Maintenance, upgrading and rebuilding, 3rd Edition. Prentice Hall, N.J, 1998.
Authors’ contact details
Indra Gunawan,
School of Applied Sciences and Engineering,
Monash University, Gippsland Campus, Churchill, VIC 3842
Ajay Karan,
Maintenance Engineer, Valspar
Email: ajaykaran_01@yahoo.com.au