ABSTRACT
A very brief insight is given into a value improvement model (VIM) for repetitive processes applicable to any business improvement project where people and/or plant provide a service to support the overall business objective. Arguing that competitive advantage can be realised through the different amalgams of productive and strategic resources, the VIM focuses on aligning resource bundles (people and plant) and any influencing factors creating efficacious, efficient and effective processes applying Lean and Six Sigma holistically. A case study, using a simple Scalextric track assembly process, is used to demonstrate the VIM application. Readers can use the VIM in their businesses as a visual and systematic framework that enables them to understand, assess and improve their repetitive processes.
DEVELOPING A VALUE IMPROVEMENT MODEL FOR REPETITIVE PROCESSES
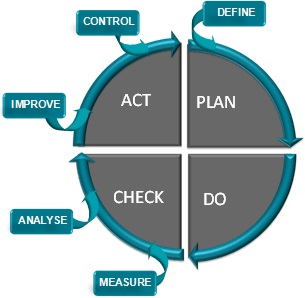
Developing a value improvement model for repetitive processes, Figure 1 shows a proposed framework providing a structured approach to sustainable value improvements building on the Six Sigma DMAIC (Define, Measure, Analyse, Improve and Control) and Deming/Shewhart PDCA (Plan > Do > Study/Check > Act ) cycles. Of interest here is the original Shewhart Cycle discussed by Deming where the four step PDCA cycle has a fifth step defined as ‘Repeat Step 1, with knowledge accumulated” and a sixth step defined as “Repeat Step 2, and onward’. This continuous knowledge accumulation cycle allows for better understanding of the process to be improved, rather than being a one-off improvement perhaps found in the linear and sequential Six Sigma DMAIC improvement process.
Figure 1 also shows how the PDCA and DMAIC improvement can be structured to complement each other; DMAIC is added to the continuous cycle of PDCA and the PDCA cycle is enhanced by the framework provided by DMAIC. The proposed value improvement cycle takes the following steps based around seven Ps: Purpose, Perspective, People, Plant, Product, Performance and Process.
1. Define: Understand what the Purpose of the investigation is from the Business’ Perspective? Quantify the change required to the Process, perhaps using the Six Sigma project charter approach.
2. Plan: Understand how the resource bundles of People and Plant are aligned to deliver the customer needs detailed in the Product description.
3. Do: Run the repetitive Process to deliver the Product.
4. Check/Measure: Understand the outcomes of the repetitive Process and measure Performance.
5. Analyse: Analyse the Performance comparing the actual outcomes against those specified by the Product, quantifying examples of waste (Lean) and process variability (Six Sigma) against the customer Perspective (Product) and business Perspective (Purpose).
6. Improve/Act: Change the Process inputs based on the outcome analysis.
7. Control: Put in place control mechanisms to ensure the Process changes are sustained.
8. Define 2: Start again revisiting the Purpose and Perspective.
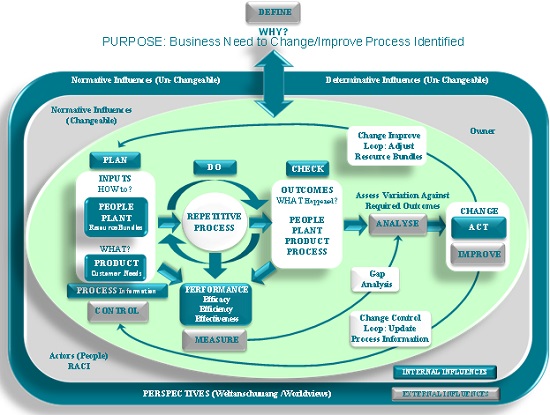
Developing a conceptual framework to operationalise the model in a practitioner environment, Figure 2 introduces the generic VIM (g-VIM) for repetitive processes that has been used successfully in both service and manufacturing industry. The internal elements on the g-VIM focus on measuring/analysing an outcome based on a requirement and feeding back improvements and updating process controls. This could be classified as hard systems thinking, which was developed to solve real-world problems during and after World War II. Although proven to be very useful, hard systems thinking has received considerable criticism focusing on limitations when understanding complexity, politics, plurality, beliefs and values. Looking to overcome these potential weaknesses the g-VIM also takes into account internal and external influencing factors taking a holistic approach encompassing elements of soft systems thinking, in particular the use of the Customer > Actor > Transformation Process > Worldview > Owner > Environment (CATWOE) tool (See Table 1 for a summary of the CATWOE definitions used in the g-VIM).
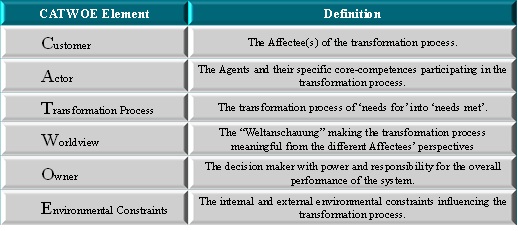
The CATWOE tool used in conjunction with the Six Sigma Supplier > Input > Process > Output > Customer (SIPOC) provides an excellent way of populating the g-VIM with the bespoke elements required to understand the repetitive process holistically and to identify opportunities for sustainable business improvements.
A CASE STUDY EXAMPLE
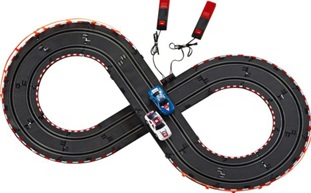
This case study uses a simple manufacturing-based exercise developed to educate personnel in the basic principles of Lean and Six Sigma. The repetitive process chosen is the assembly and completion of single lap of a Scalextric track as shown in Figure 3.
Populating the g-VIM to create a specific value improvement model, Figure 4 shows the Track Build-Off VIM (t-VIM) used to improve the track assembly and lap completion time. Full details of the training course material and delivery approach are outside the scope of this article but the intent is to pitch two teams against each other to prepare the race track to the customer’s requirement (customer = me, product = track layout provided with instructions) and then complete one lap with one car with no unacceptable incidents (crashes). The teams get the chance to improve the assembly and race times as they are educated in Lean and Six Sigma principles and also gain valuable process knowledge.
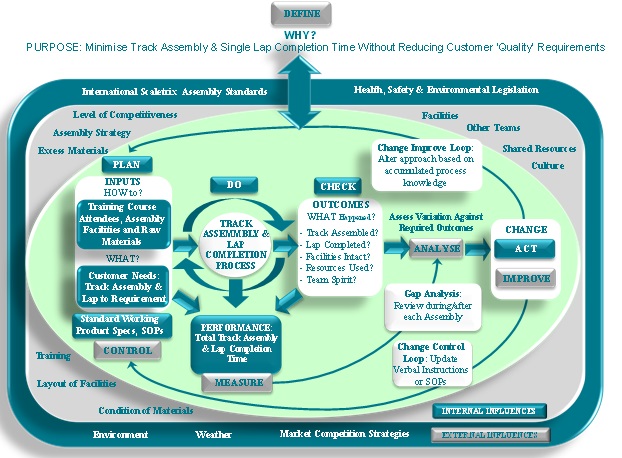
In the t-VIM, the repetitive process has been identified under ‘DO’ as the Track Assembly and Lap Completion Process. Captured under ‘PLAN’ are the direct inputs to the process, which in this case are the Training Course Attendees, the Assembly Facilities and the Raw Materials provided, which are working to the Customer Needs specified as the Track Assembly and Lap to Requirement. The direct Outcomes of the process are captured under ‘CHECK’ and are based on understanding What Happened? Including –
- Track assembled?
- Lap completed?
- Facilities intact?
- Resources used?
- Team spirit?
The level of Performance achieved is Measured against the Total Track Assembly and Lap Completion Time (assumes quality of track build is to specification and lap is completed with no unacceptable incidents).
The next stage is a Gap Analysis reviewed During/After each Assembly and Analysed comparing any Variation Against Required Outcomes. With an understanding of the gap between the required and actual there is now an opportunity to change the process inputs and ‘ACT’ or Improve the repetitive process. The Change Improve Loop adjusts the direct inputs to the process and the Change Control Loop updates any verbal or written instructions, in this instance assuring a level of Standard Working. This is the key part of the value improvement model and any change(s) made must also take into account the influencing factors shown in the Internal and External Influences bands of the t-VIM.
The Internal Influences band shows elements of the process which are not direct inputs but can have a negative or positive impact on the outcomes of the repetitive process and are changeable by the process owner. For example, the Layout of Facilities is a key element which can both positively (if the layout allows for minimal waste and variation during the assembly) or negatively (if the layout means there is excessive waste such as transportation/movement, or high variation due to no dedicated storage or assembly locations). In this example, and probably relevant to all manufacturing processes, a change in layout to optimise a single process could de-optimise another adjacent process, hence the requirement to understand the total consequences of any changes made.
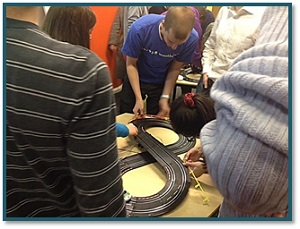
Similarly to the Internal Influences band, the External Influences band shows those elements of the process which are not direct inputs but can have a negative or positive impact on the outcomes. However, the External Influences are un-changeable and outside the control of the process owner although it is possible to engage and try to influence any potential changes required. For example, the Market Competition Strategies (in the simple example, the other team), may negatively influence the process by acquiring all of the raw materials or changing their layout to de-optimise their competitor’s layout. A positive influence is the International Scalextric Assembly Standard which means all of the pieces of track are interchangeable and the standardisation provides flexibility in the assembly process, where all pieces can fit together through a standard sizing and part numbering which can also be used in the assembly SOP. The International Scalextric Assembly Standard could also have a negative impact on the process if it stipulates track and car maintenance regimes which in the eyes of the process owner de-optimise the process.
SUMMARY
The value improvement model (VIM) has been introduced as a useful business improvement approach and a simple case study using a Scalextric track assembly and lap completion repetitive process has been used to demonstrate the effectiveness of the VIM. Previous attendees of the track build-off exercise have managed to reduce the assembly and lap completion time from over 420 seconds to less than 15 seconds in just 4 cycles of the repetitive process (Figure 5 shows the teams during one of the training exercises)! In industry, the VIM has been used successfully to make substantial business process improvements.
If ever you have a repetitive process that needs improving, think about the framework provided by the VIM and apply it to your improvement project. For further details and possible collaborations, please contact Paul Gibbons by email or connect with Paul on Linked In http://lnkd.in/zUntXz